Hi Guys,
I had ordered a Micrometer Saddle Handwheel from Hemingway Kits a few months back and it finally came last week. They order them in small quantities and were temporarily out of stock when I placed my order. However, it was worth the wait. It is by far, the nicest accessory that I have purchased for my Myford Super 7 lathe. The workmanship is just outstanding and the fit and finish are just beautiful. This is the link to the Hemingway page: http://www.hemingwaykits.com/acatalog/Micrometer_Saddle_Handwheel_-_Myford_7_Series.html
The design is by Graham Meek and I believe that the original construction article appeared in the UK publication Engineering In Miniature a few years back. I saw the reprint of the article in The Home Shop Machinist Setember/October 2011 issue and ever since had wanted to fit one to my lathe. It also appears in Graham Meek's new book 'Projects For Your Workshop, Vol.1'. It is a very clever design that utilizes internal gearing to "slow down the dial in relationship to the carriage travel." It is available in Metric or Imperial versions from Hemingway and the construction article provides complete information on building either version. It is a very complete construction article that even documents how to build the tooling to hold and cut the gears. This concept could be adapted to other lathes as well and Mr. Meek provides enough background information on the design that it could be applied to another lathe.
The reason I opted to buy the kit from Hemingway instead of building one is that I have numerous projects that need completion and it would have been quite some time until I could stop to build another accessory for my lathe. The Myford Super 7 lathe has a gap bed which really limits the usefulness of a conventional bed mounted carriage stop. It just doesn't allow the use of one near the headstock where much of the work is done. On lathes without the quick change gear box, there are several tapped holes available for a length stop attachment point, as can be seen on several of Ramon's work in progress photos. With the QCGB, there is precious little room available for a stop, although after doing some research back through Model Engineer and Engineering In Miniature, there have been several very good designs published in the past.
The Micrometer Saddle Handwheel has an adjustable micrometer collar and the graduations on my Imperial version are 0.010"/division and one revolution is 1.000" of linear travel along the bed. (Please see the Hemingway link for more information on accuracy, the Metric version, etc.) The graduations are wide enough that you can easily estimate to 0.005", which works great for quickly roughing a workpiece. It may not be the complete solution to accurate length control on the Myford all alone, but coupled with the usual techniques and my future length stop, I am confident it will do everything that I require of it. This will definitely make my Myford lathe a lot more fun to use and should speed up the machining time on many jobs considerably.
I can highly recommend this kit from Hemingway. Every part is beautifully machined to very high standards. The micrometer collar is ground and the graduations are crisply engraved. When assembled, it can be 'zeroed' very smoothly and the geartrain is silky smooth as well. The installation is very straight forward and the instructions are clear. The only machining required for the S7 is to drill and tap the existing handwheel shaft M5, which the instructions tell you that you can do without disassembling the lathe. Since I regularly (once or twice a year depending on how much cast iron I have machined) remove my leadscrew, saddle and apron to clean them, I opted to disassemble the lathe and remove the shaft which can be drilled and tapped in the lathe with the tailstock. The other important detail is to spend the time fitting the new hub and its keyway to the original shaft. This is just the usual deburring and fitting of parts. However, you want these to fit without interference because the assembly does have to be removed in order to access the apron oil fill plug, which is what is used to secure the new dial backplate to the apron.
Well done Graham Meek and Kirk Burwell from Hemingway Kits! Thanks for a great design and product.
Regards,
Mike
I had ordered a Micrometer Saddle Handwheel from Hemingway Kits a few months back and it finally came last week. They order them in small quantities and were temporarily out of stock when I placed my order. However, it was worth the wait. It is by far, the nicest accessory that I have purchased for my Myford Super 7 lathe. The workmanship is just outstanding and the fit and finish are just beautiful. This is the link to the Hemingway page: http://www.hemingwaykits.com/acatalog/Micrometer_Saddle_Handwheel_-_Myford_7_Series.html
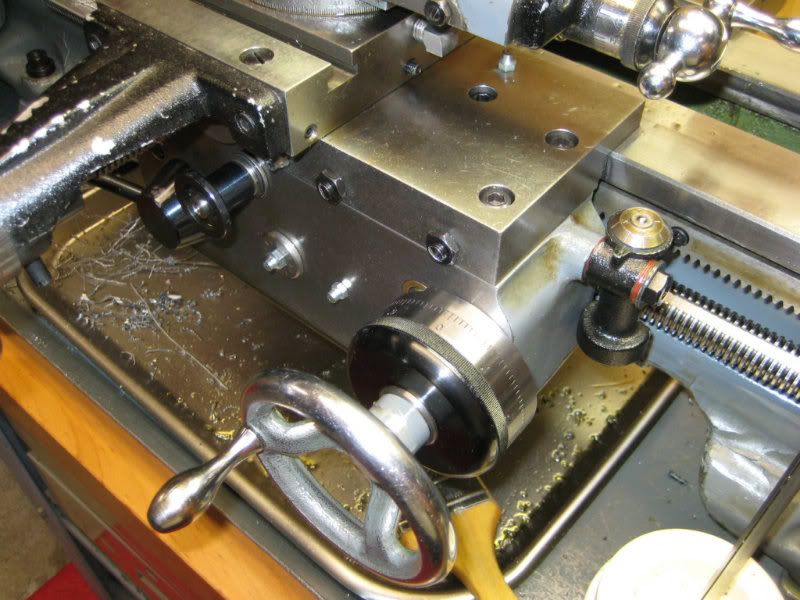
The design is by Graham Meek and I believe that the original construction article appeared in the UK publication Engineering In Miniature a few years back. I saw the reprint of the article in The Home Shop Machinist Setember/October 2011 issue and ever since had wanted to fit one to my lathe. It also appears in Graham Meek's new book 'Projects For Your Workshop, Vol.1'. It is a very clever design that utilizes internal gearing to "slow down the dial in relationship to the carriage travel." It is available in Metric or Imperial versions from Hemingway and the construction article provides complete information on building either version. It is a very complete construction article that even documents how to build the tooling to hold and cut the gears. This concept could be adapted to other lathes as well and Mr. Meek provides enough background information on the design that it could be applied to another lathe.
The reason I opted to buy the kit from Hemingway instead of building one is that I have numerous projects that need completion and it would have been quite some time until I could stop to build another accessory for my lathe. The Myford Super 7 lathe has a gap bed which really limits the usefulness of a conventional bed mounted carriage stop. It just doesn't allow the use of one near the headstock where much of the work is done. On lathes without the quick change gear box, there are several tapped holes available for a length stop attachment point, as can be seen on several of Ramon's work in progress photos. With the QCGB, there is precious little room available for a stop, although after doing some research back through Model Engineer and Engineering In Miniature, there have been several very good designs published in the past.
The Micrometer Saddle Handwheel has an adjustable micrometer collar and the graduations on my Imperial version are 0.010"/division and one revolution is 1.000" of linear travel along the bed. (Please see the Hemingway link for more information on accuracy, the Metric version, etc.) The graduations are wide enough that you can easily estimate to 0.005", which works great for quickly roughing a workpiece. It may not be the complete solution to accurate length control on the Myford all alone, but coupled with the usual techniques and my future length stop, I am confident it will do everything that I require of it. This will definitely make my Myford lathe a lot more fun to use and should speed up the machining time on many jobs considerably.
I can highly recommend this kit from Hemingway. Every part is beautifully machined to very high standards. The micrometer collar is ground and the graduations are crisply engraved. When assembled, it can be 'zeroed' very smoothly and the geartrain is silky smooth as well. The installation is very straight forward and the instructions are clear. The only machining required for the S7 is to drill and tap the existing handwheel shaft M5, which the instructions tell you that you can do without disassembling the lathe. Since I regularly (once or twice a year depending on how much cast iron I have machined) remove my leadscrew, saddle and apron to clean them, I opted to disassemble the lathe and remove the shaft which can be drilled and tapped in the lathe with the tailstock. The other important detail is to spend the time fitting the new hub and its keyway to the original shaft. This is just the usual deburring and fitting of parts. However, you want these to fit without interference because the assembly does have to be removed in order to access the apron oil fill plug, which is what is used to secure the new dial backplate to the apron.
Well done Graham Meek and Kirk Burwell from Hemingway Kits! Thanks for a great design and product.
Regards,
Mike