Thought I would share this interesting little job I have done for my cousins. They are keen on aviation history and have founded a museum based in Surrey UK. One project is a cockpit display from a P63 Kingcobra. They needed two seat brackets so they could bolt the seat on and came up with the original drawing for the part and asked if I could make them.
Not being required to fly they were not too bothered about fine tolerances which was just as well as they appear to me to be very close with the tongue being offset by 1 thou. Well that's if I read it right ;D.
Attatched the drawing and here's a photo of the brackets.
As I said it was good practice and I certainly need it on the mill. I find it very difficult to keep track of things and think about backlash and trying to re measure after you have made a few cuts. I found at one point I needed 16 thou off so I took 10 and measured again. Wow 1/2 thou undersize ??? Anyway I think they will probably do what is required of them.
Here's a link to their website
http://www.wingsmuseum.co.uk/
Peter.
Not being required to fly they were not too bothered about fine tolerances which was just as well as they appear to me to be very close with the tongue being offset by 1 thou. Well that's if I read it right ;D.
Attatched the drawing and here's a photo of the brackets.
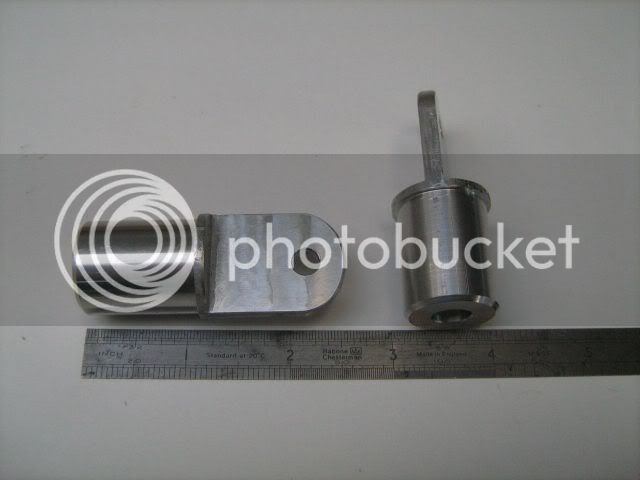
As I said it was good practice and I certainly need it on the mill. I find it very difficult to keep track of things and think about backlash and trying to re measure after you have made a few cuts. I found at one point I needed 16 thou off so I took 10 and measured again. Wow 1/2 thou undersize ??? Anyway I think they will probably do what is required of them.
Here's a link to their website
http://www.wingsmuseum.co.uk/
Peter.
