Mitchg07261995
Senior Member
- Joined
- Nov 12, 2012
- Messages
- 242
- Reaction score
- 53
Hi all, I started making the micro hosc engine in my class during free time, like during our 15 minute break that we get one time per day. I am building this and a stirling engine at the same time so i am just working on the hosc when i find a spare few minutes. Im thinking of going in on tuesdays and staying from 7:30 am-3:45 when i normally get out of class to get alot more done on the two engines. I ordered some of the really tiny drills that I need for this engine today from tool king.
any way here is what i have this far.
flywheel, .250'' diameter with a whole in the center from a #60 drill
with air fitting for the engine, i just need a .020'' drill which should be here with in the next 2 weeks
and just to show how tiny these parts are, here is the cylinder back plate to my stirling engine that i am building, the graph paper that it is sitting on has 4 squares to the inch...
mitch
P.S thanks for the plans Steve!
any way here is what i have this far.
flywheel, .250'' diameter with a whole in the center from a #60 drill
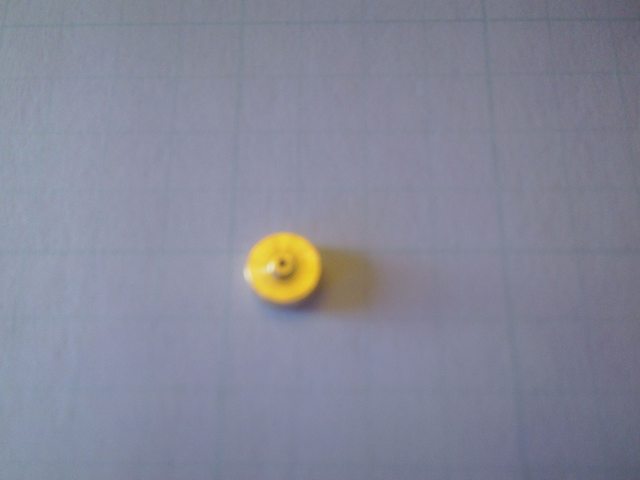
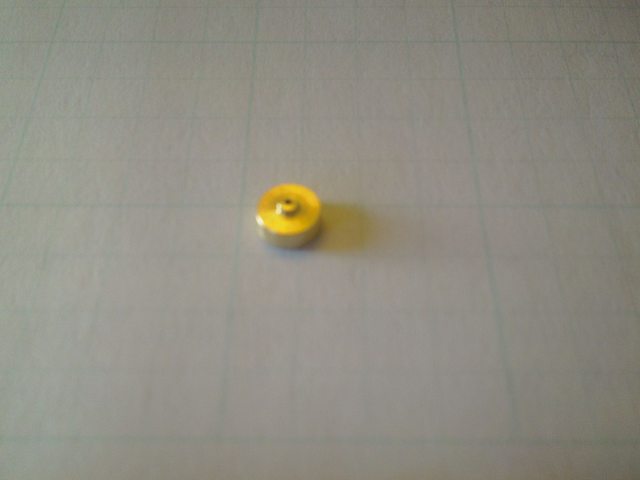
with air fitting for the engine, i just need a .020'' drill which should be here with in the next 2 weeks
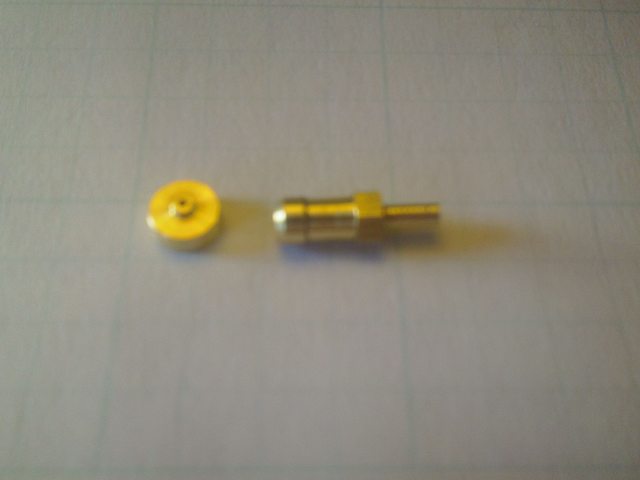
and just to show how tiny these parts are, here is the cylinder back plate to my stirling engine that i am building, the graph paper that it is sitting on has 4 squares to the inch...
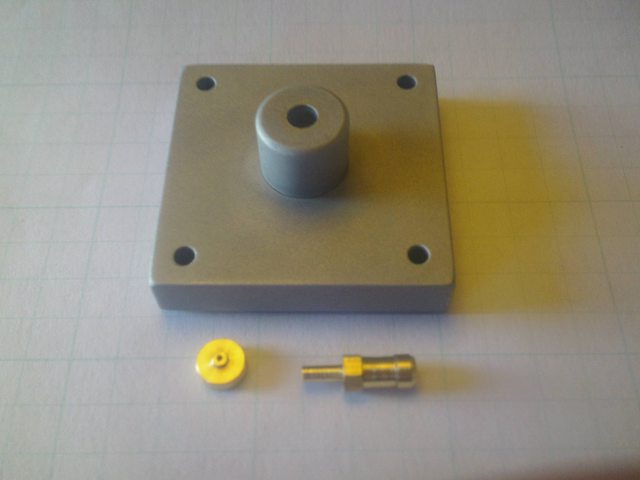
mitch
P.S thanks for the plans Steve!