Hi,
I have had 6 Dickson style holders for many years but didn't want to buy any more at $80 each over here, so I decided to make my own. I did consider buying a wedge style from the US, but I would loose money on this one as it cost me $500 8 years ago.
I made these up last year but am just getting around to posting them now because of the house move. I am still yet to decide what finish is going on them.
My mate gave me a piece of plate (column base of a large shed) a few years back and I have kept it for this purpose. It was 550 x 350 x 32mm thick and the tool holders are 31.75 deep so close enough to the thickness of the factory ones.
I had to cut it up but it wouldn't fit in the bandsaw so I put 2 cuts in it outside with the 9inch grinder.
After that it was about 4-5 hours sitting by the saw cutting it into little blocks.The bandsaw was clean before I started and the carbon blade did a good job.
This is the Dickson style tool post, it has 2 V's and a slot where it is pulled back onto the V's via a cam action in the tool post, very simple really.
Once they where all cut up I faced the sides and the ends with the horizontal spindle and a carbide end mill.
The slot was then roughed out.
One side of the V roughed out
The other side of the V roughed out.
The pile roughed out to get rid of most of the waist metal.You can see a red and blue one there, I colored these because they came off the saw a little thin so I marked them like this as they where not the same as the others. It was only something small like 0.25-0.5mm but it makes a difference in setting them up in a jig.
This is the jig I used for the roughing angle for the V's.
Here I am roughing the slot wider with a hoging end mill, it was easier to widen the slot with the vertical spindle than the horizontal spindle.
The finish left from the roughing end mill.
Finishing the slot
Cutting the slot with a key seat cutter. It was a bit blunt so I sharpened it using the lathe, it then did the whole job.
You can see how the swarf filled the vice, so I cut up some ice cream container to help out.
The little key cutter moved so metal
Facing them all
Knocking the corners off with a 45 degree end mill
Finishing the V's
machining a flat on top of the V's
Drilling all the holes with a temporary shield
This is the tap set up I used, the coolant flushed out the chips so things went quicker. I had to tap 230 M8 holes.
I cut up the 25mm bar for the adjusters, drilled and taped them, then mad up this arbour to thread them on for all there operations.
Making the adjusters
I stole the wheels off the push knurler and made a clamp knurler
Knurling the adjusters
My temporary coolant set up run off the mill.
All knurled
Most of the shaving that where caught after knurling.
I set up these tools in 2 tool holders to do all the operations in one go
Machined the outside diameter
Taking of the sharp corner
Taking off the bottom edge.
All done, I made 60 odd for spares as I never want to make these again,LOL
All of them heated up and dunked in oil
What a repetitious job
Finished
The one stuff up when I was roughing them, oh well it will get used for something like an indicator holder.
I picked up 1500 odd grub screws from the UK for just over $100, a lot cheap than buying them here for $50 odd dollar a box of 100.There is more than in the picture they are just the M8 ones need for the tool holders.
I have different lengths so I will be able to custom fit the grub screws to different size tooling I put in them
holders and will be changing my factory holders over to grub screws as well. The square he bolts where just to expensive and I would rather they didn't stick up above the holder.
Wow that was a lot of work.
Dave
I have had 6 Dickson style holders for many years but didn't want to buy any more at $80 each over here, so I decided to make my own. I did consider buying a wedge style from the US, but I would loose money on this one as it cost me $500 8 years ago.
I made these up last year but am just getting around to posting them now because of the house move. I am still yet to decide what finish is going on them.
My mate gave me a piece of plate (column base of a large shed) a few years back and I have kept it for this purpose. It was 550 x 350 x 32mm thick and the tool holders are 31.75 deep so close enough to the thickness of the factory ones.
I had to cut it up but it wouldn't fit in the bandsaw so I put 2 cuts in it outside with the 9inch grinder.
After that it was about 4-5 hours sitting by the saw cutting it into little blocks.The bandsaw was clean before I started and the carbon blade did a good job.
This is the Dickson style tool post, it has 2 V's and a slot where it is pulled back onto the V's via a cam action in the tool post, very simple really.
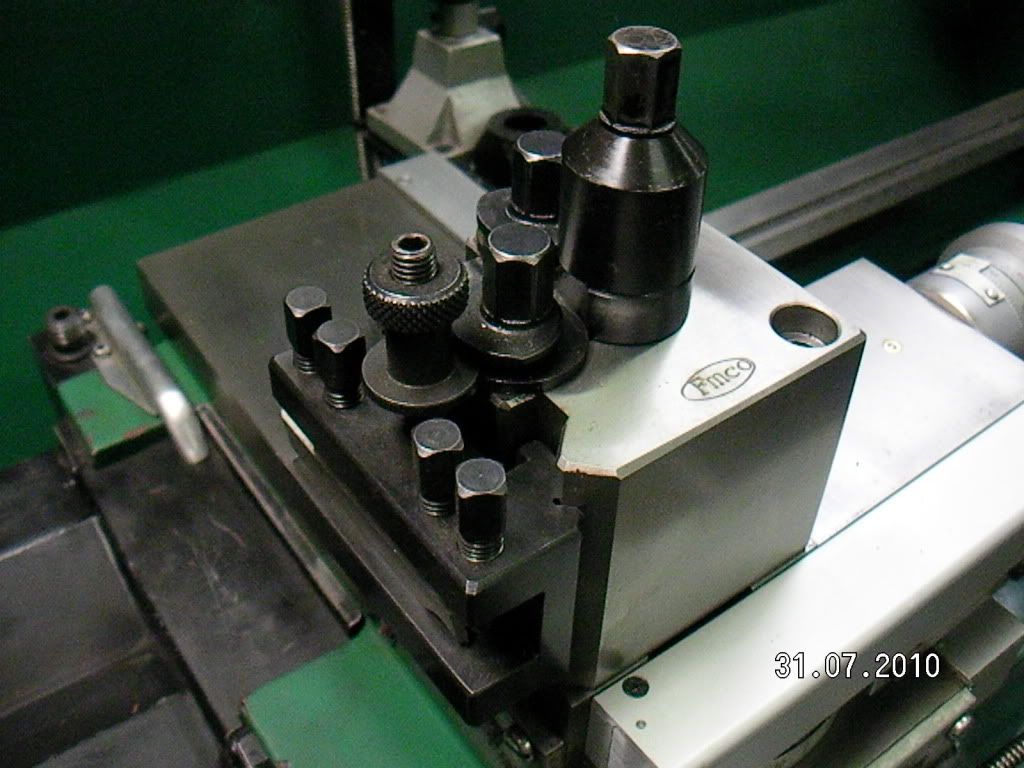
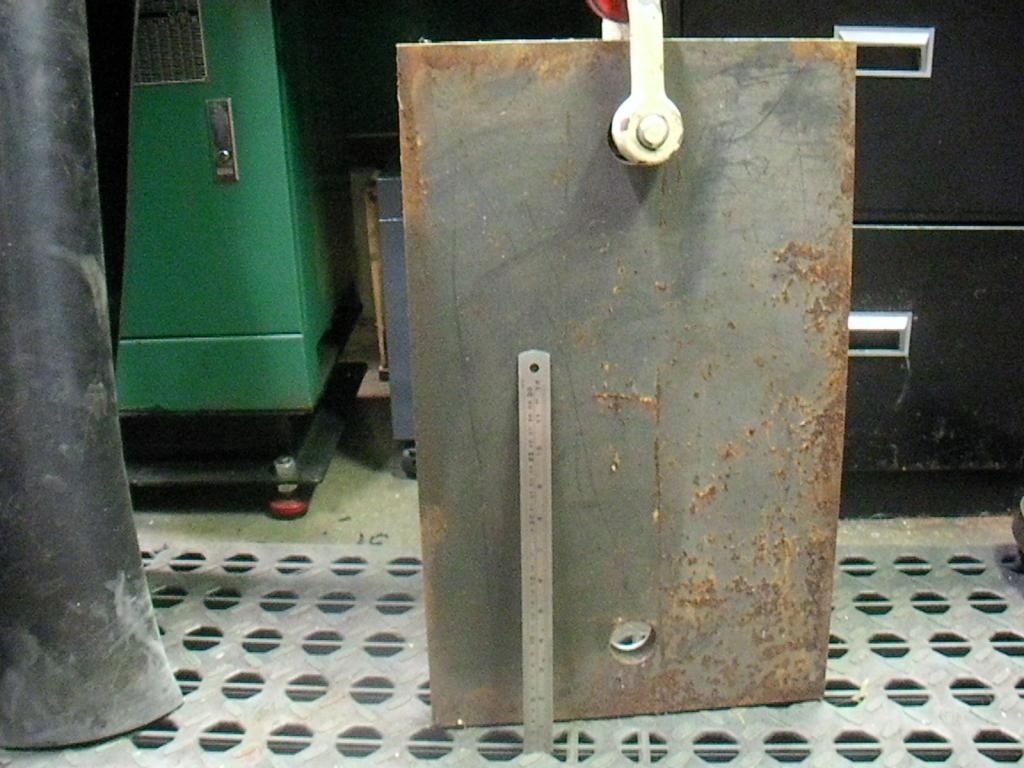
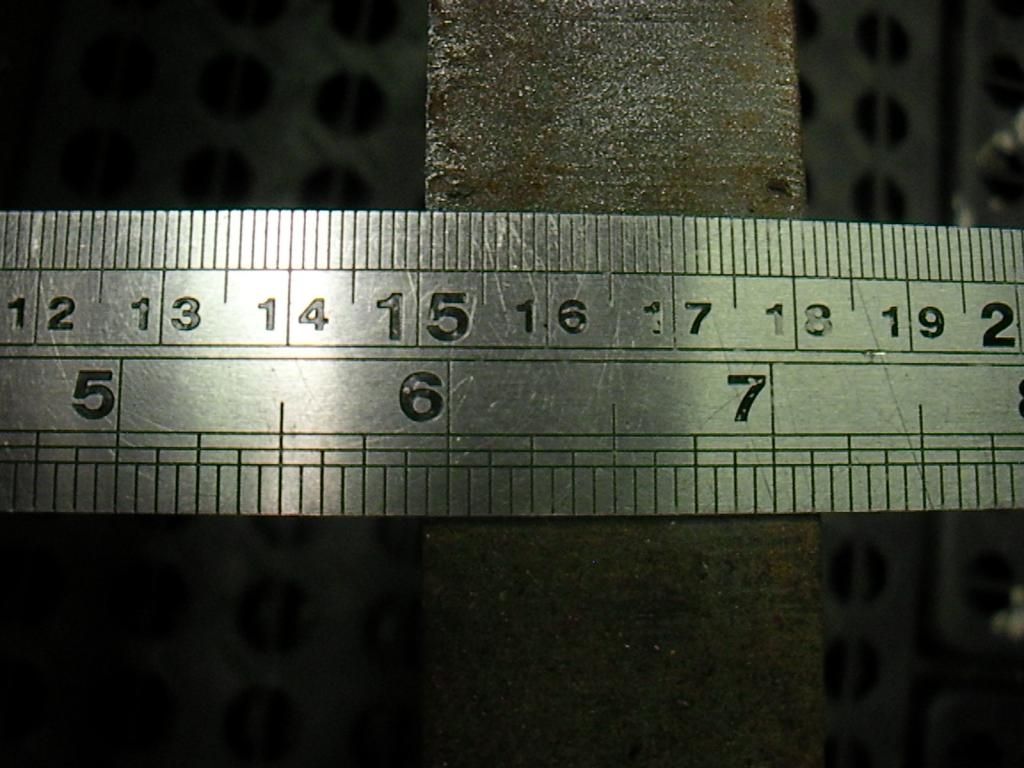
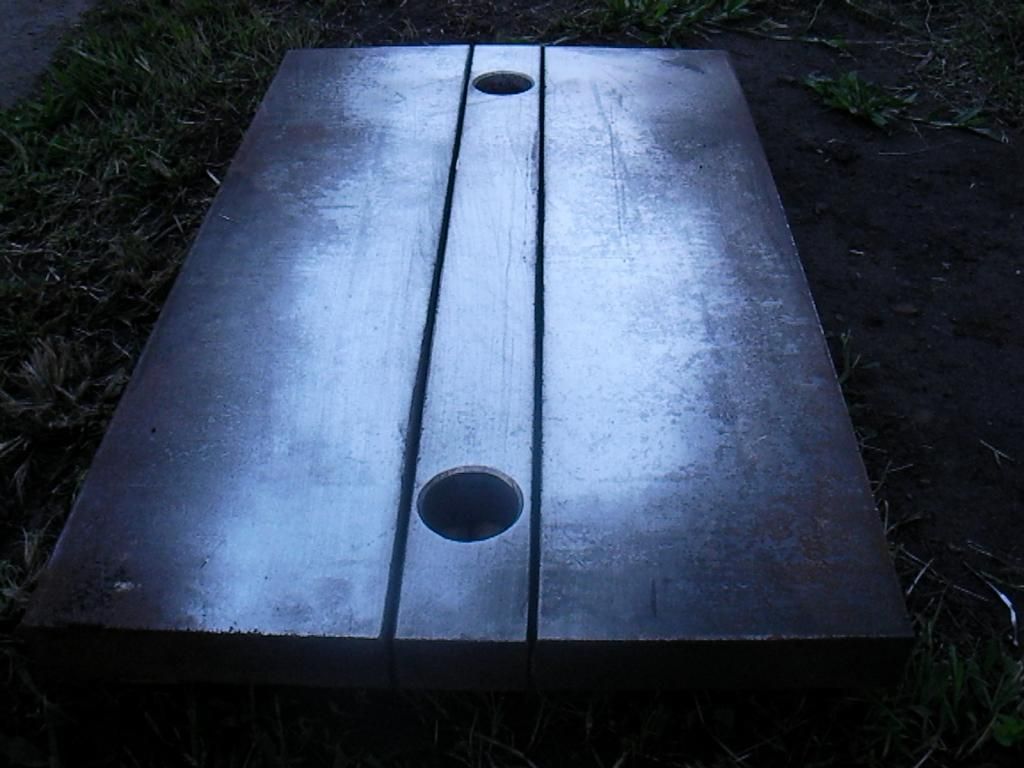
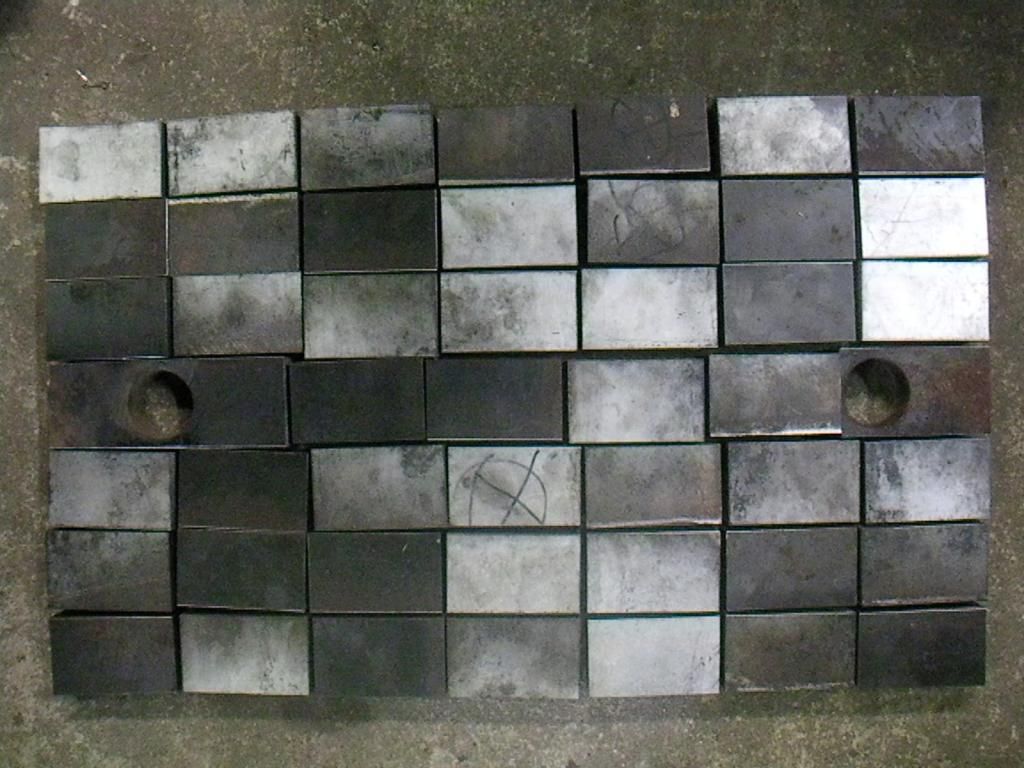
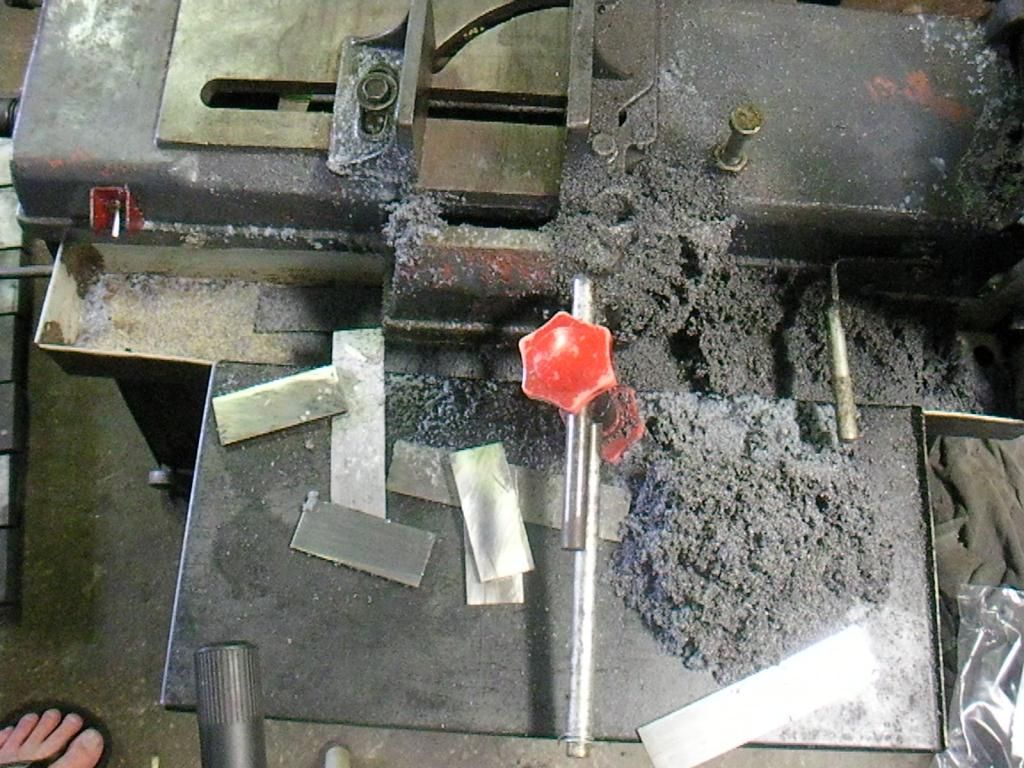
Once they where all cut up I faced the sides and the ends with the horizontal spindle and a carbide end mill.
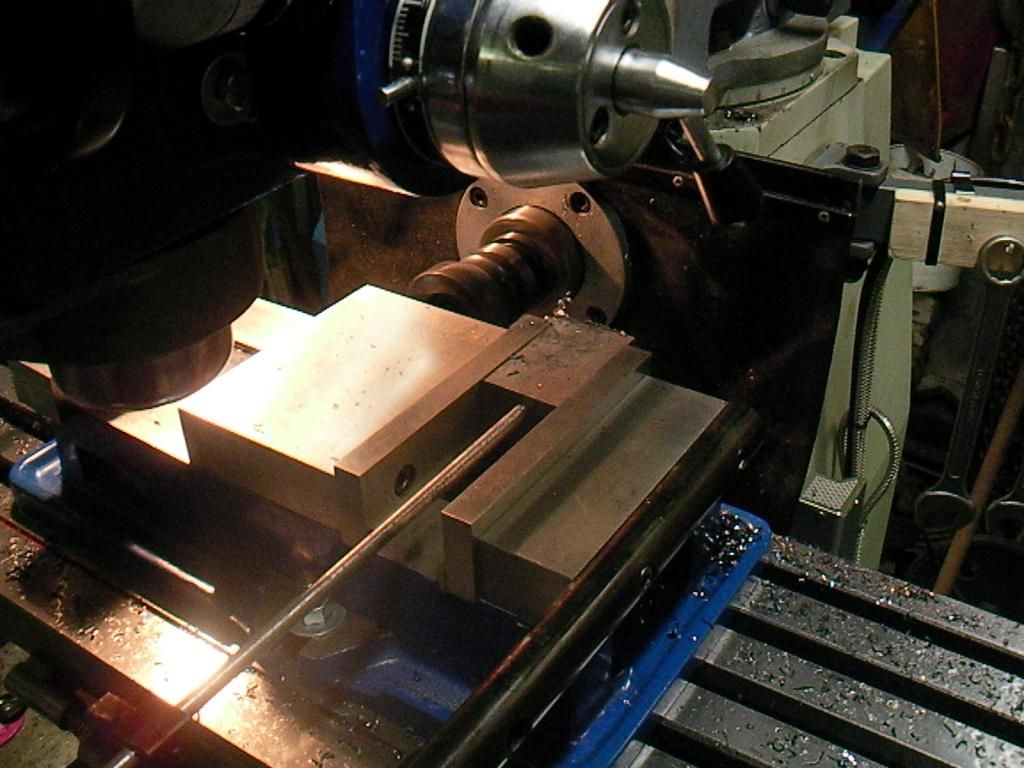
The slot was then roughed out.
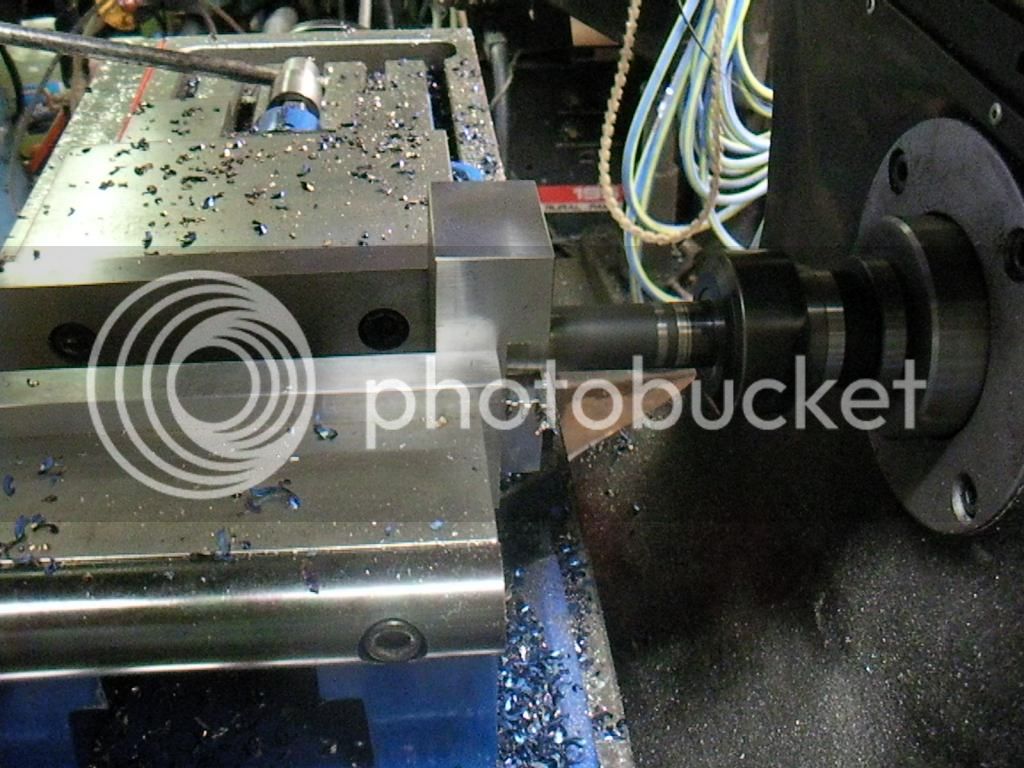
One side of the V roughed out
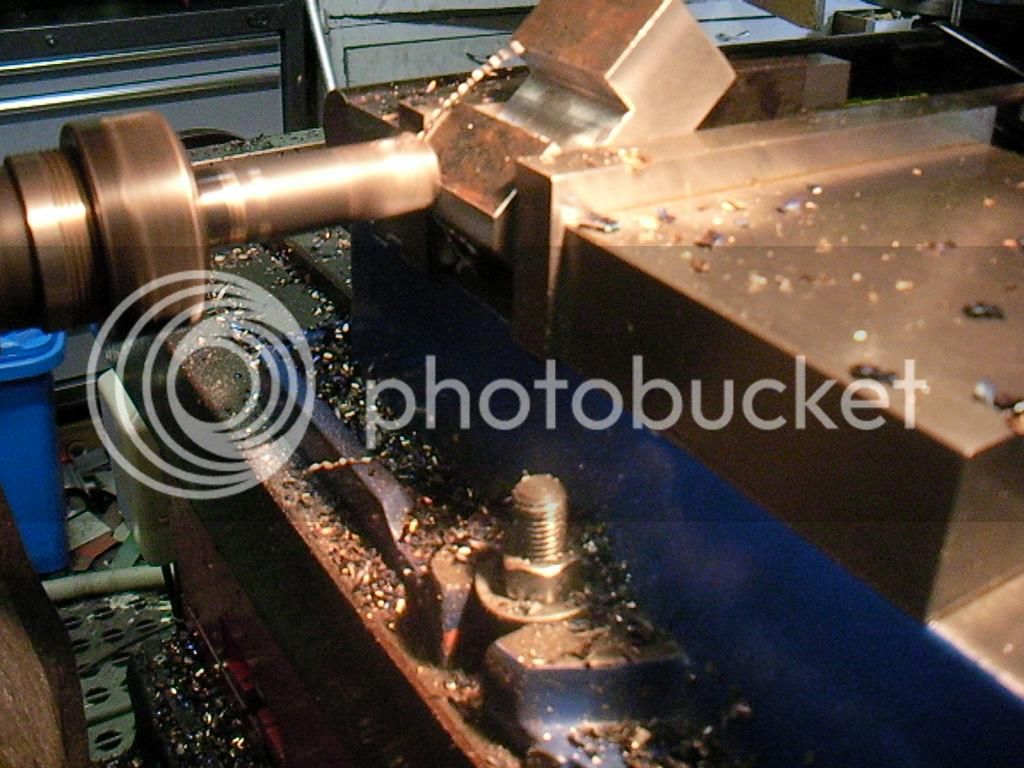
The other side of the V roughed out.
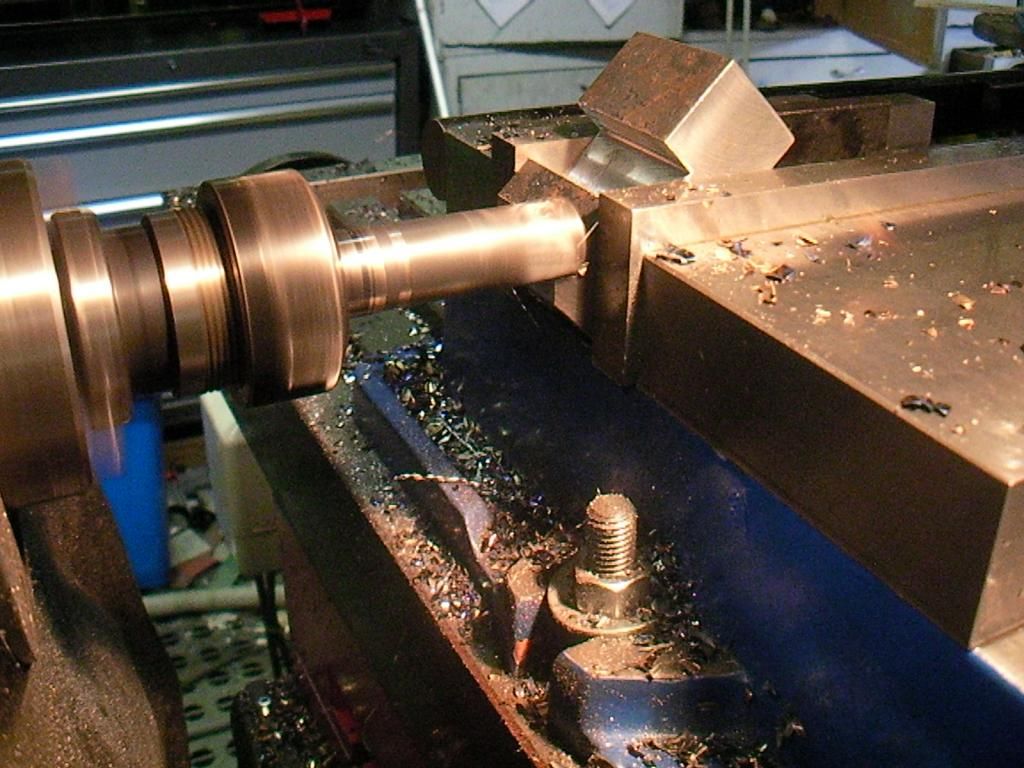
The pile roughed out to get rid of most of the waist metal.You can see a red and blue one there, I colored these because they came off the saw a little thin so I marked them like this as they where not the same as the others. It was only something small like 0.25-0.5mm but it makes a difference in setting them up in a jig.
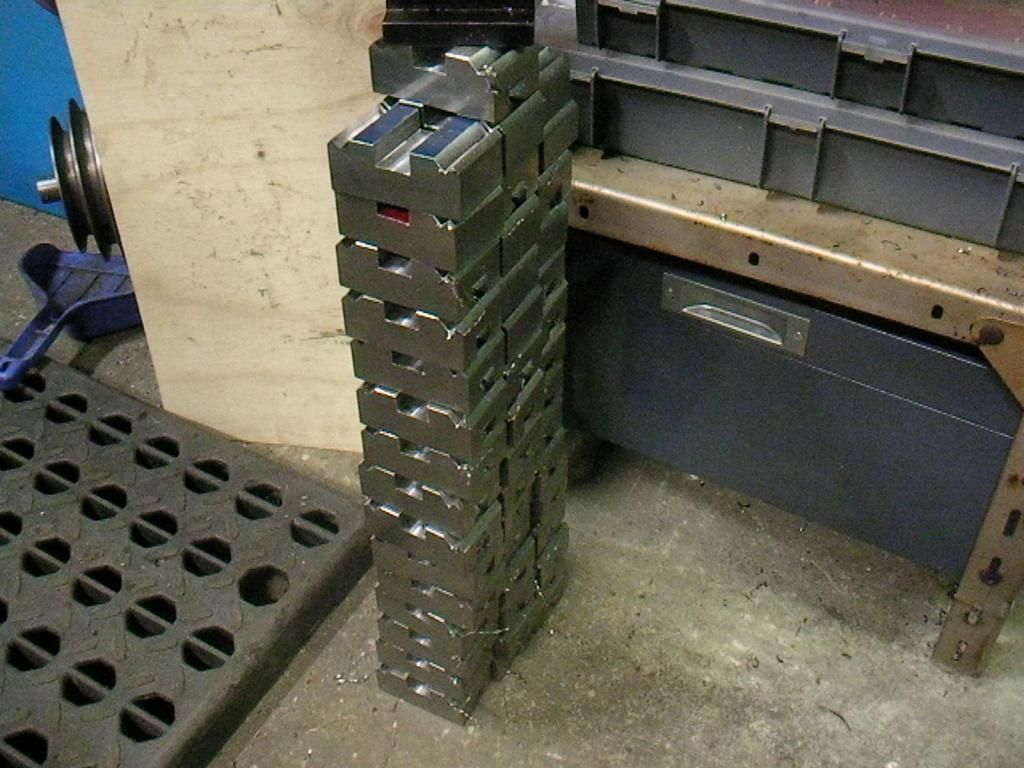
This is the jig I used for the roughing angle for the V's.
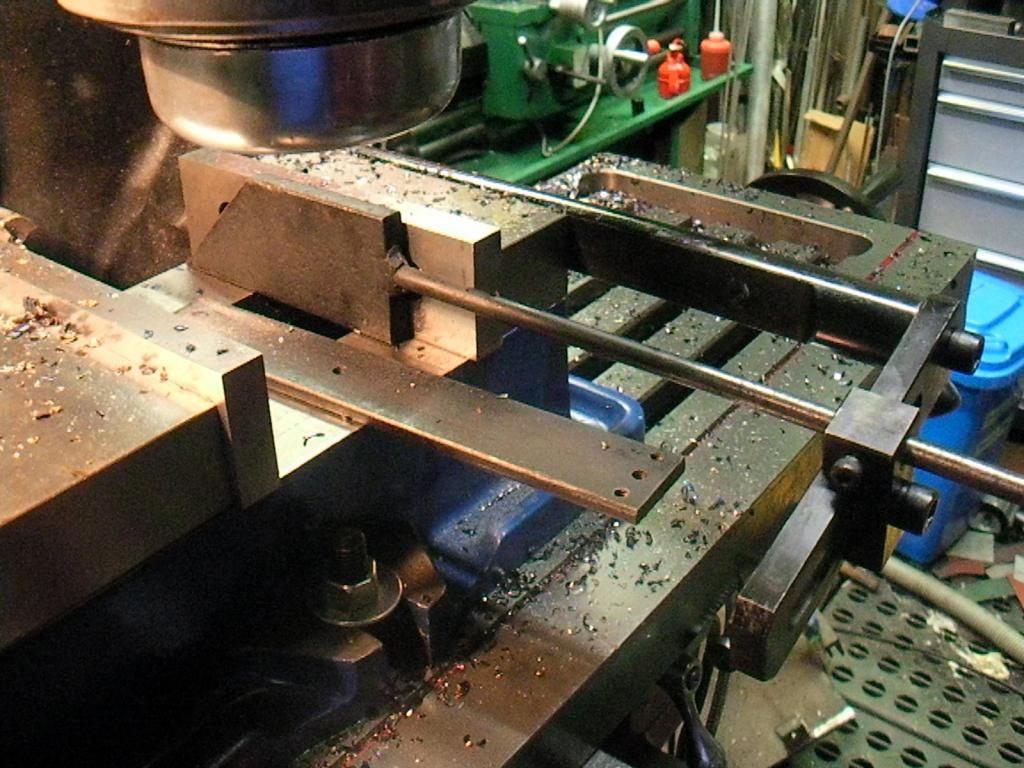
Here I am roughing the slot wider with a hoging end mill, it was easier to widen the slot with the vertical spindle than the horizontal spindle.
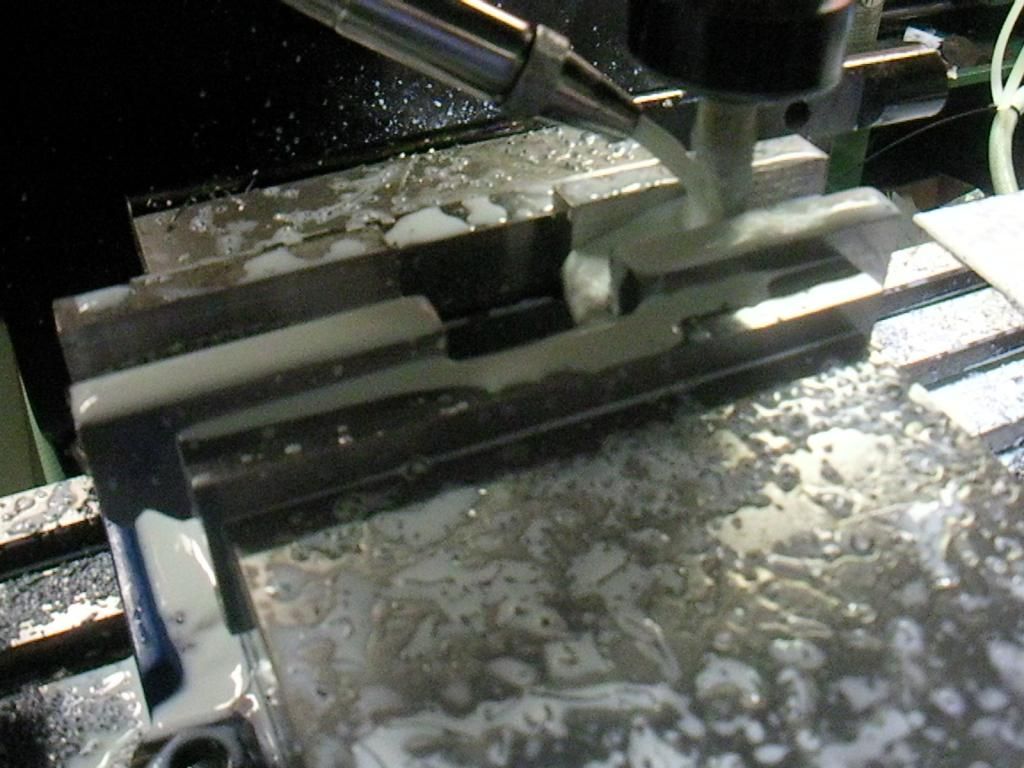
The finish left from the roughing end mill.
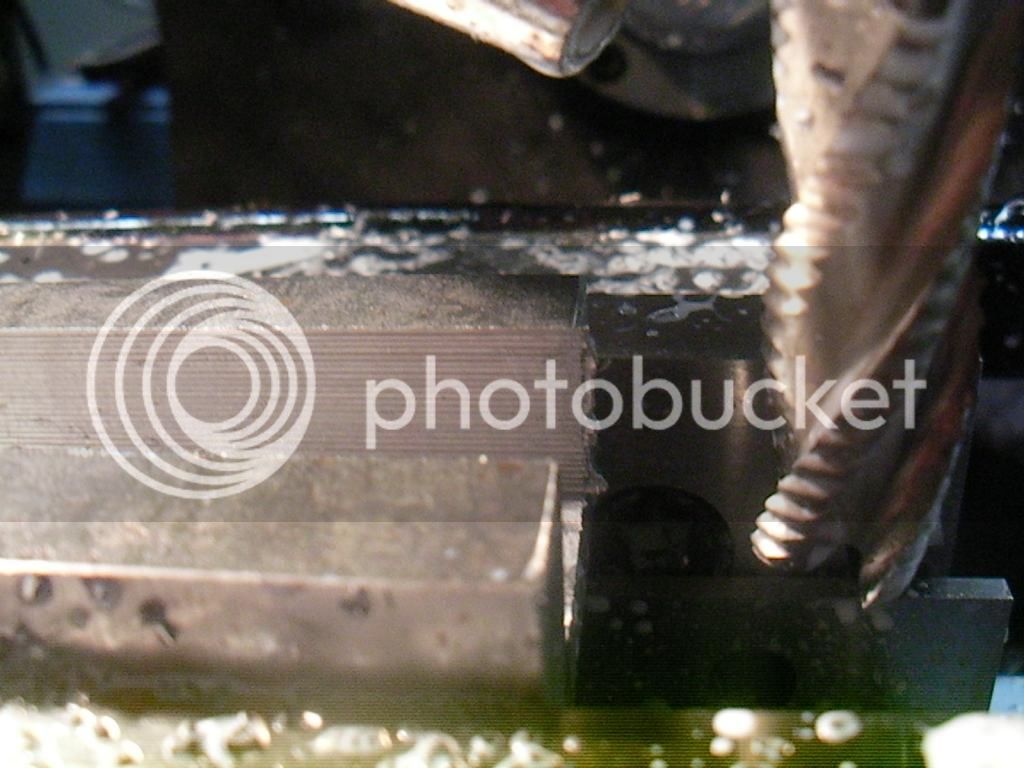
Finishing the slot
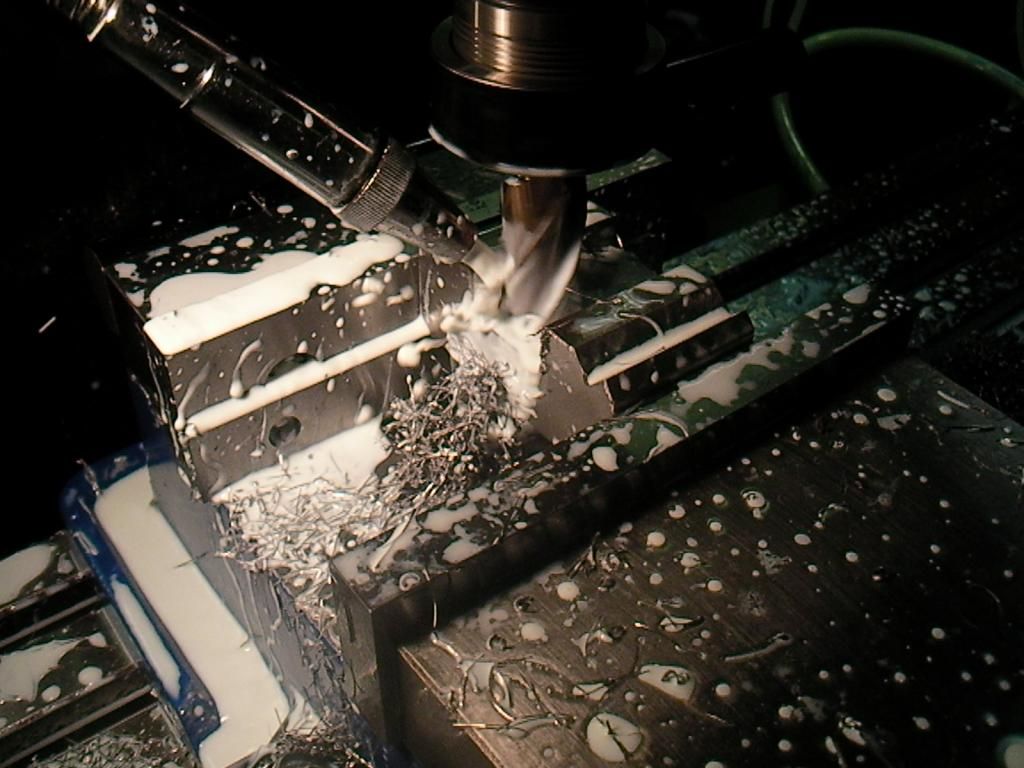
Cutting the slot with a key seat cutter. It was a bit blunt so I sharpened it using the lathe, it then did the whole job.
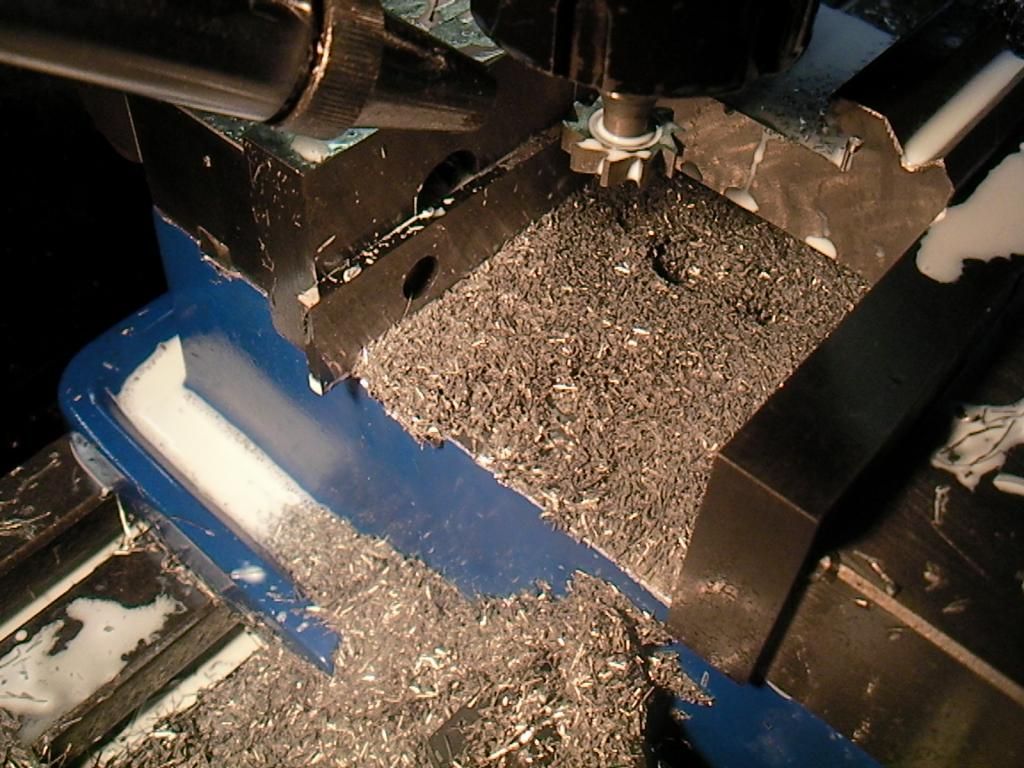
You can see how the swarf filled the vice, so I cut up some ice cream container to help out.
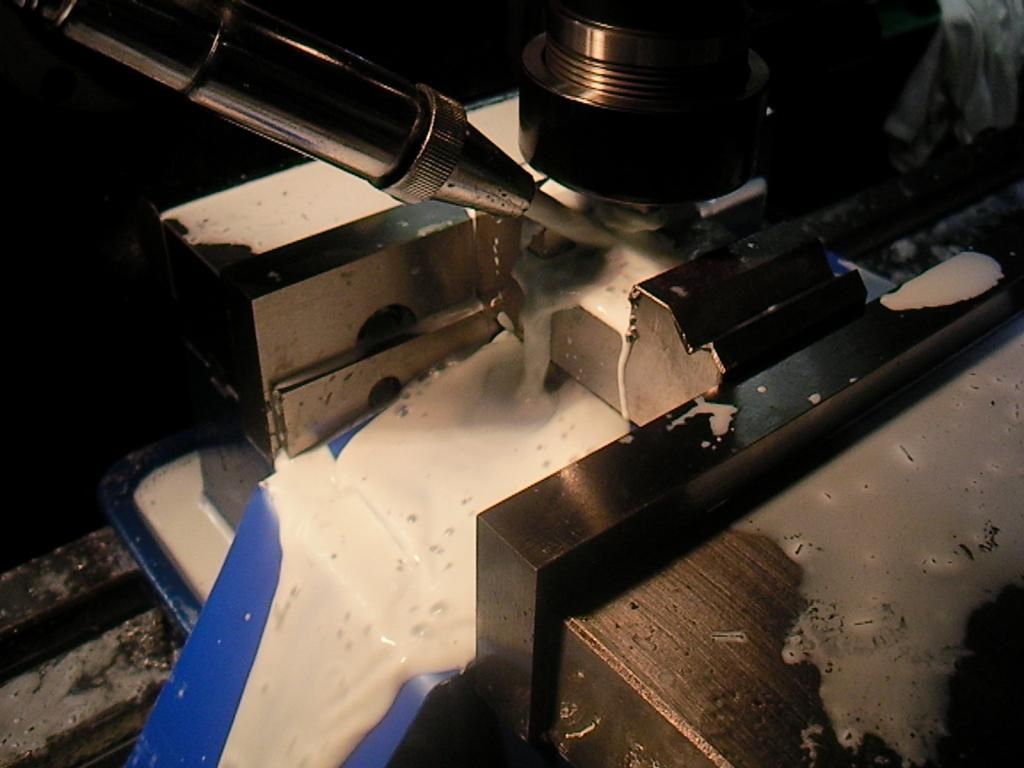
The little key cutter moved so metal

Facing them all
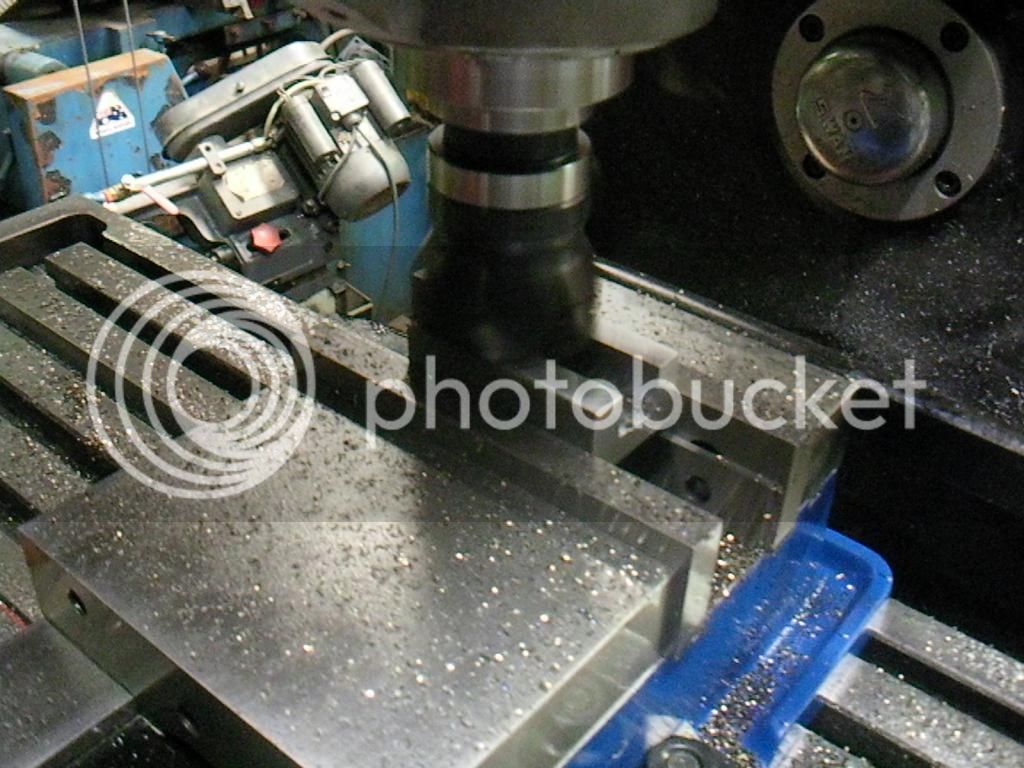
Knocking the corners off with a 45 degree end mill
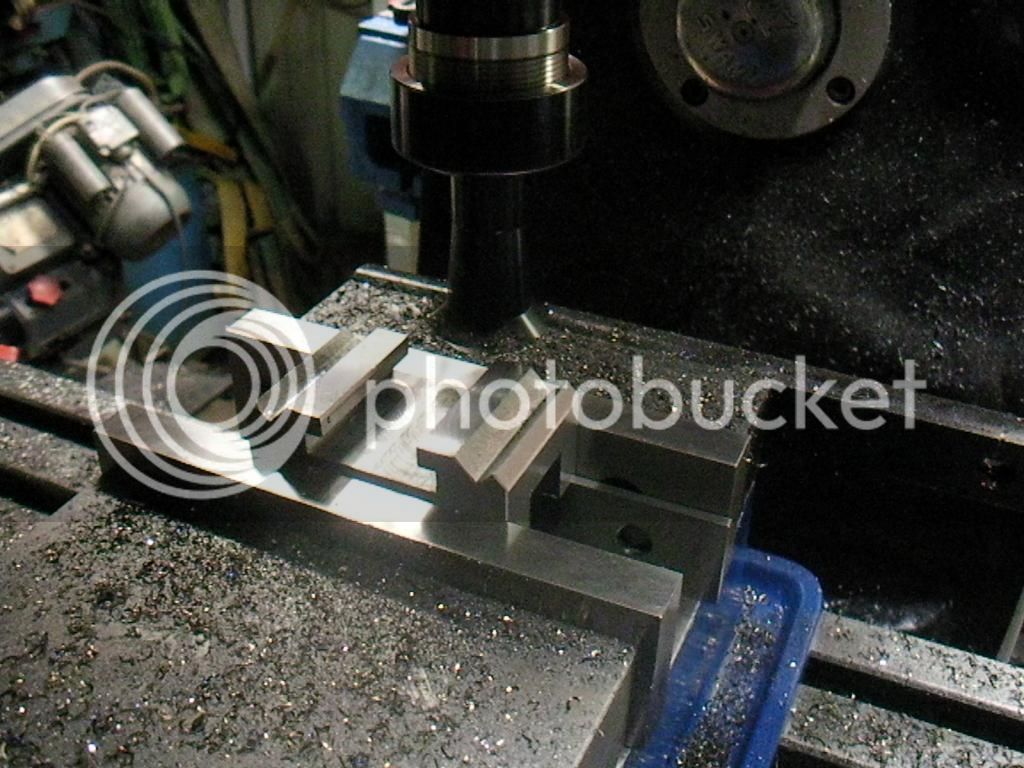
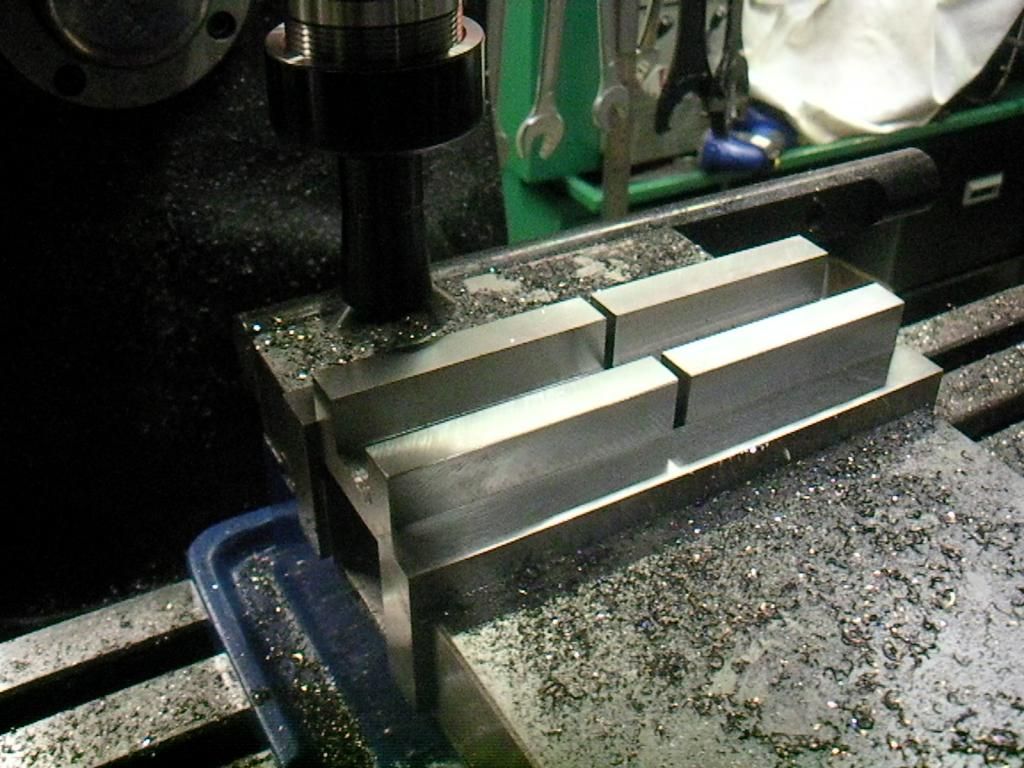
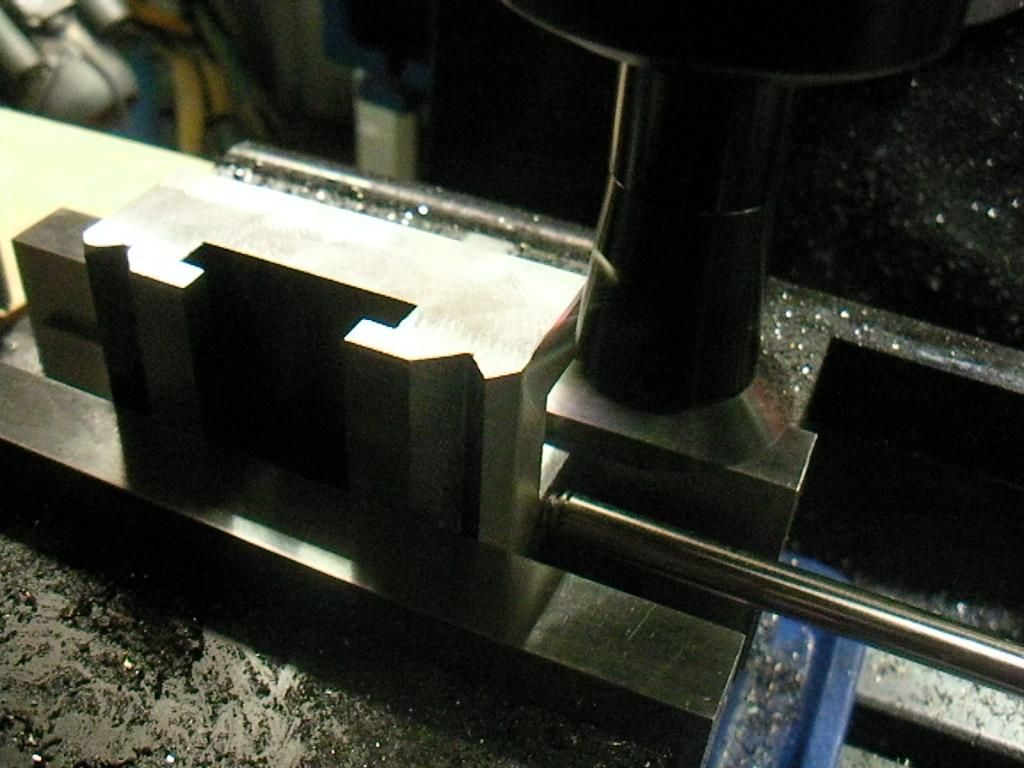
Finishing the V's
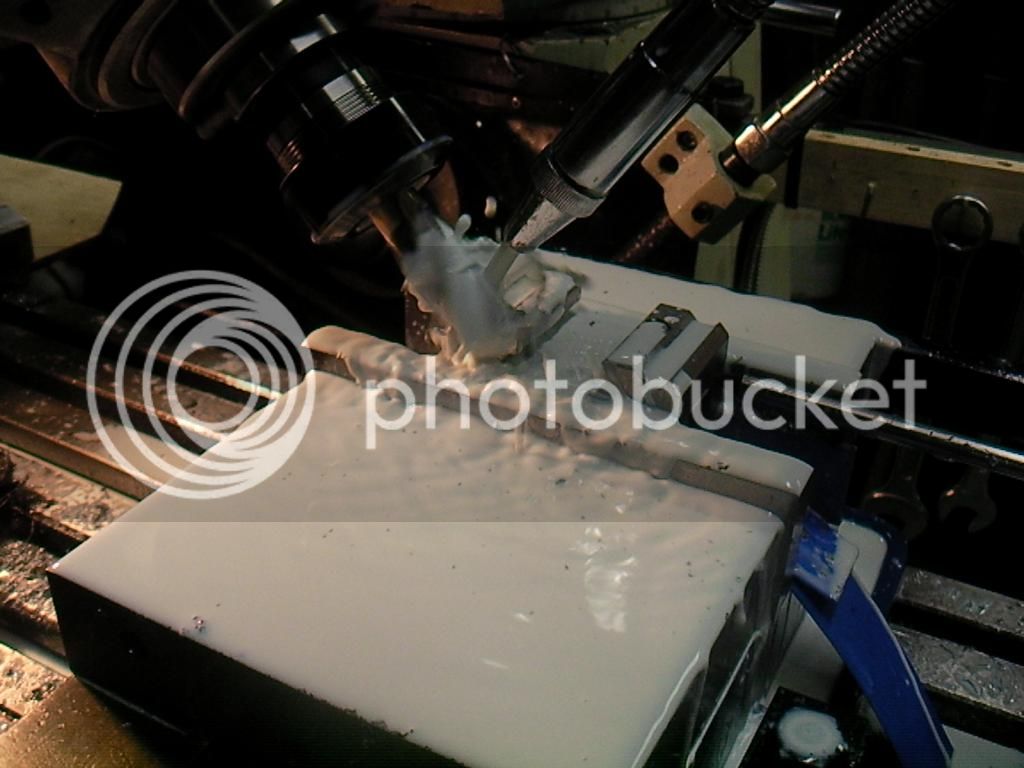
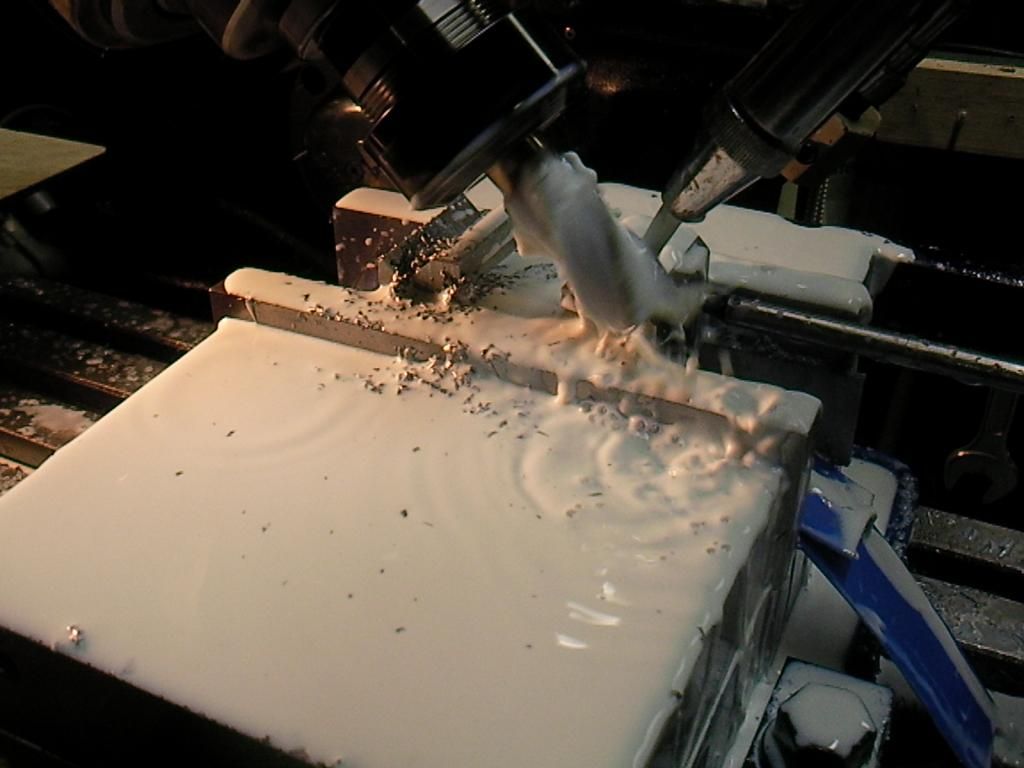
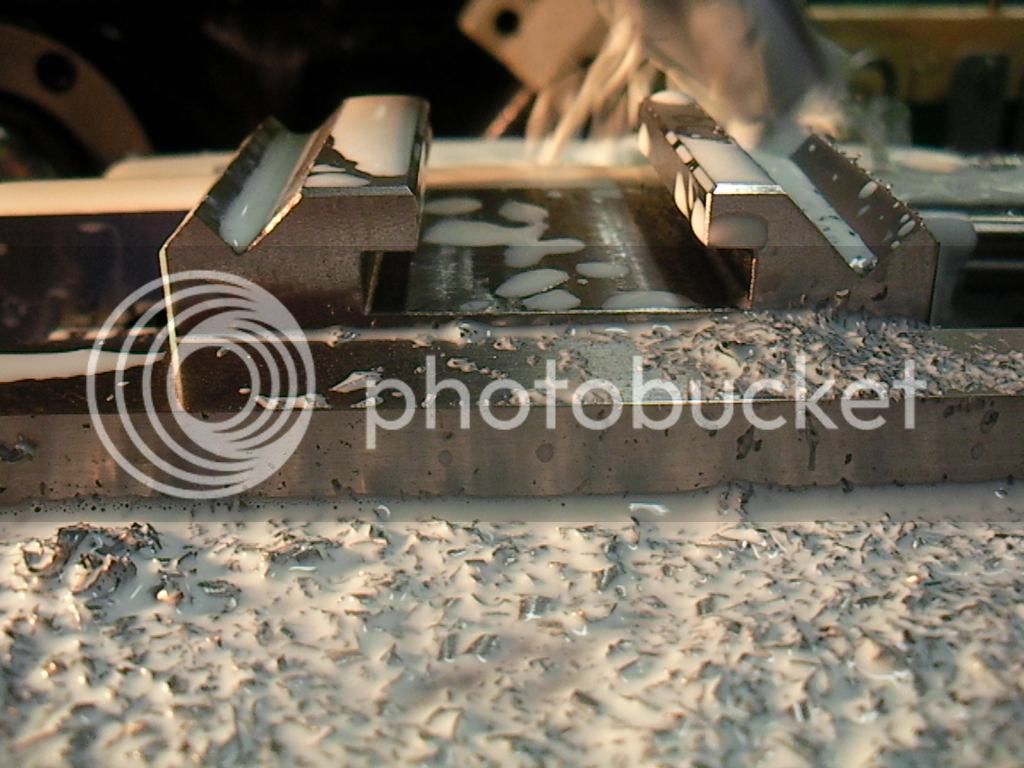
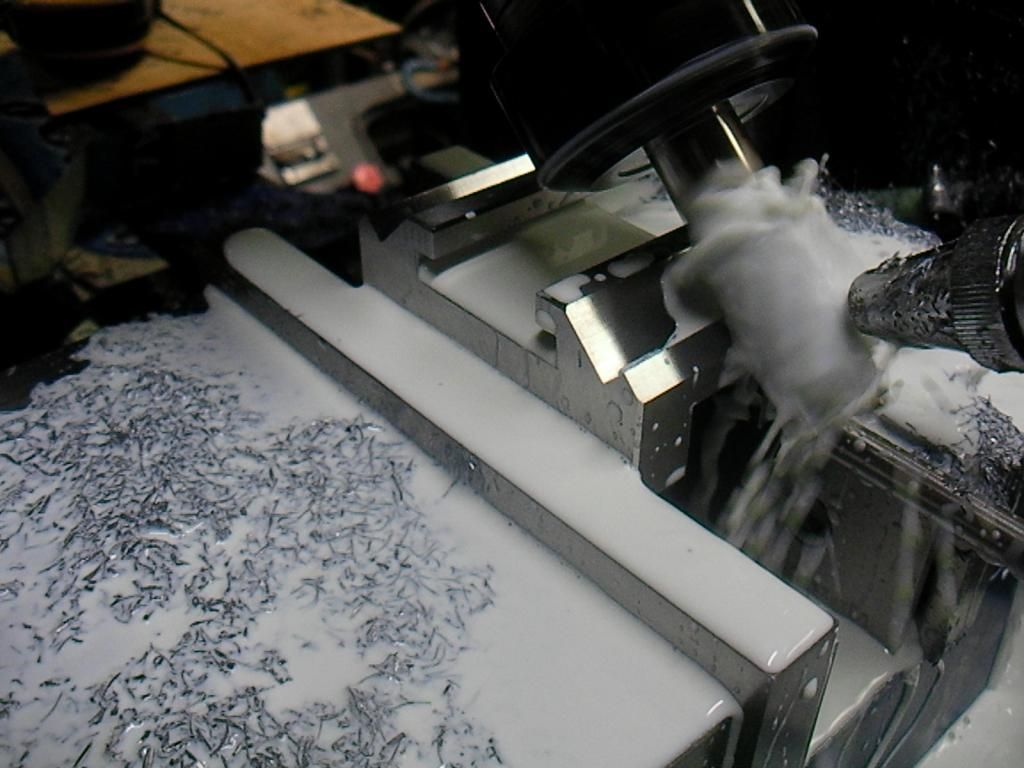
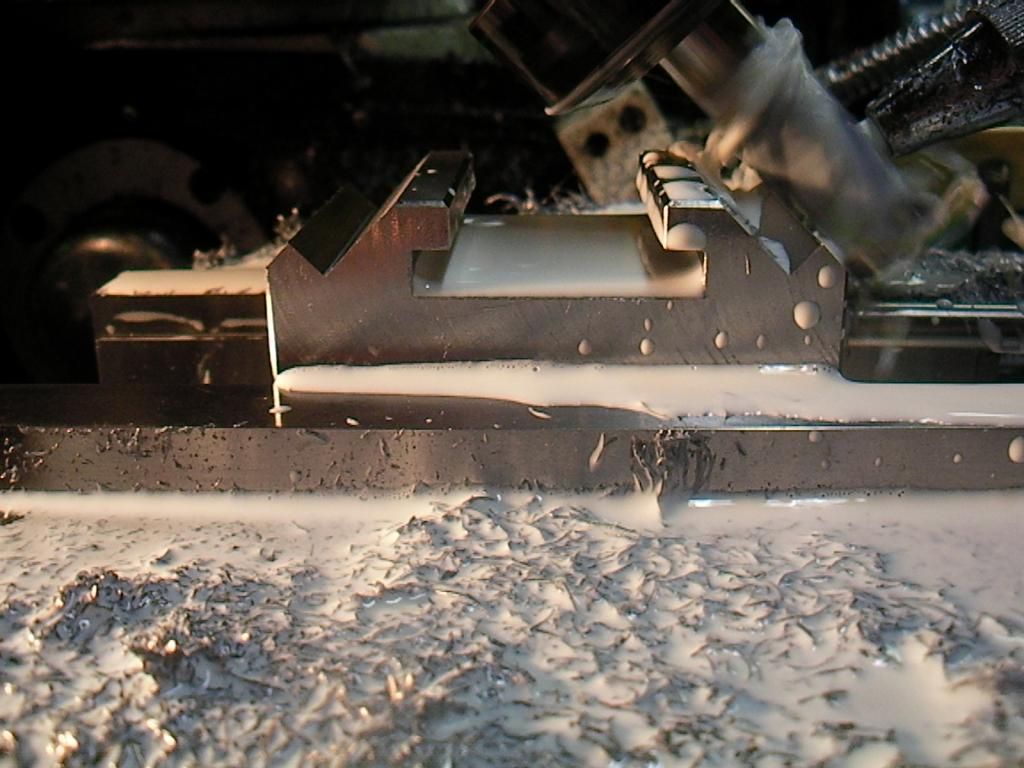
machining a flat on top of the V's
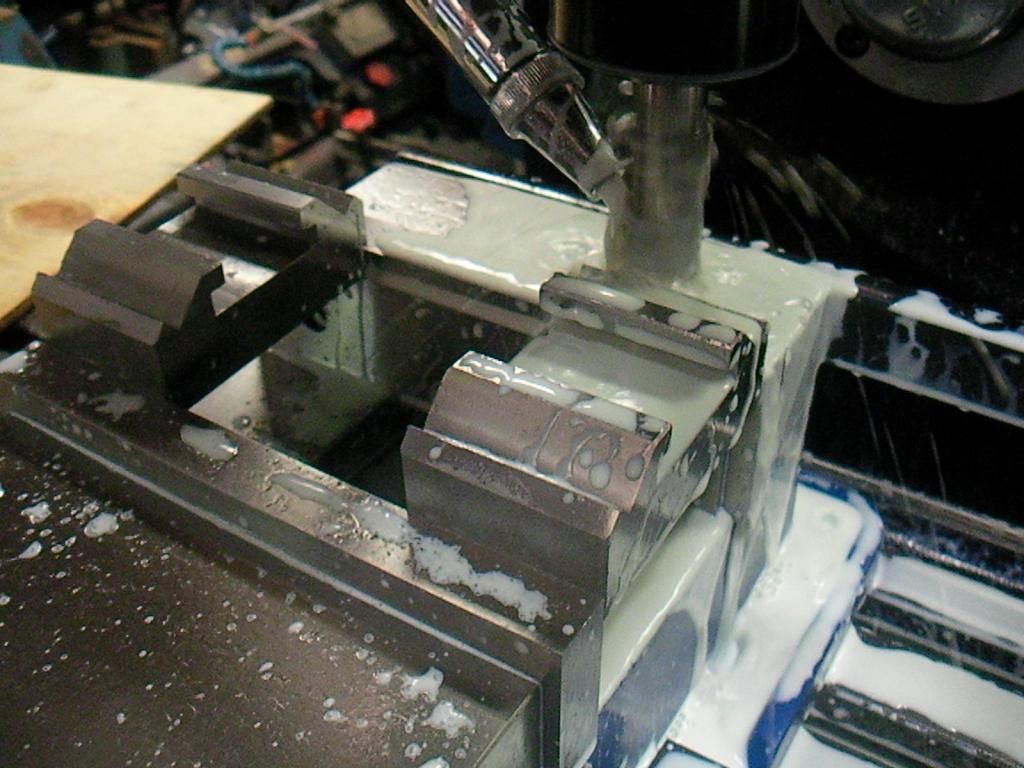
Drilling all the holes with a temporary shield
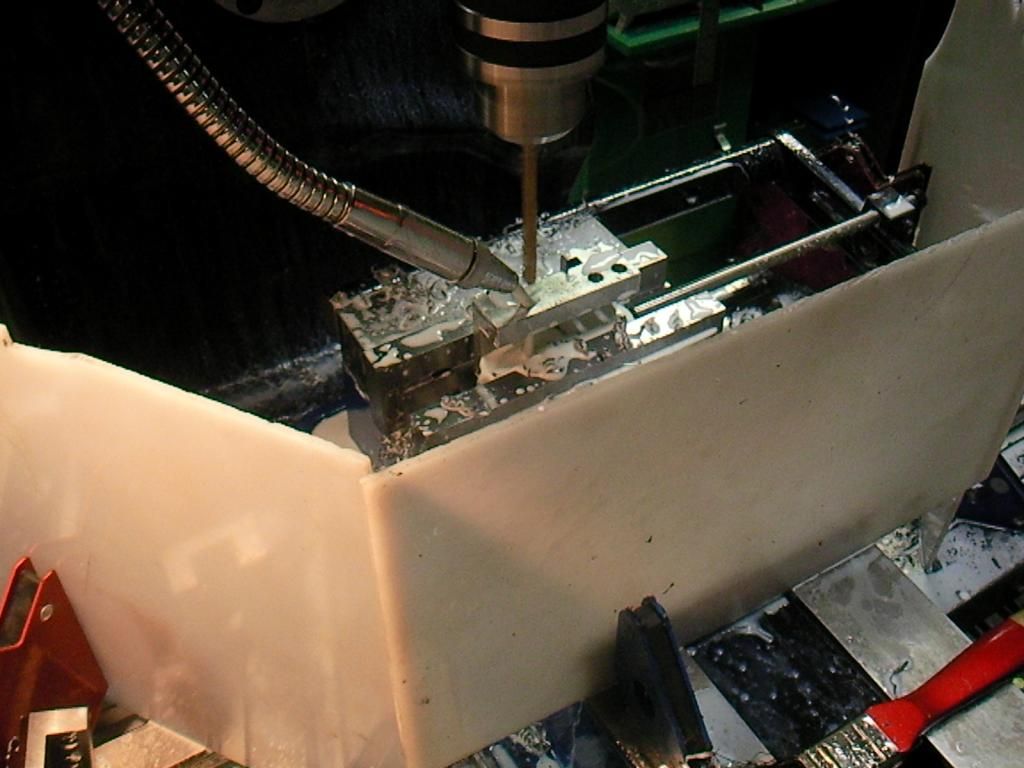
This is the tap set up I used, the coolant flushed out the chips so things went quicker. I had to tap 230 M8 holes.
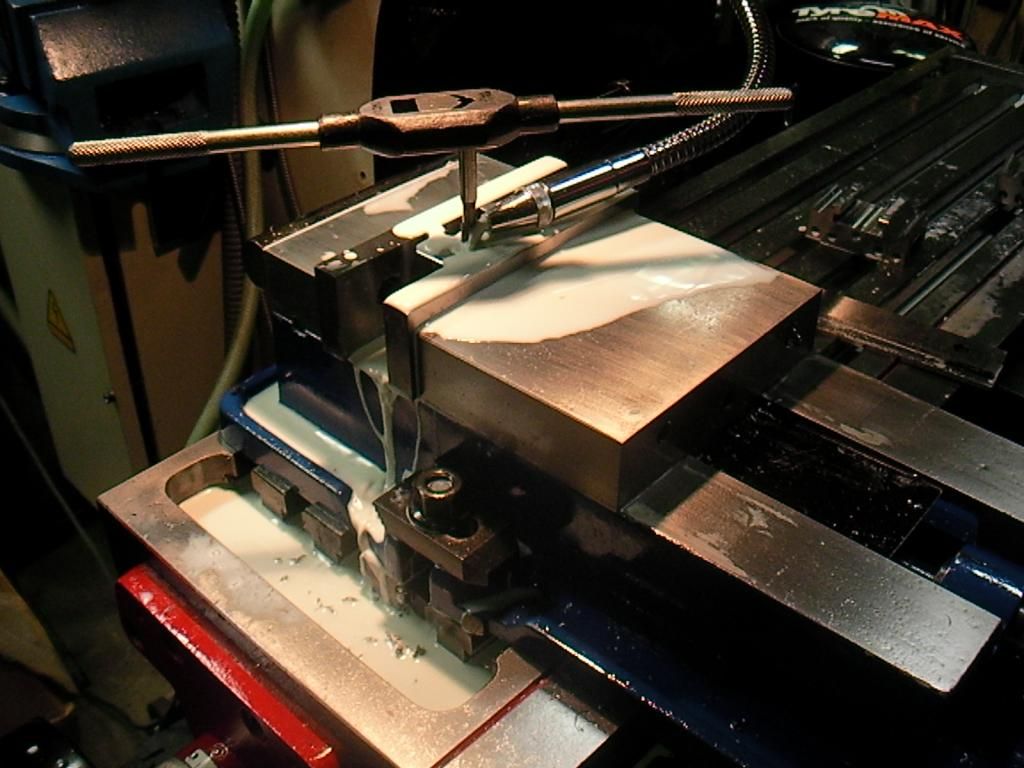
I cut up the 25mm bar for the adjusters, drilled and taped them, then mad up this arbour to thread them on for all there operations.
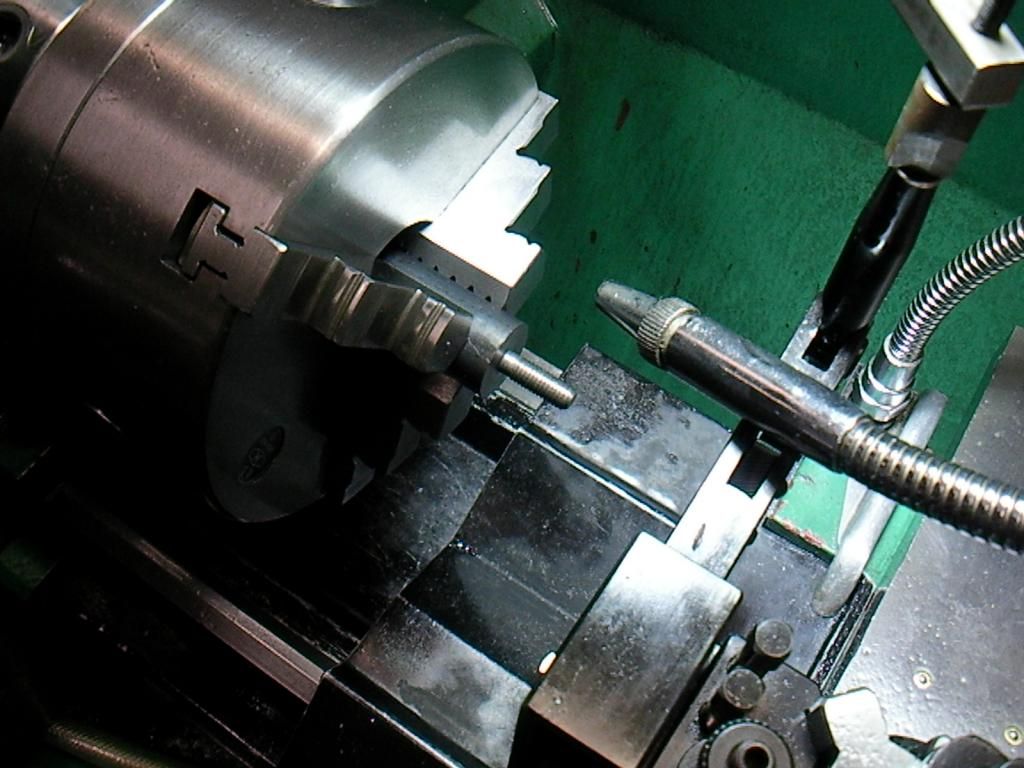
Making the adjusters
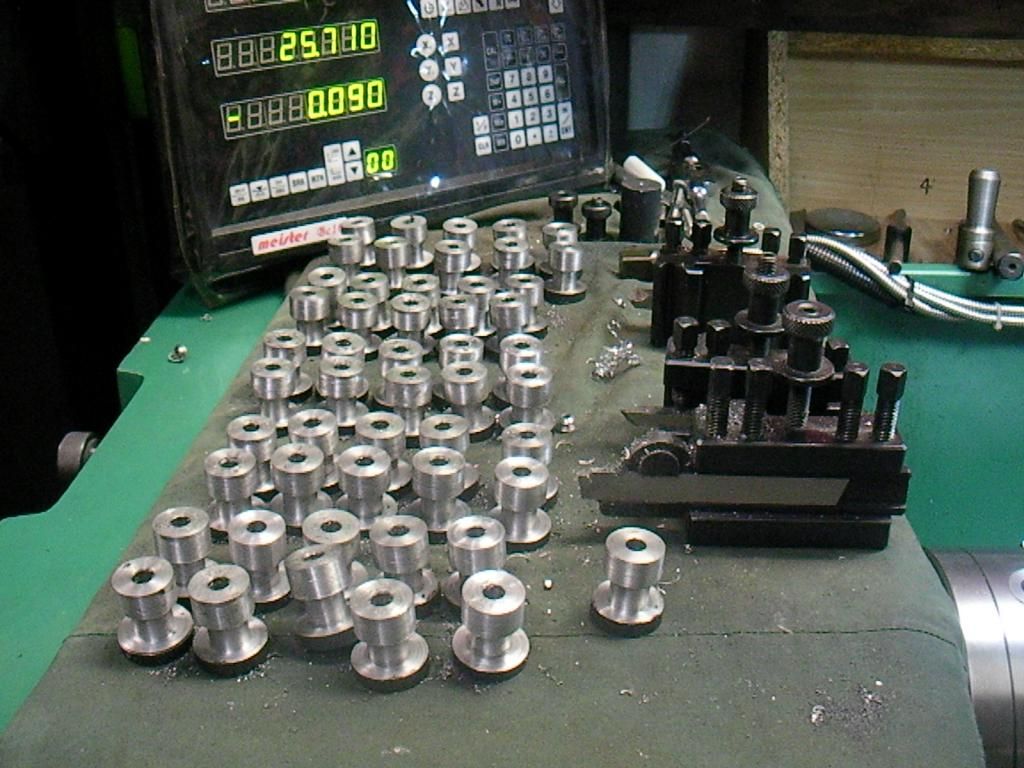
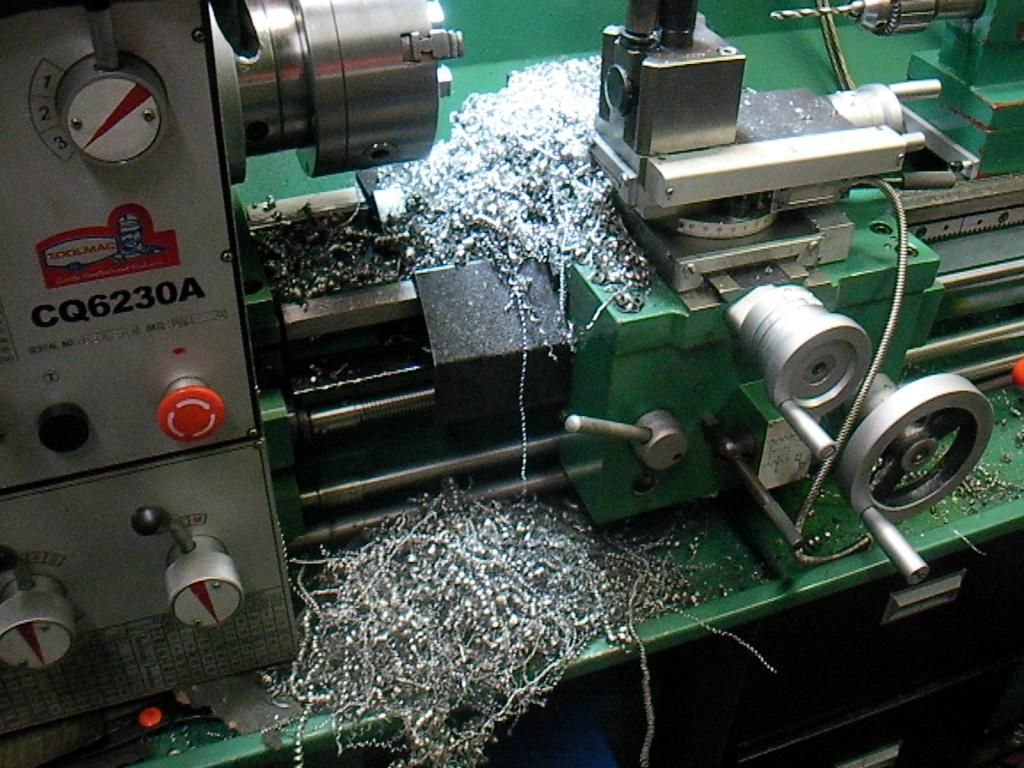
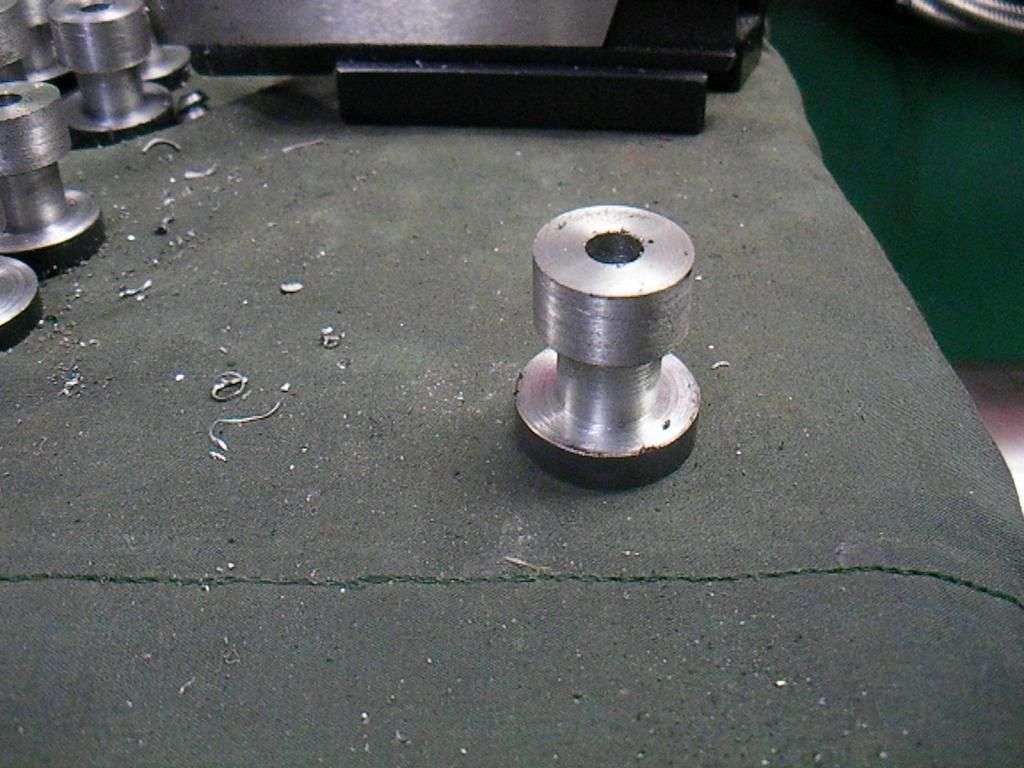
I stole the wheels off the push knurler and made a clamp knurler
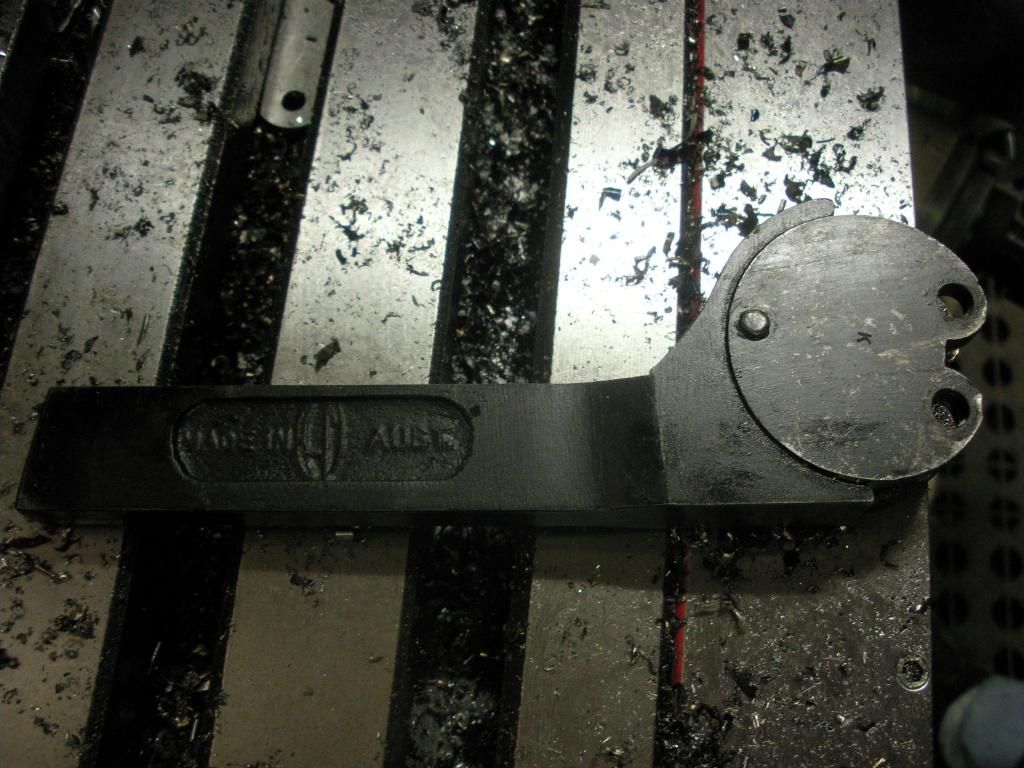
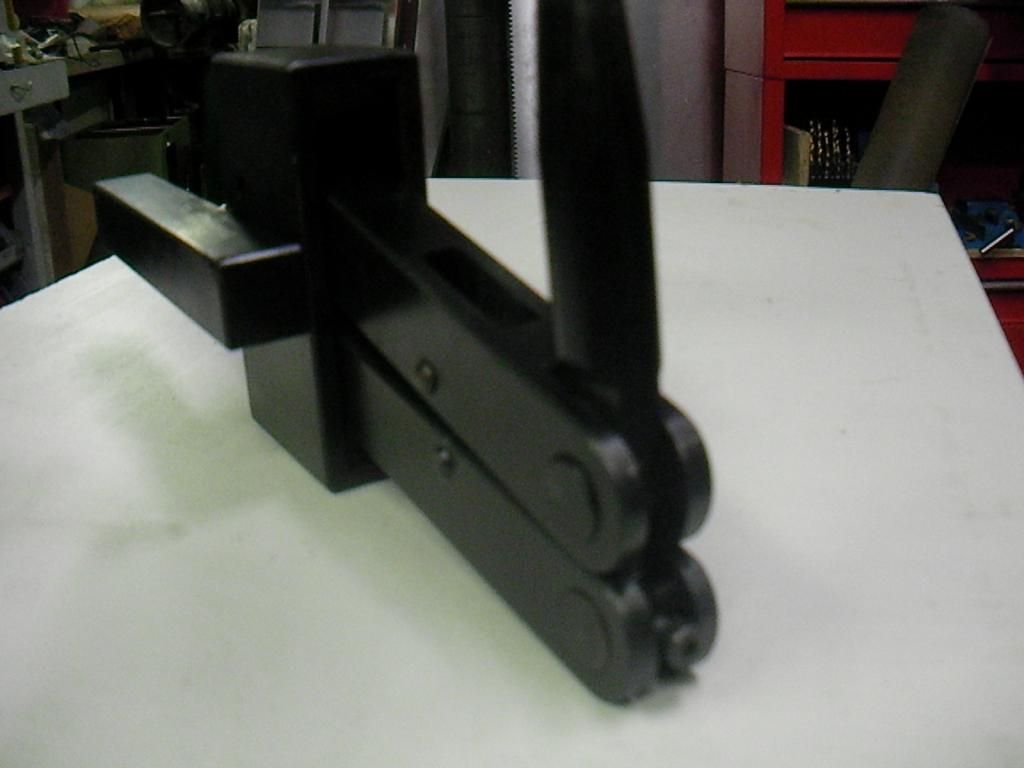
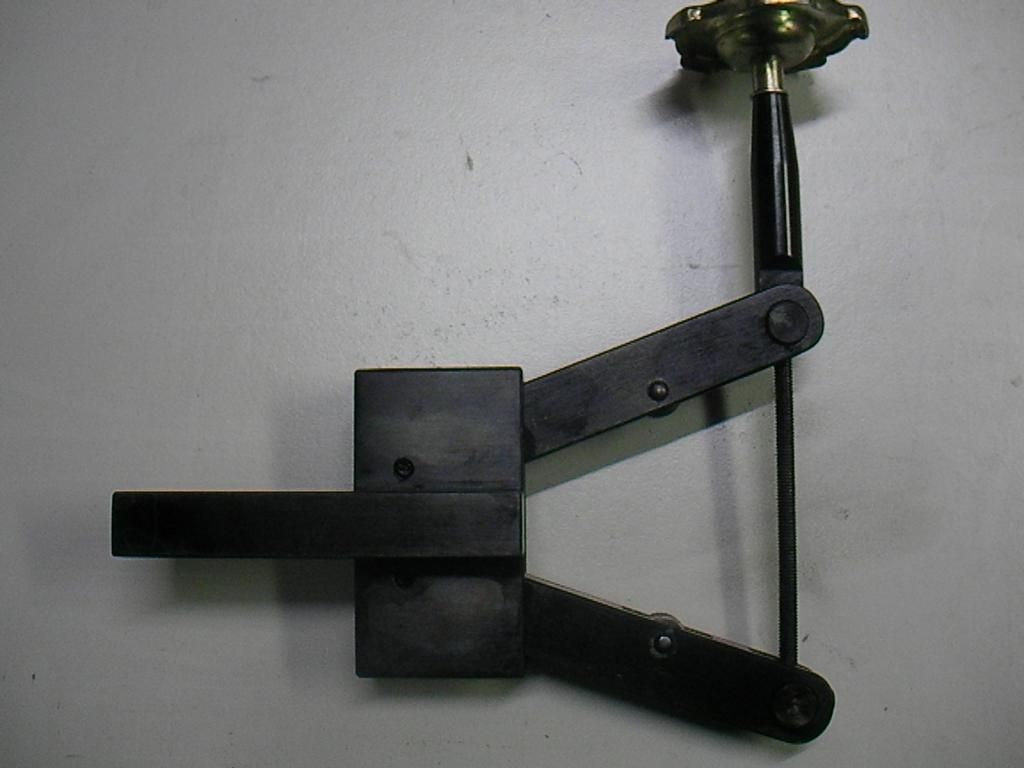
Knurling the adjusters
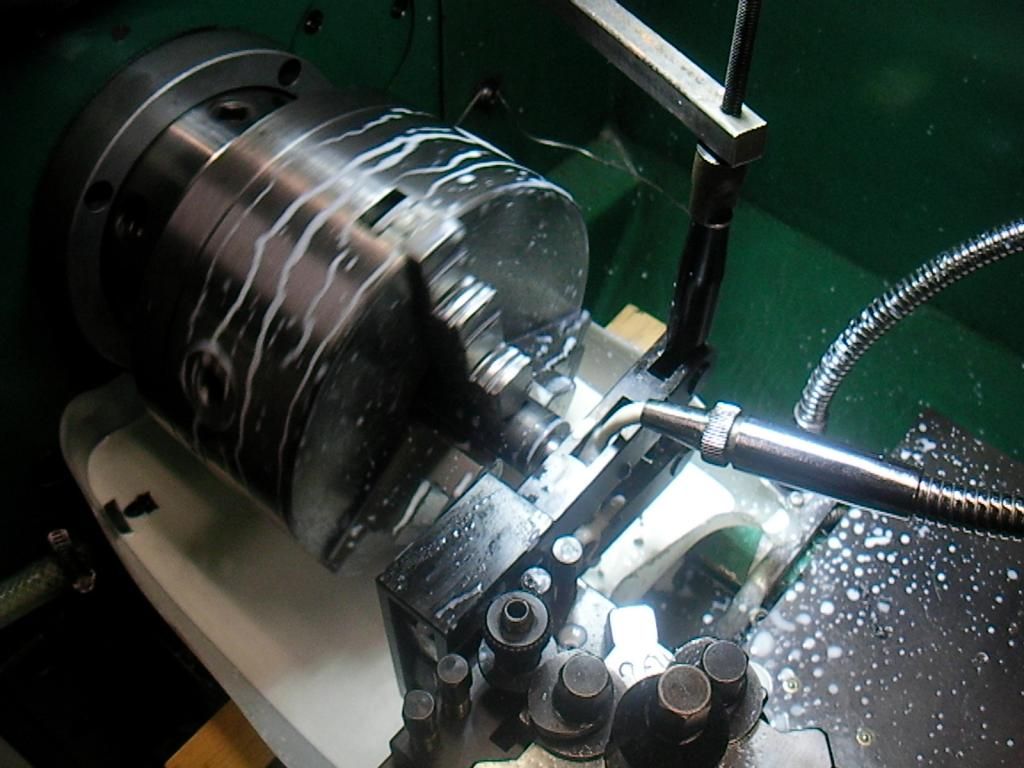
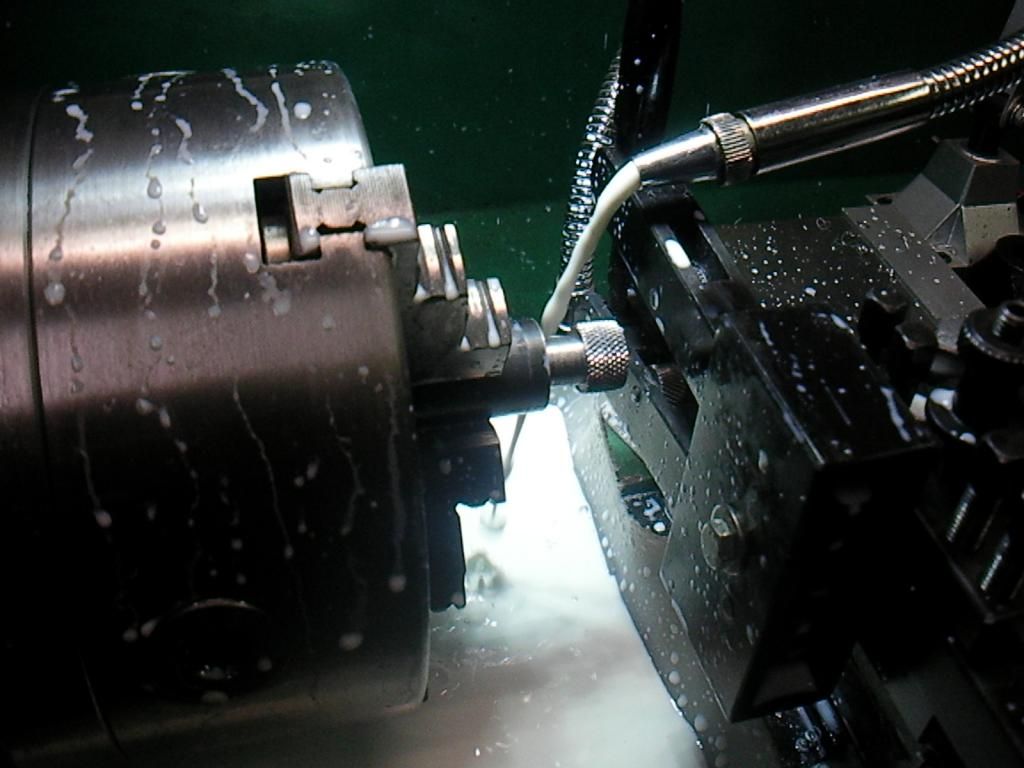
My temporary coolant set up run off the mill.
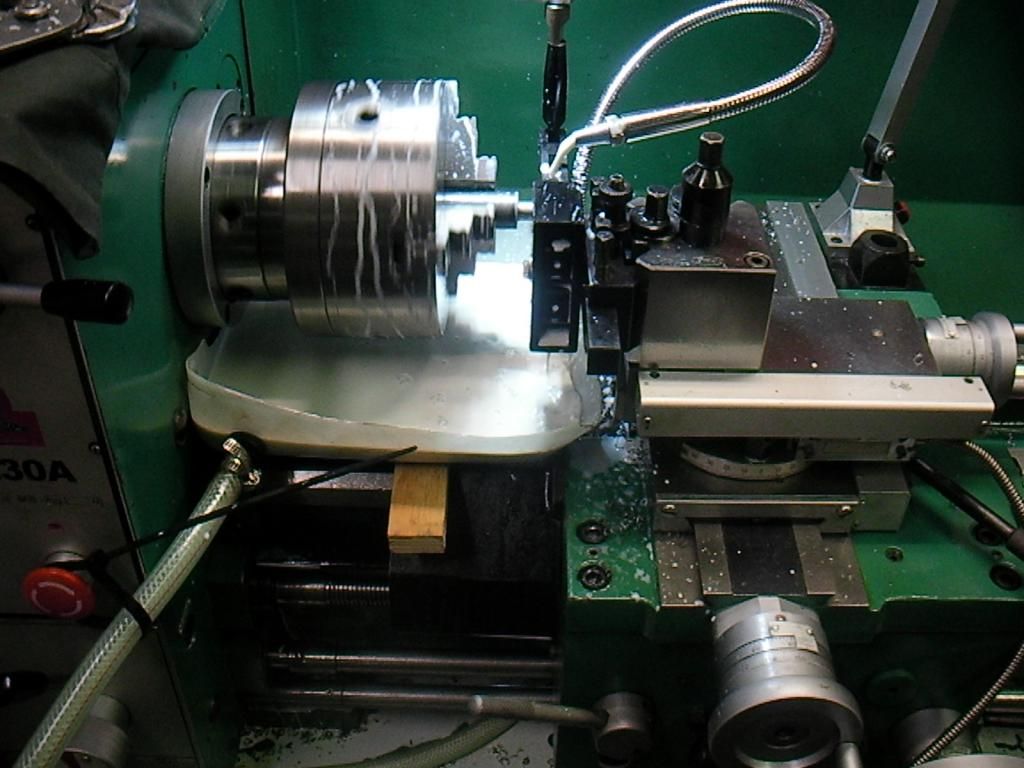
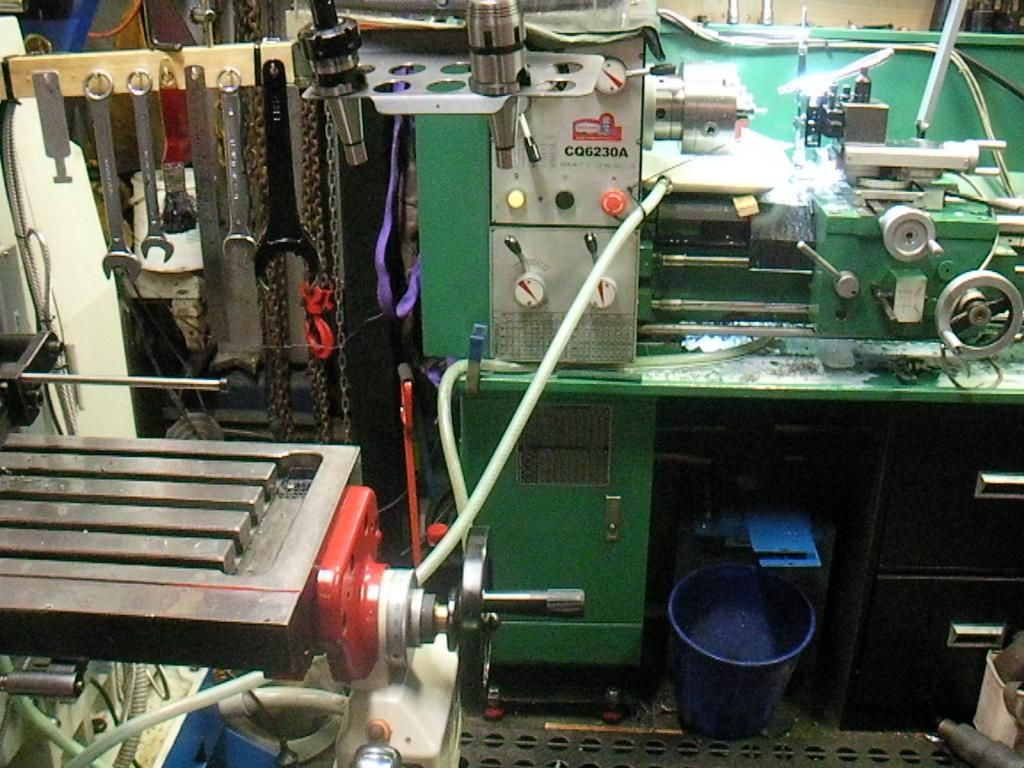
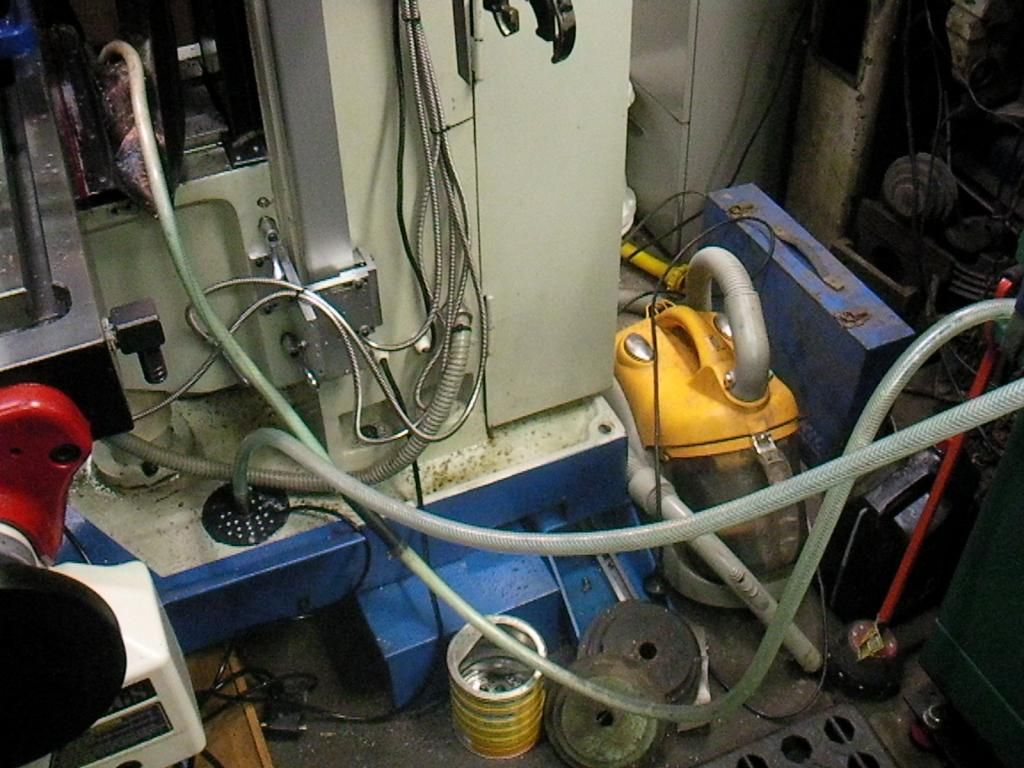
All knurled
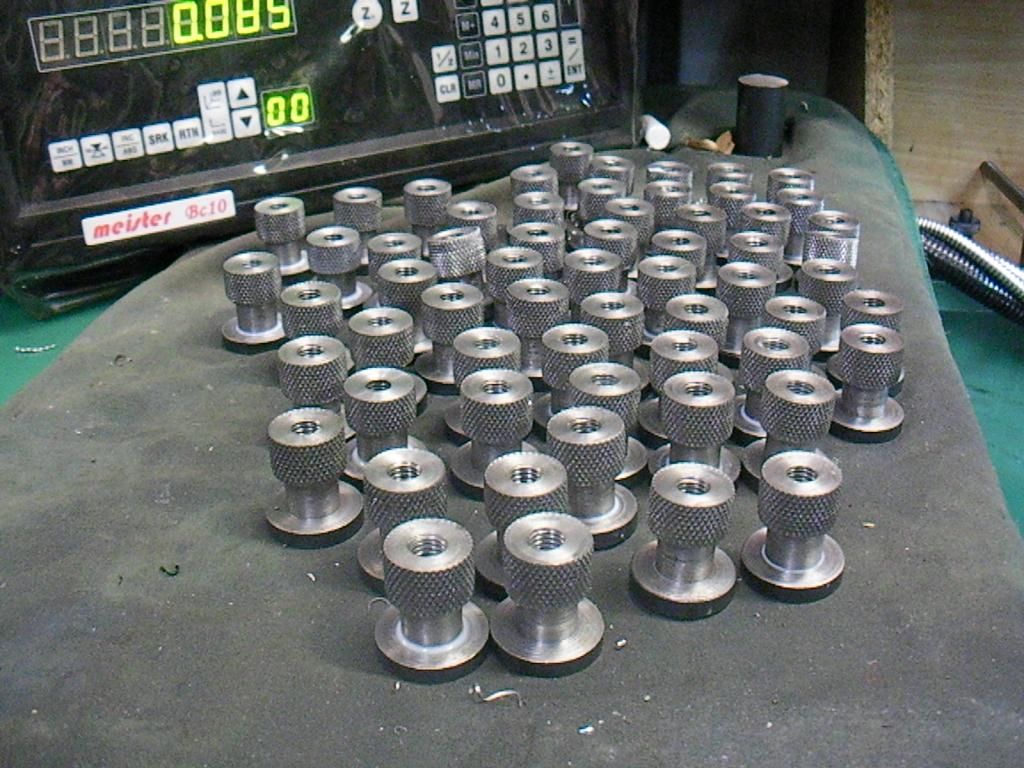
Most of the shaving that where caught after knurling.
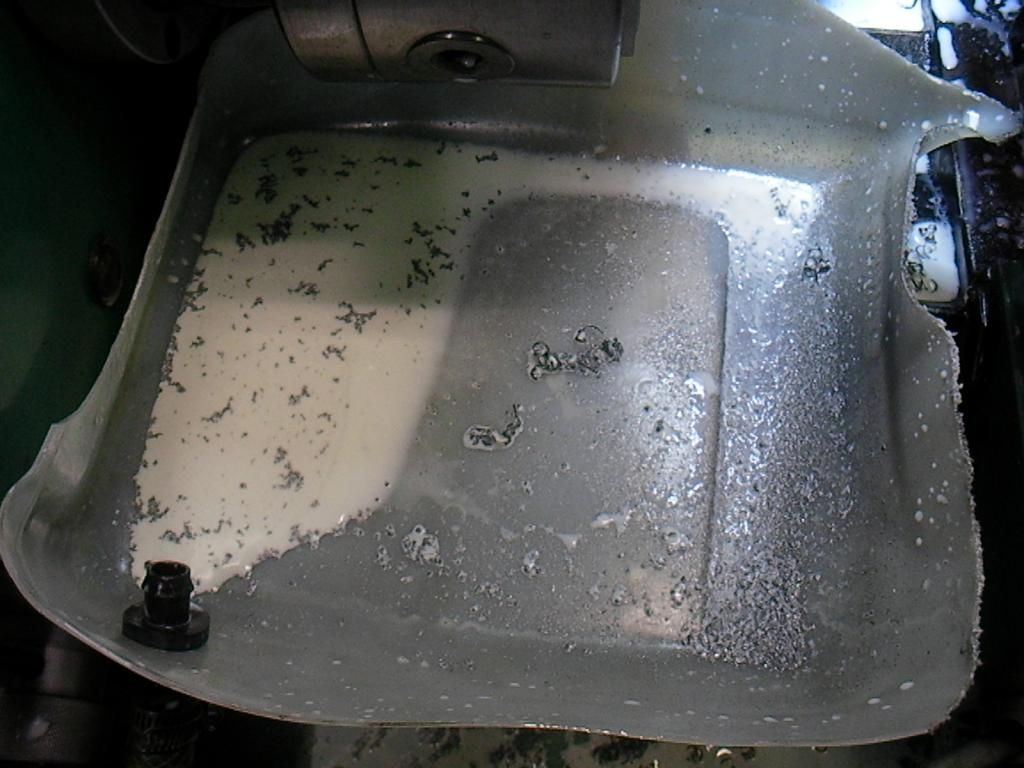
I set up these tools in 2 tool holders to do all the operations in one go
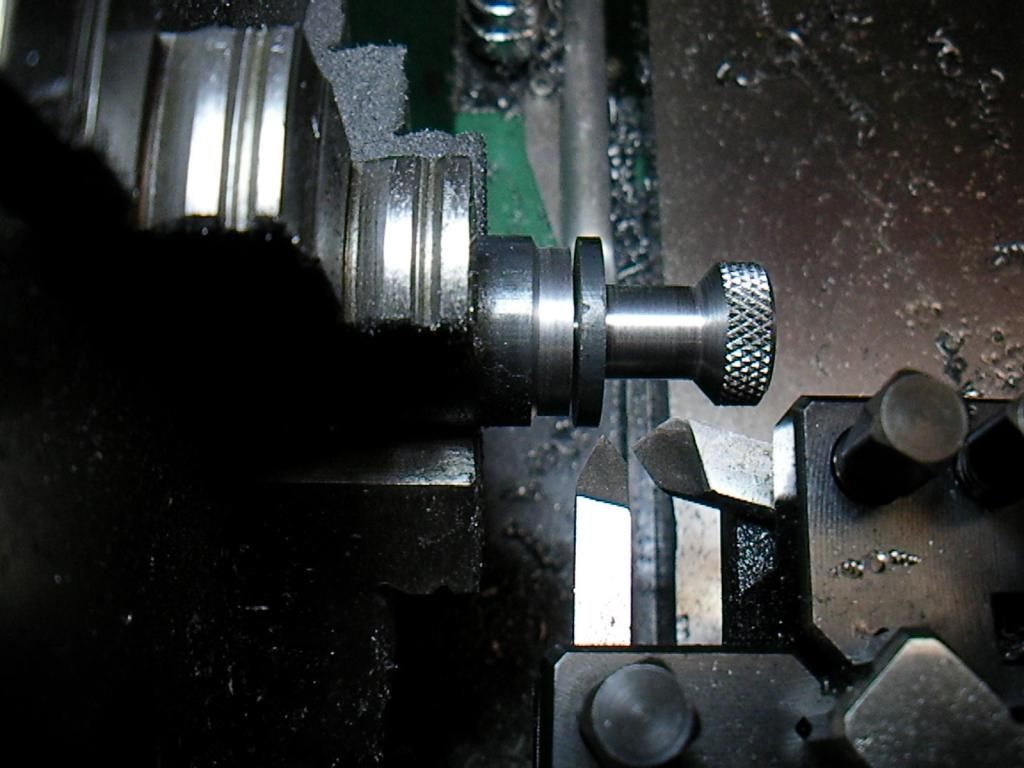
Machined the outside diameter
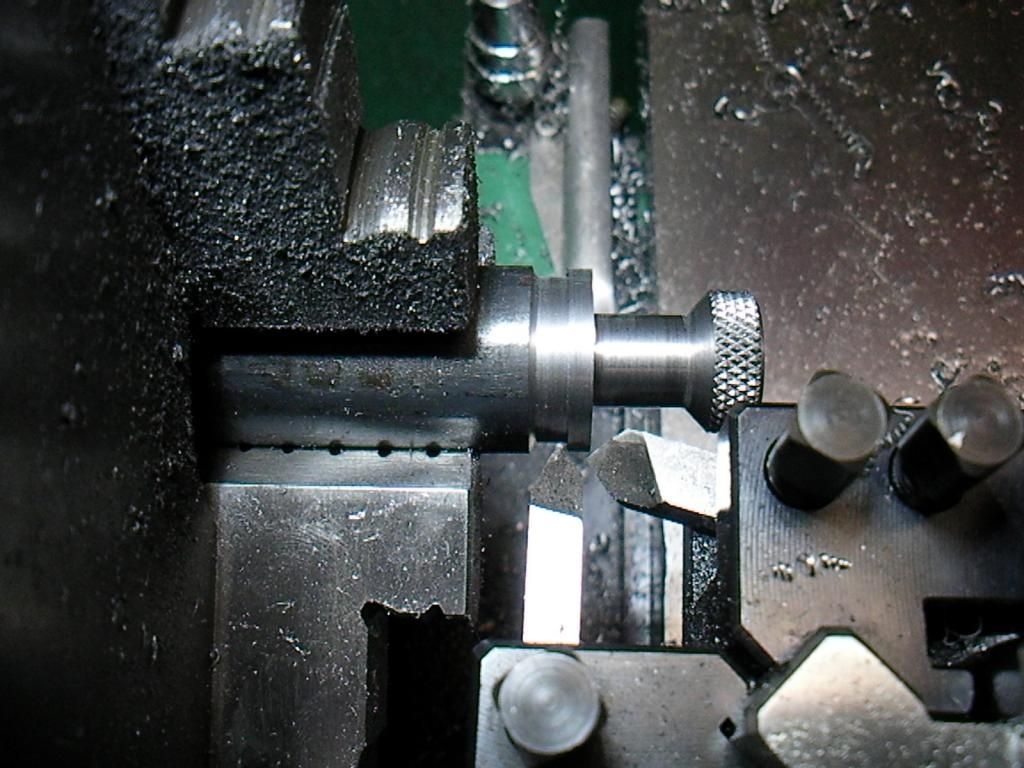
Taking of the sharp corner
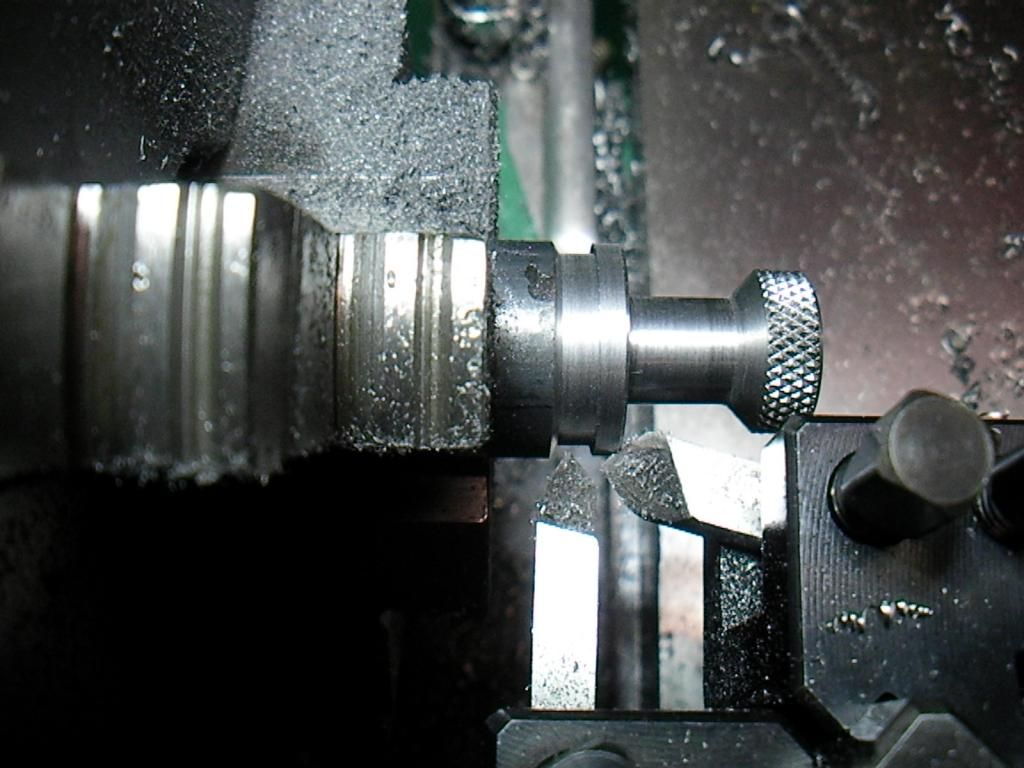
Taking off the bottom edge.
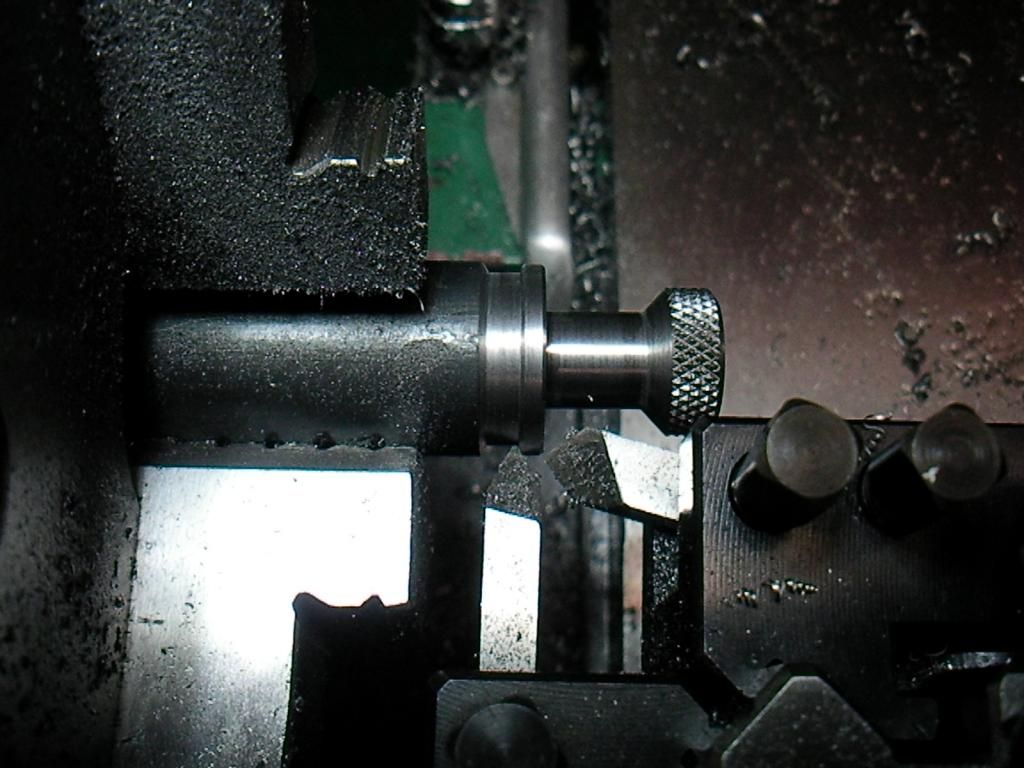
All done, I made 60 odd for spares as I never want to make these again,LOL
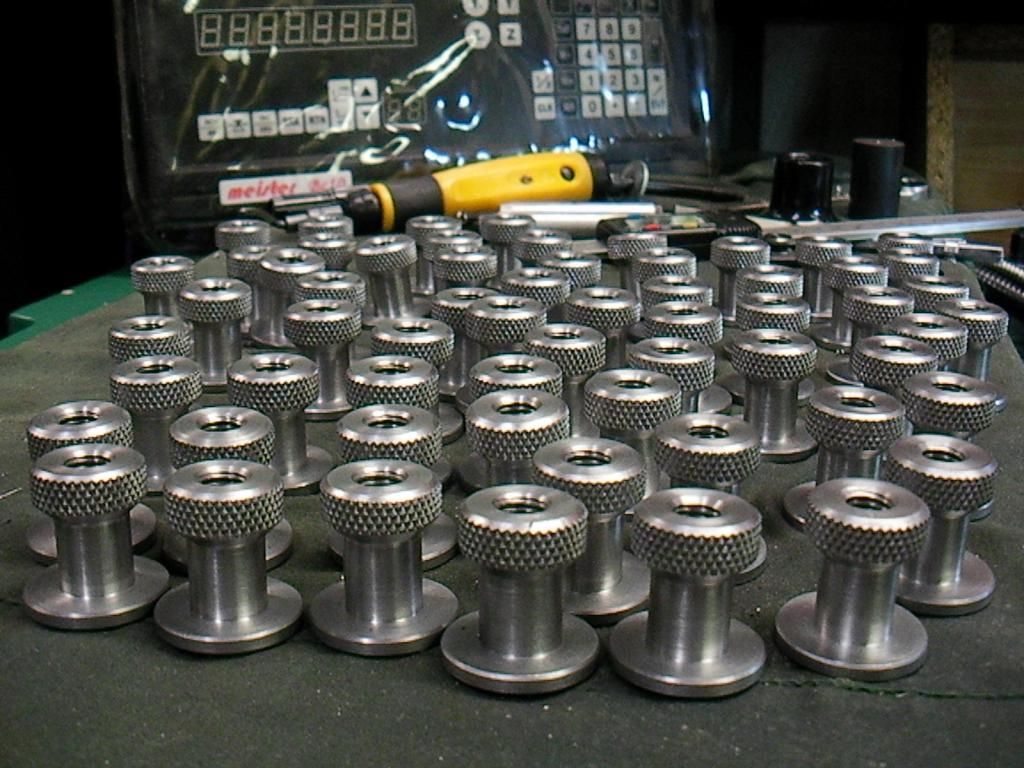
All of them heated up and dunked in oil
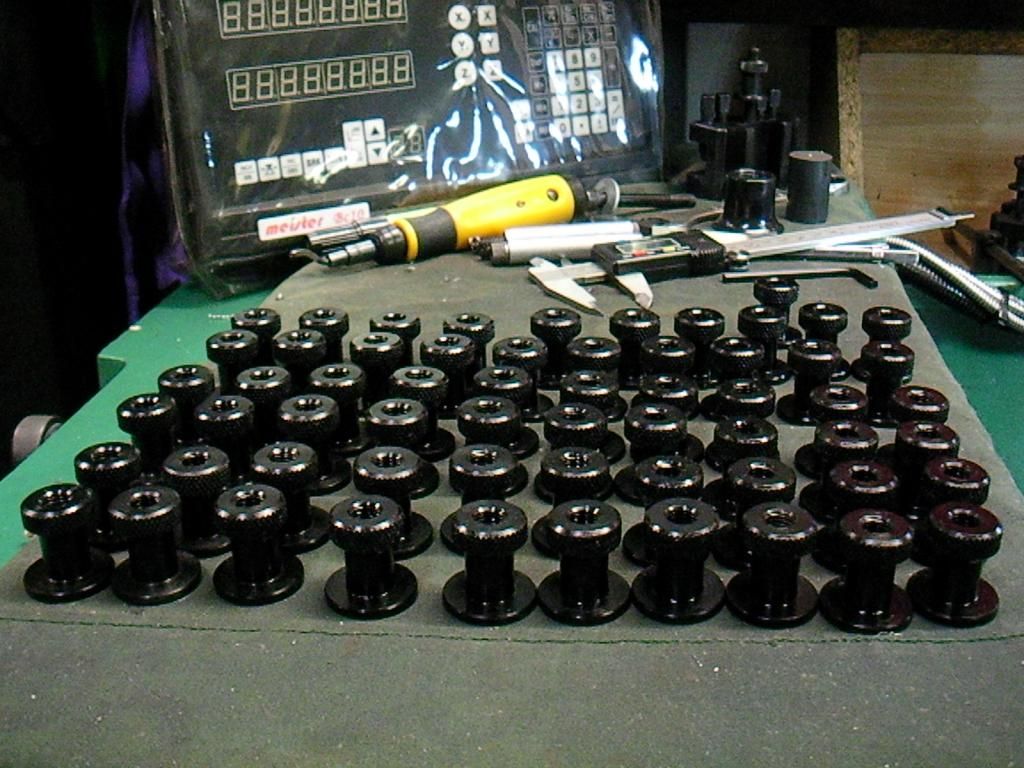
What a repetitious job
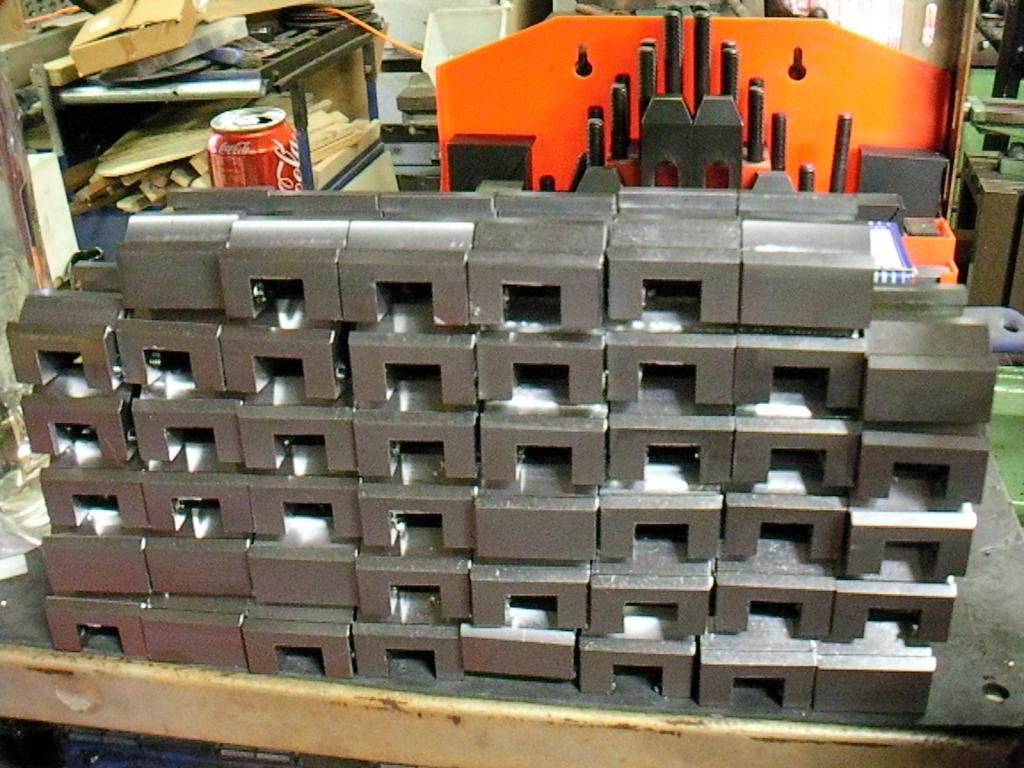
Finished
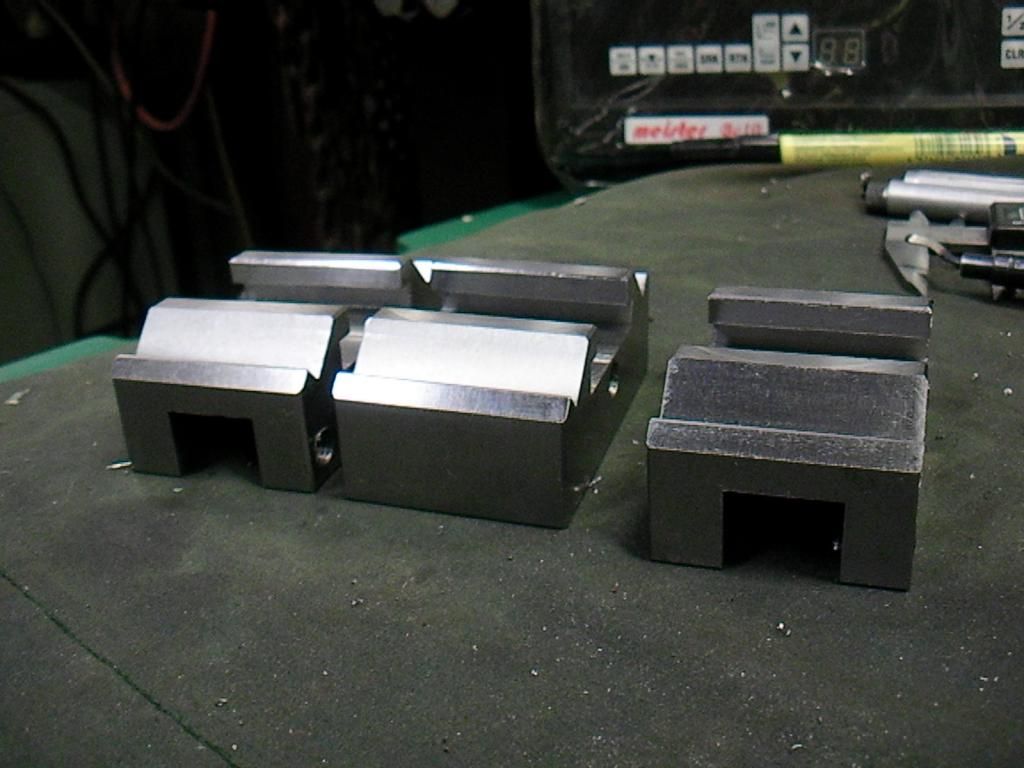
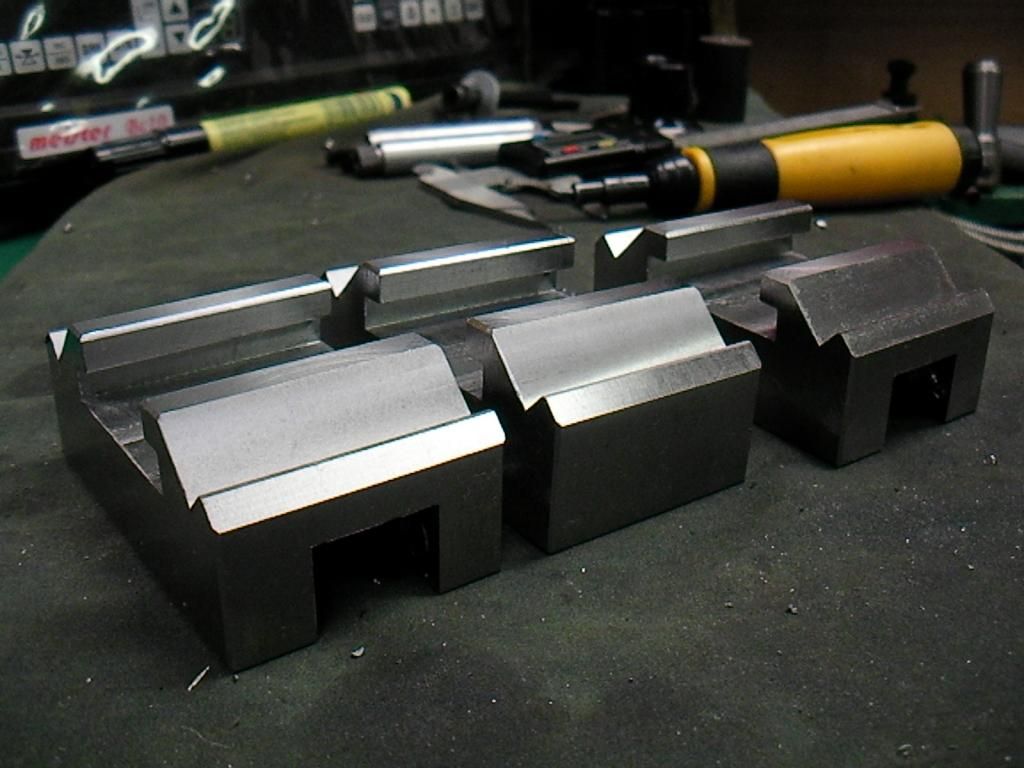
The one stuff up when I was roughing them, oh well it will get used for something like an indicator holder.
I picked up 1500 odd grub screws from the UK for just over $100, a lot cheap than buying them here for $50 odd dollar a box of 100.There is more than in the picture they are just the M8 ones need for the tool holders.
I have different lengths so I will be able to custom fit the grub screws to different size tooling I put in them
holders and will be changing my factory holders over to grub screws as well. The square he bolts where just to expensive and I would rather they didn't stick up above the holder.
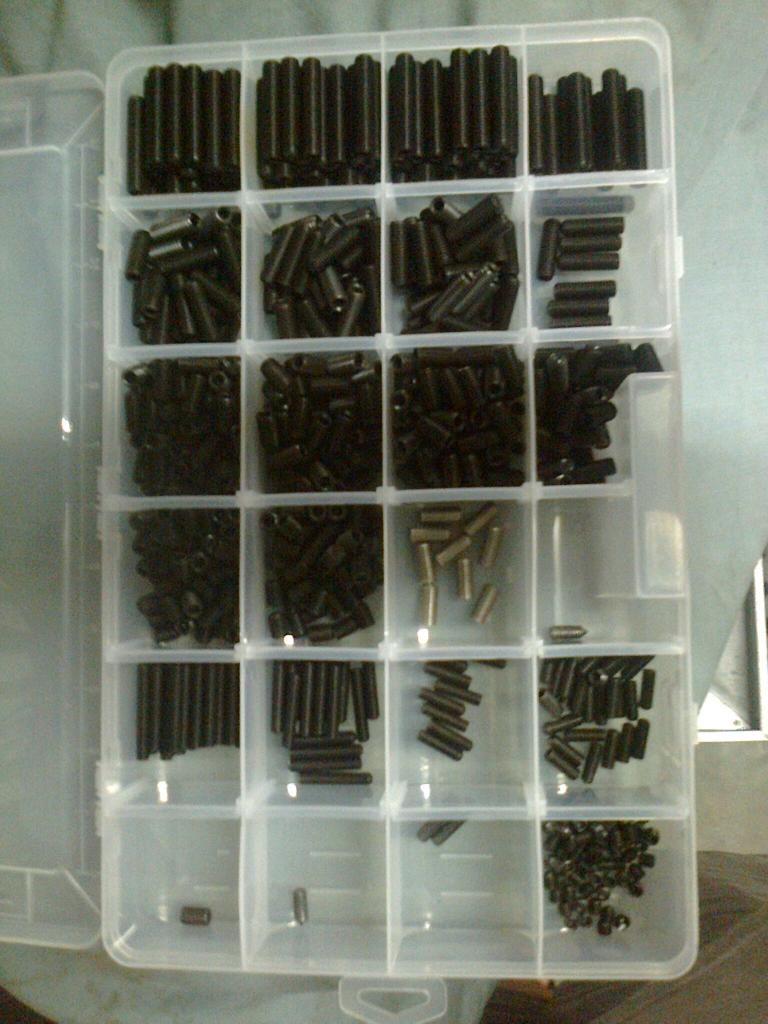
Wow that was a lot of work.
Dave