This is a carry over from a little while ago where I was discussing one of these tools.
This little device is needed by myself because I can't now get down low enough to use my 'split the line' gauge that I have used for a fair while now. I was going to use a 10mm prism but thought better of it and I am now using a 15mm one. I bought a pair of them from China at just under 10 pounds for the two.
These are now my ramblings where I used what I had to hand and designed it on the go.
---------------------------------------------------------------------------------------------
These are a few of the bits, a 2.75" length (not critical) of 3/4 ali bar, and the couple of prisms I mentioned above.
Both ends of the bar were faced up with one of my favourite cutters, a profiling tool.
A 9mm bullet point drill was was used to drill about 1" deep in one end. This drill should have been 8.9mm, but what is 0.1mm between friends.
The end of the bar was profiled down a little, just so that certain items don't become bulky, namely the locking nut.
The 1" deep hole was then tapped out to 3/8" x 40 TPI model engineering thread.
The reason I used this thread, which I use on almost all things like this, it gives a nice fine adjustment as one full revolution gives 0.025" rise or fall, the same as an imperial micrometer.
Next up was a piece of brass bar turned down to 3/8" by about 2.5" long and given the same sized thread as above. The length of these parts would need to be made so that the finished tool can be adjusted to length for your particular lathe centre height.
Another bit of brass was drilled and tapped through and a bit of straight knurl given to the outside.
The brass locking knob was given a bit of a profile by eye and the three parts assembled to check for fit.
I stepped outside my workshop door and found a bit of rough stuff which was about the right size, so I mounted it up into a soft jaw chuck (it just so happens where I had bored it was near enough the right size) so this can help me keep things straight and parallel. One end was faced, and a bit down one side as well.
This time, the piece part was drilled all the way through and the usual thread cut through it.
A small recess was formed into the bottom of the base just so that there is less chance of a bit of swarf kicking the tool off upright.
The part was turned around in the soft jaws and a bit of profiling was done to reduce weight and make it look a little nicer. All the bits were then assembled to make sure I can get the adjustment I need.
So this is as far as I go now, I will finish the write up tomorrow if all goes well.
John
This little device is needed by myself because I can't now get down low enough to use my 'split the line' gauge that I have used for a fair while now. I was going to use a 10mm prism but thought better of it and I am now using a 15mm one. I bought a pair of them from China at just under 10 pounds for the two.
These are now my ramblings where I used what I had to hand and designed it on the go.
---------------------------------------------------------------------------------------------
These are a few of the bits, a 2.75" length (not critical) of 3/4 ali bar, and the couple of prisms I mentioned above.
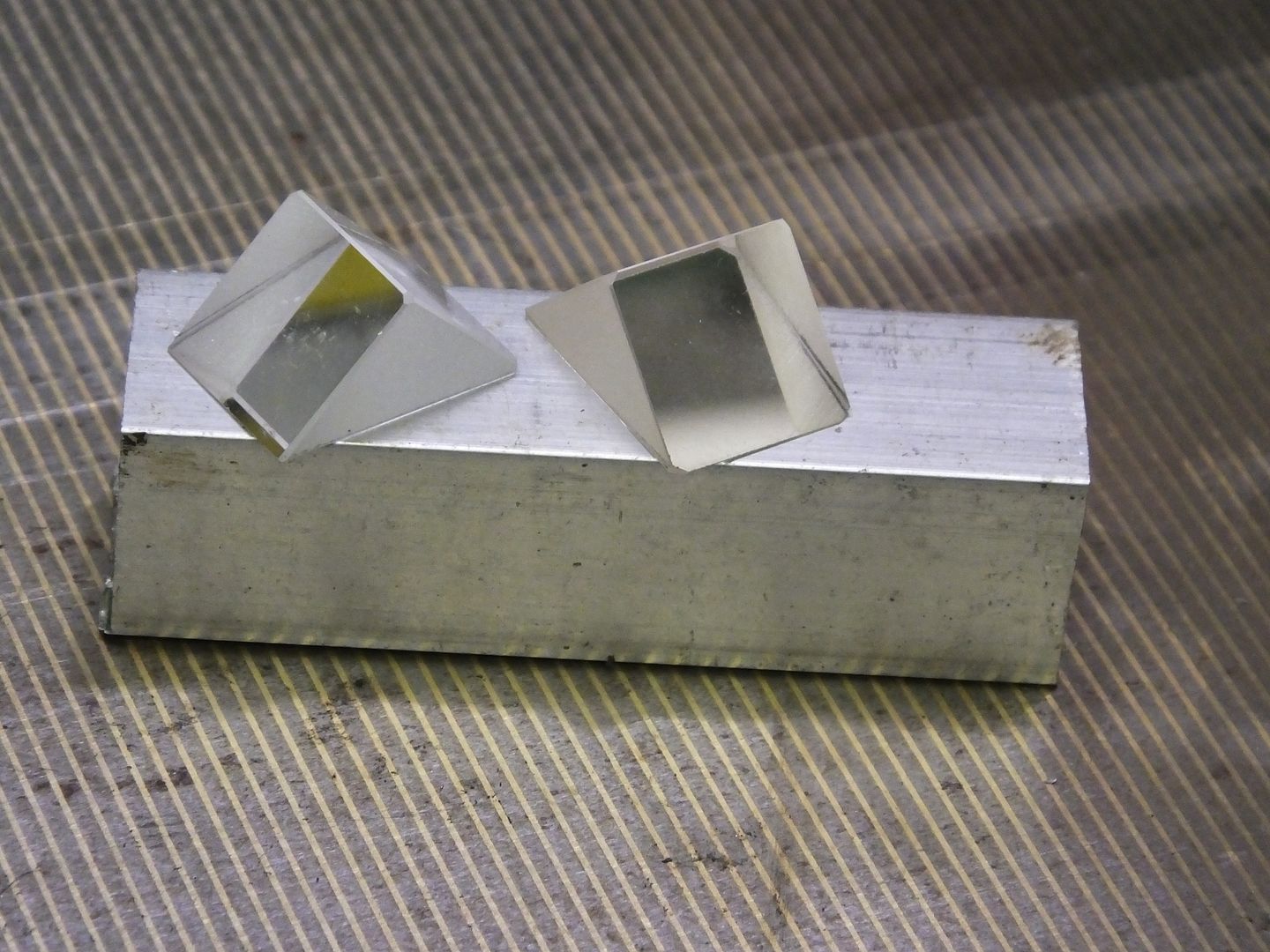
Both ends of the bar were faced up with one of my favourite cutters, a profiling tool.
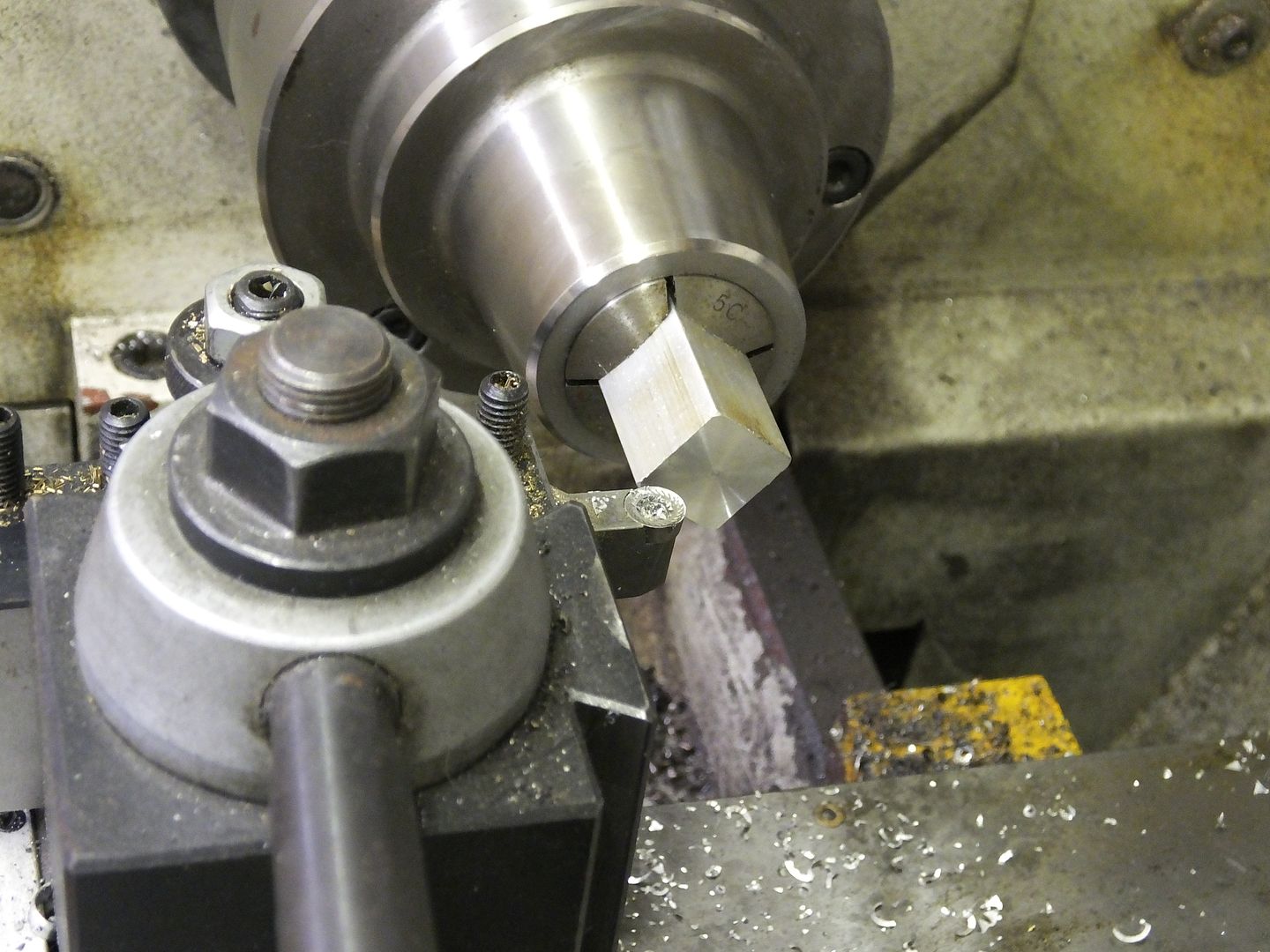
A 9mm bullet point drill was was used to drill about 1" deep in one end. This drill should have been 8.9mm, but what is 0.1mm between friends.
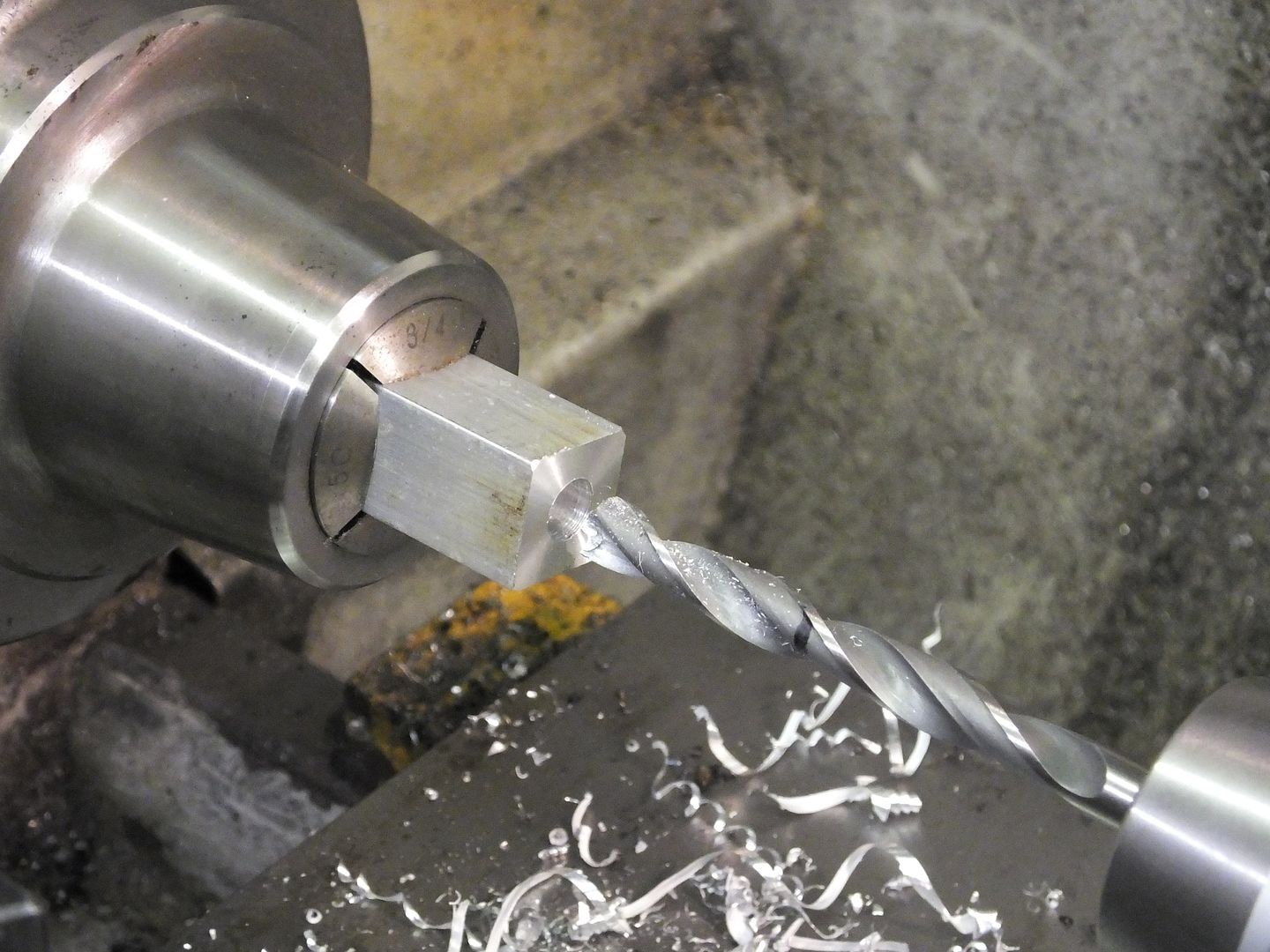
The end of the bar was profiled down a little, just so that certain items don't become bulky, namely the locking nut.
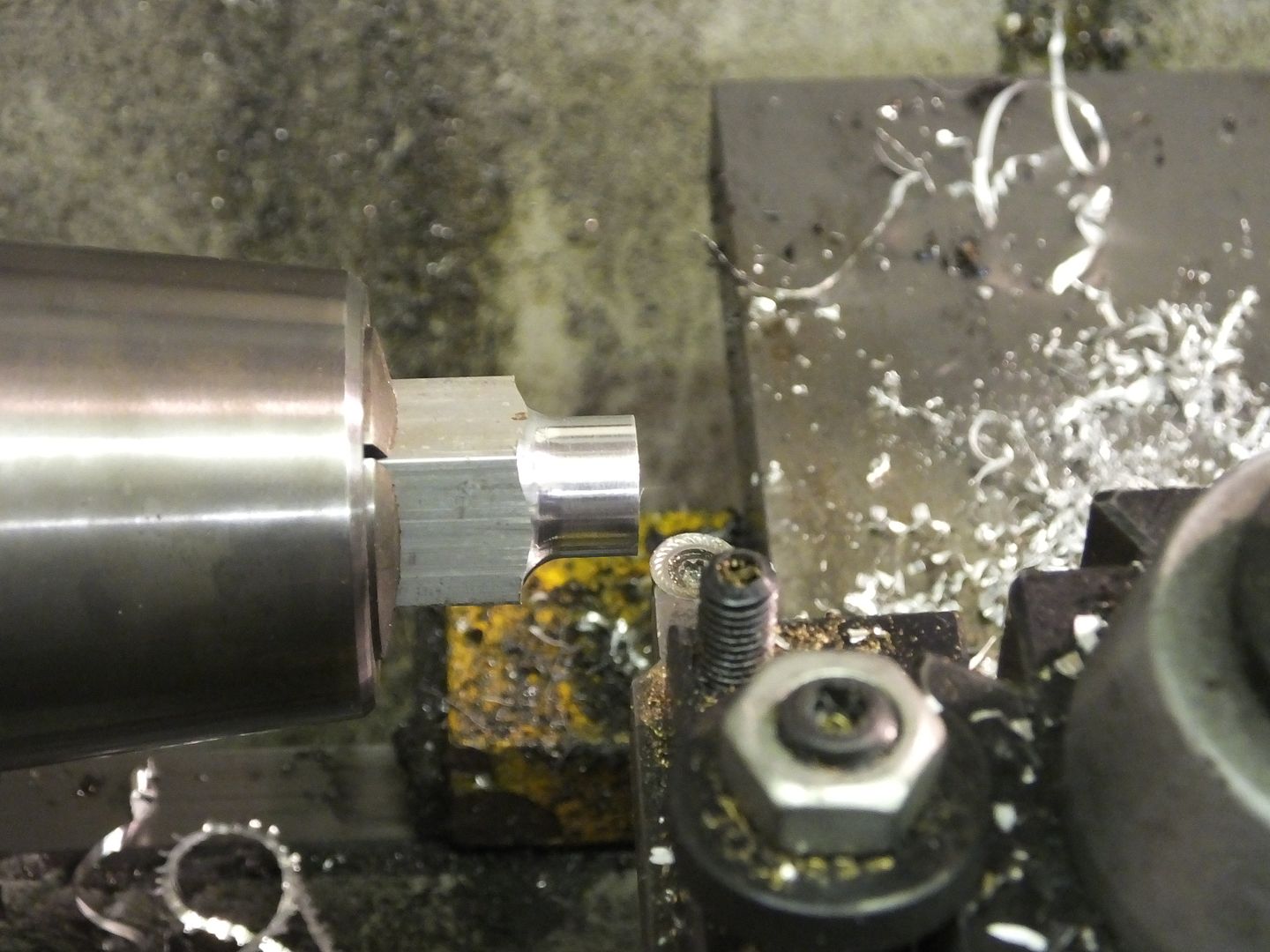
The 1" deep hole was then tapped out to 3/8" x 40 TPI model engineering thread.
The reason I used this thread, which I use on almost all things like this, it gives a nice fine adjustment as one full revolution gives 0.025" rise or fall, the same as an imperial micrometer.
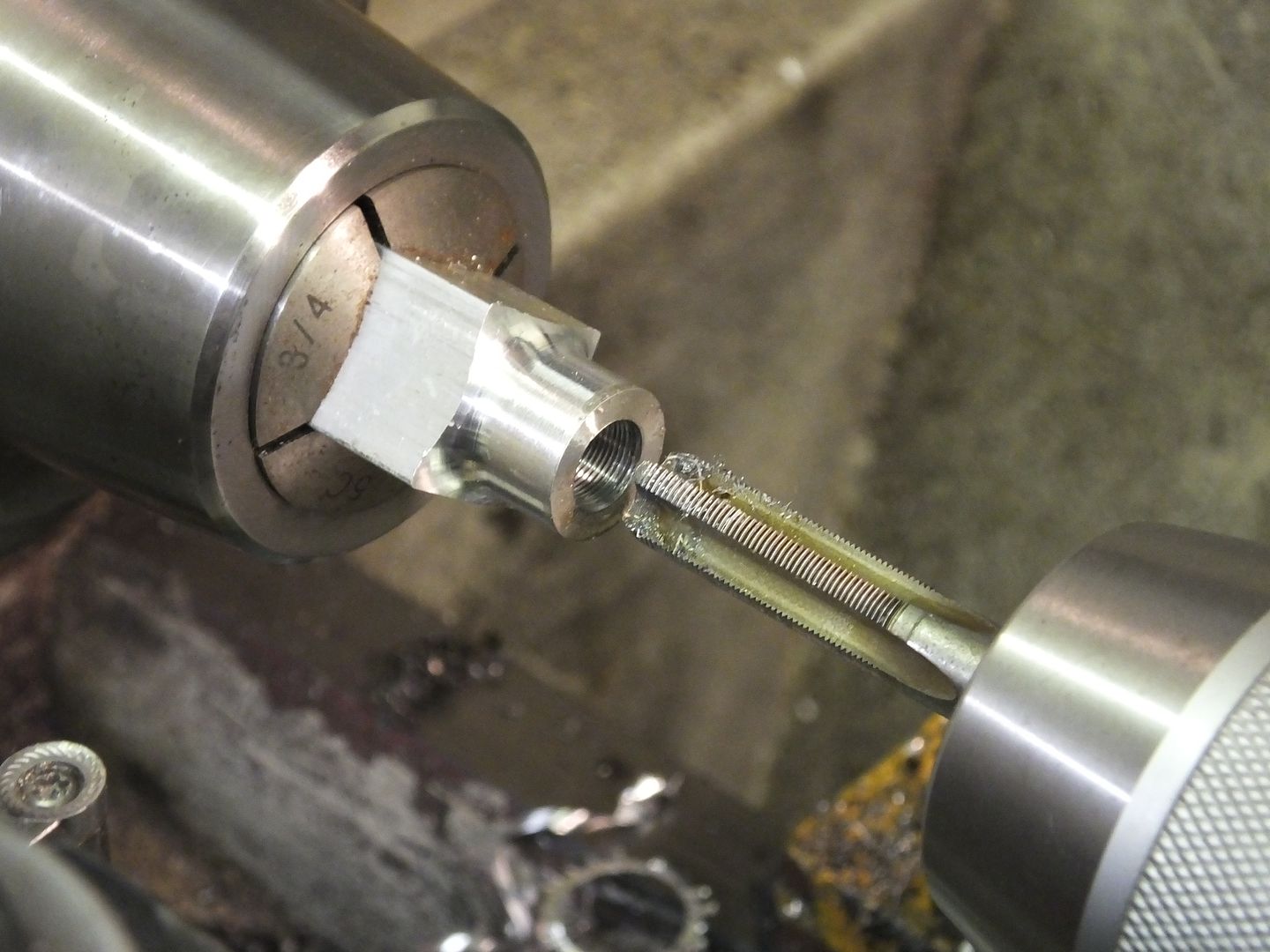
Next up was a piece of brass bar turned down to 3/8" by about 2.5" long and given the same sized thread as above. The length of these parts would need to be made so that the finished tool can be adjusted to length for your particular lathe centre height.
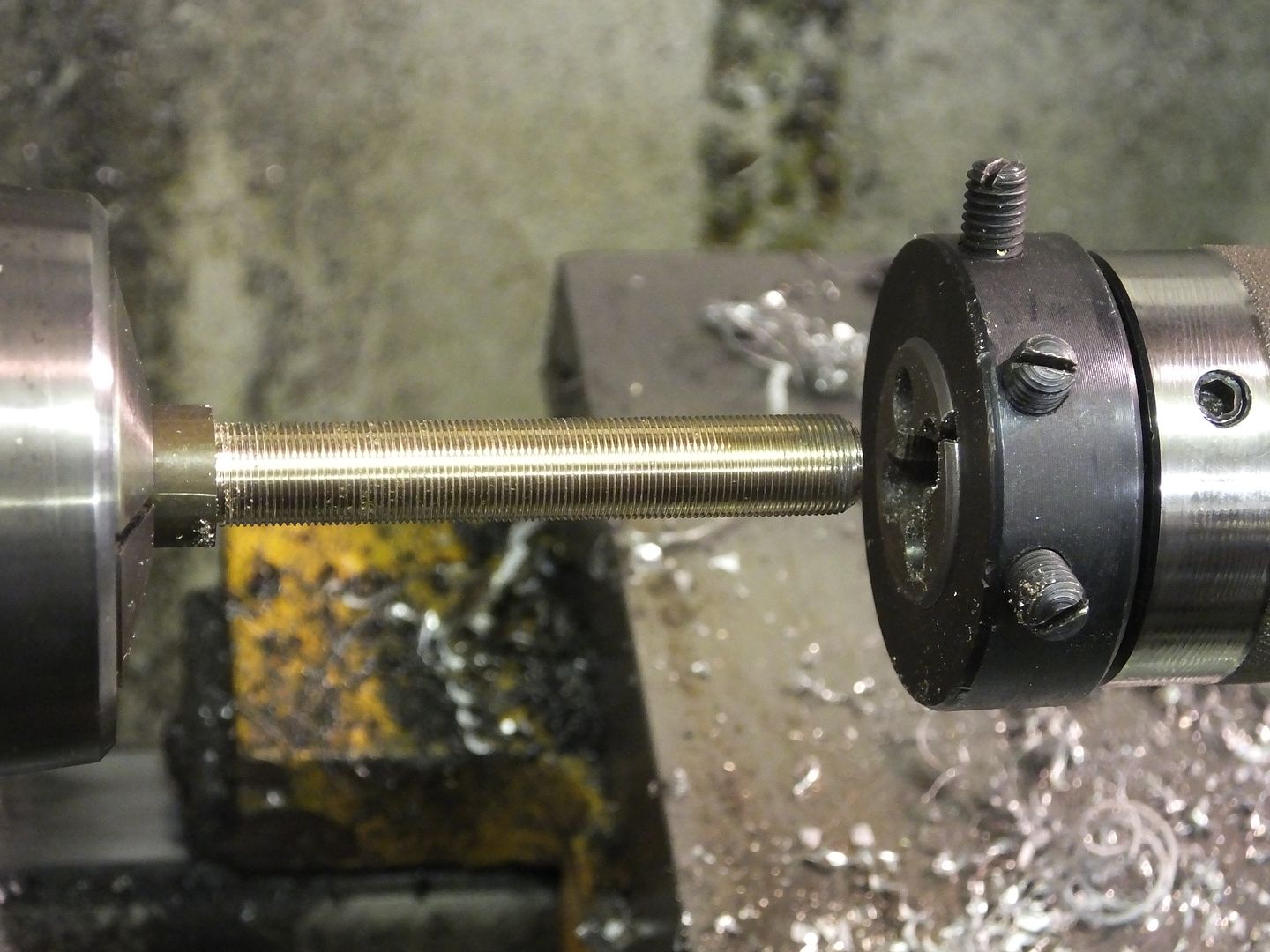
Another bit of brass was drilled and tapped through and a bit of straight knurl given to the outside.
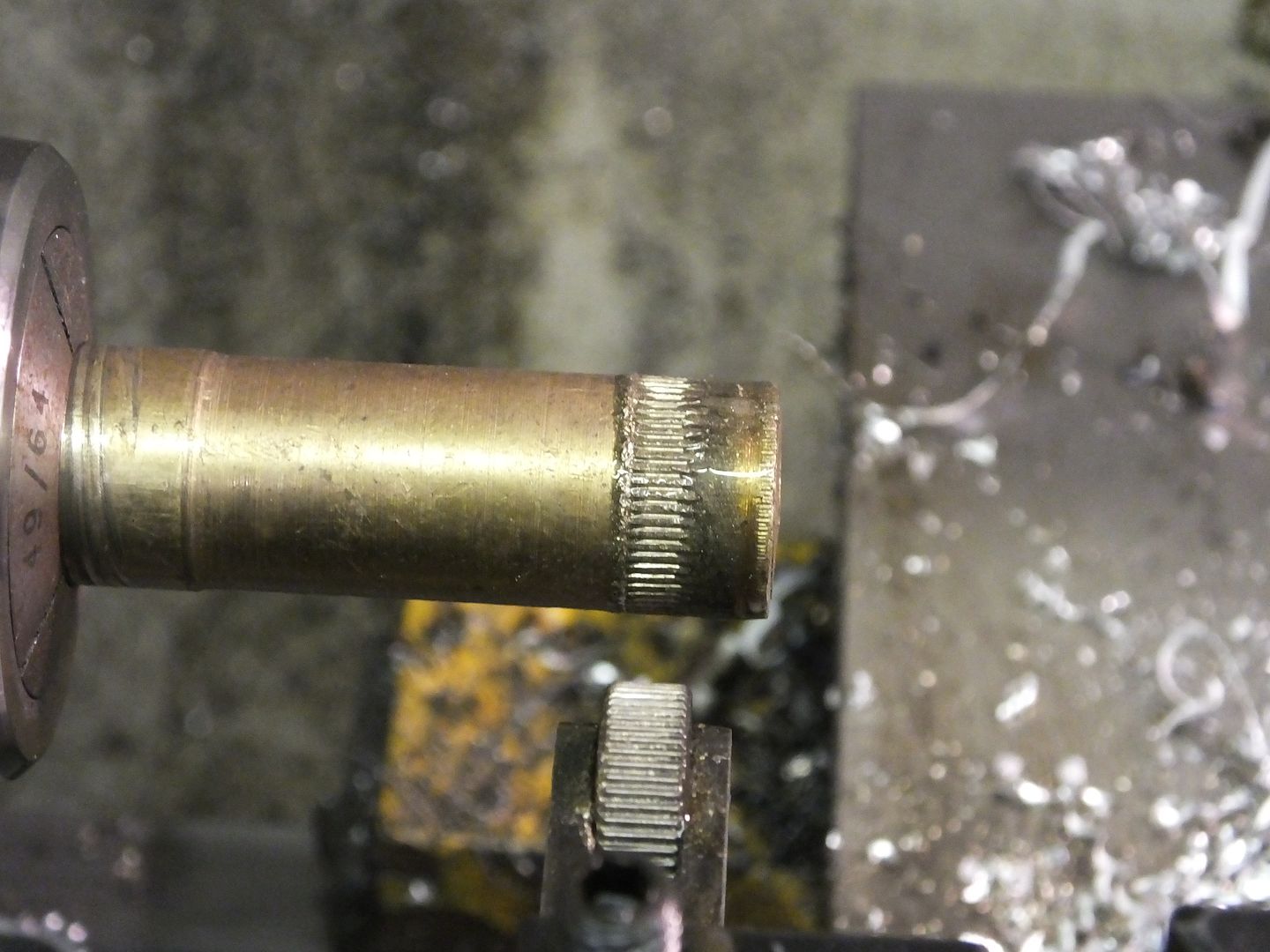
The brass locking knob was given a bit of a profile by eye and the three parts assembled to check for fit.
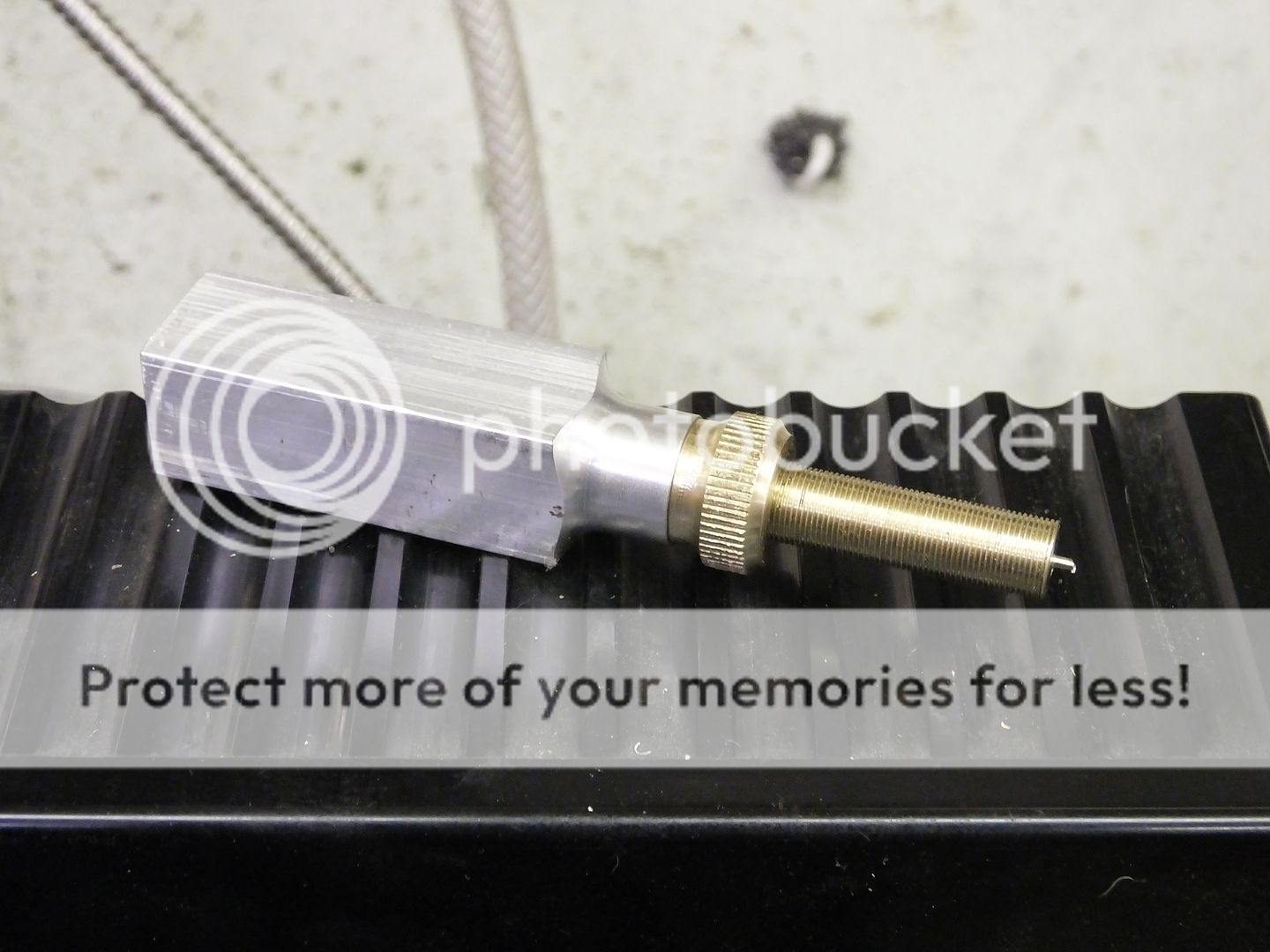
I stepped outside my workshop door and found a bit of rough stuff which was about the right size, so I mounted it up into a soft jaw chuck (it just so happens where I had bored it was near enough the right size) so this can help me keep things straight and parallel. One end was faced, and a bit down one side as well.
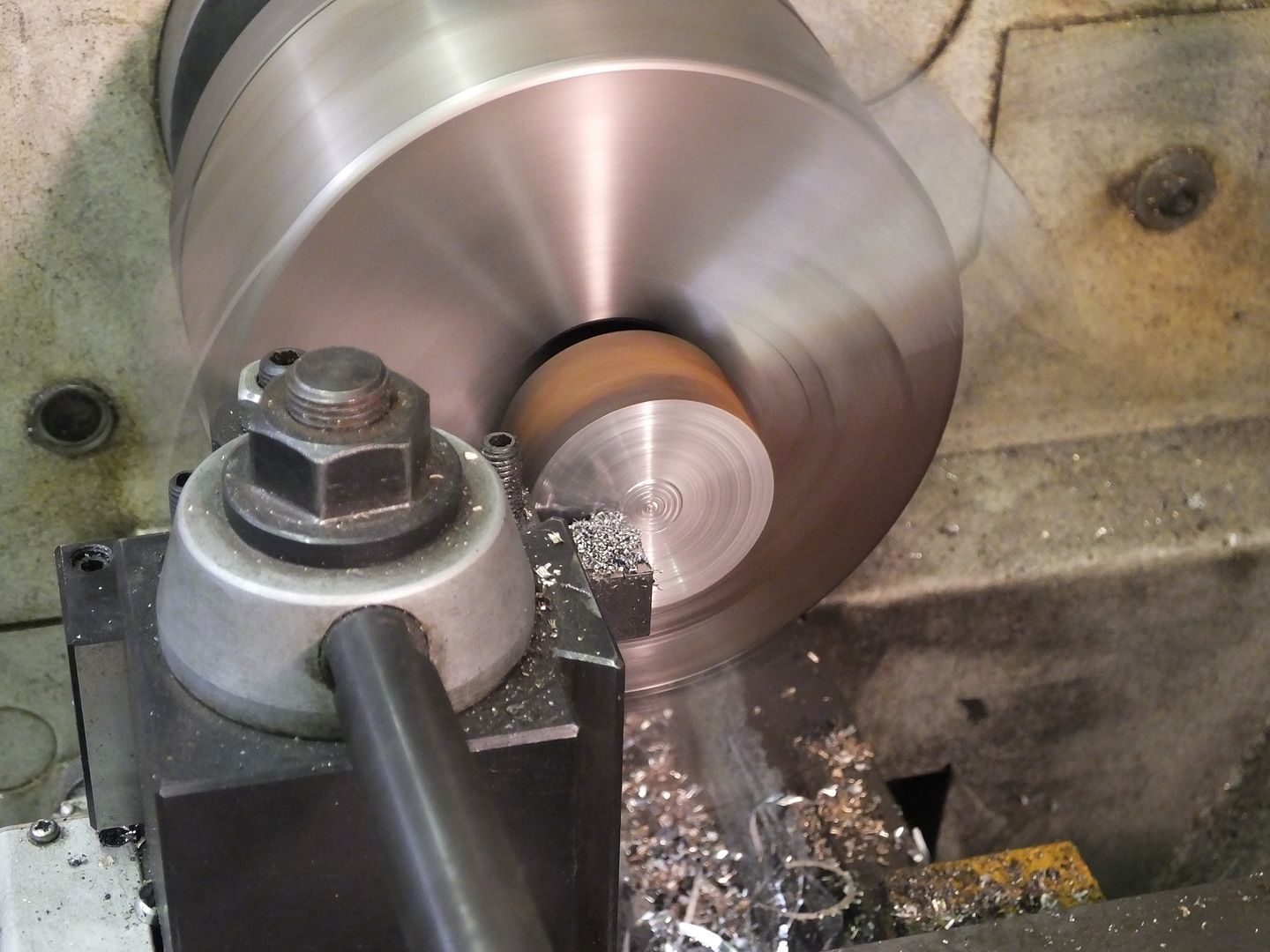
This time, the piece part was drilled all the way through and the usual thread cut through it.
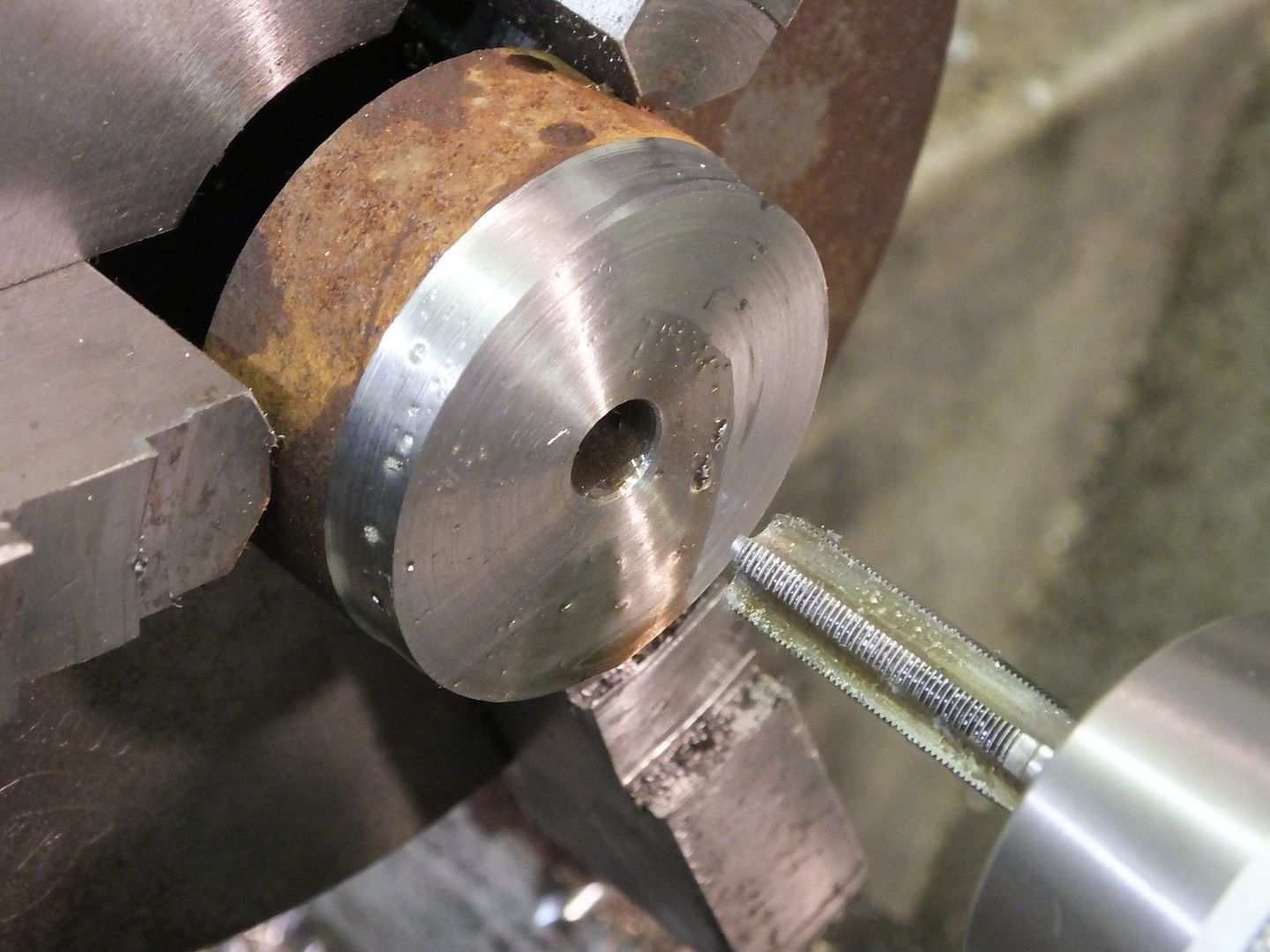
A small recess was formed into the bottom of the base just so that there is less chance of a bit of swarf kicking the tool off upright.
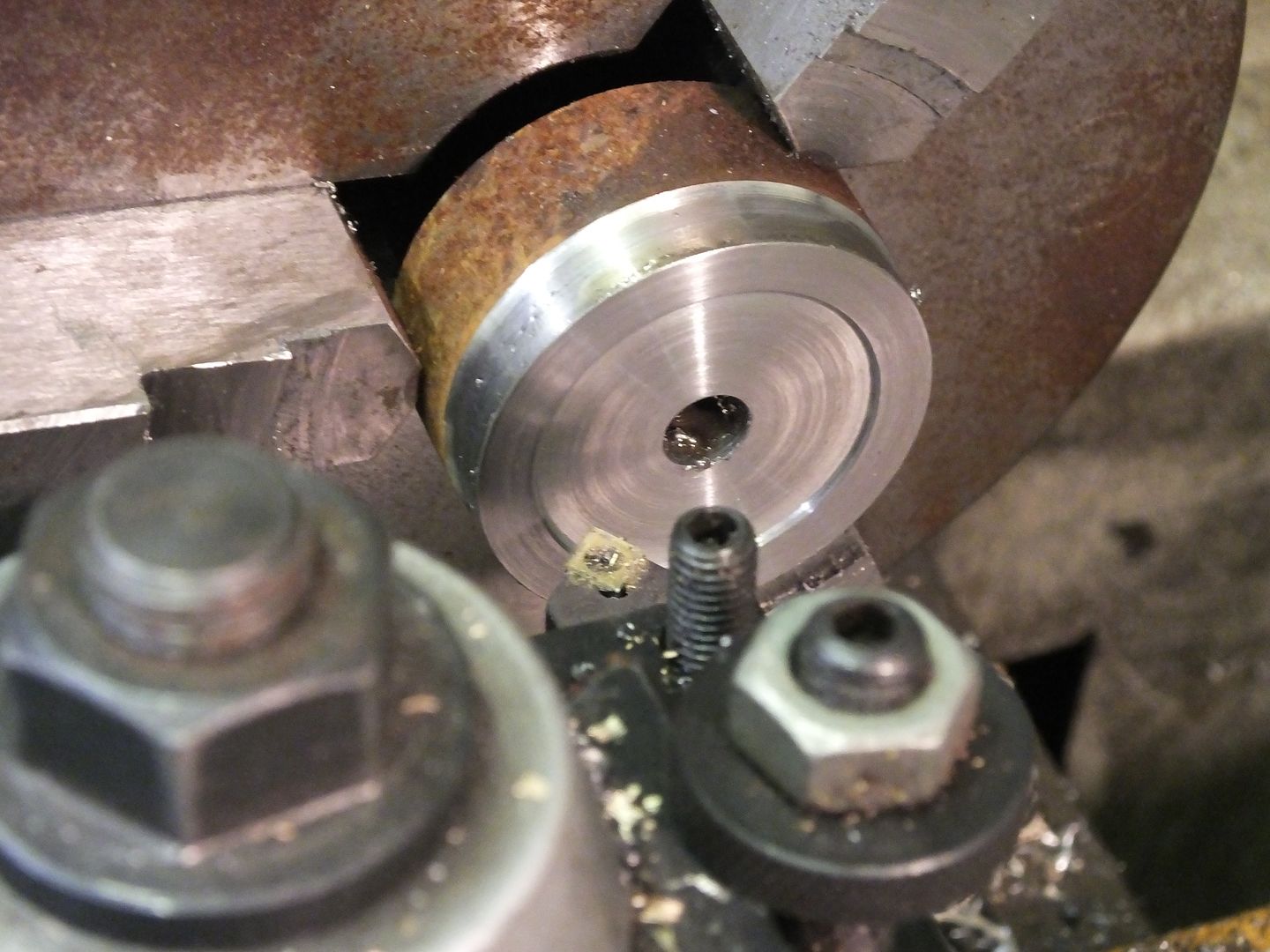
The part was turned around in the soft jaws and a bit of profiling was done to reduce weight and make it look a little nicer. All the bits were then assembled to make sure I can get the adjustment I need.
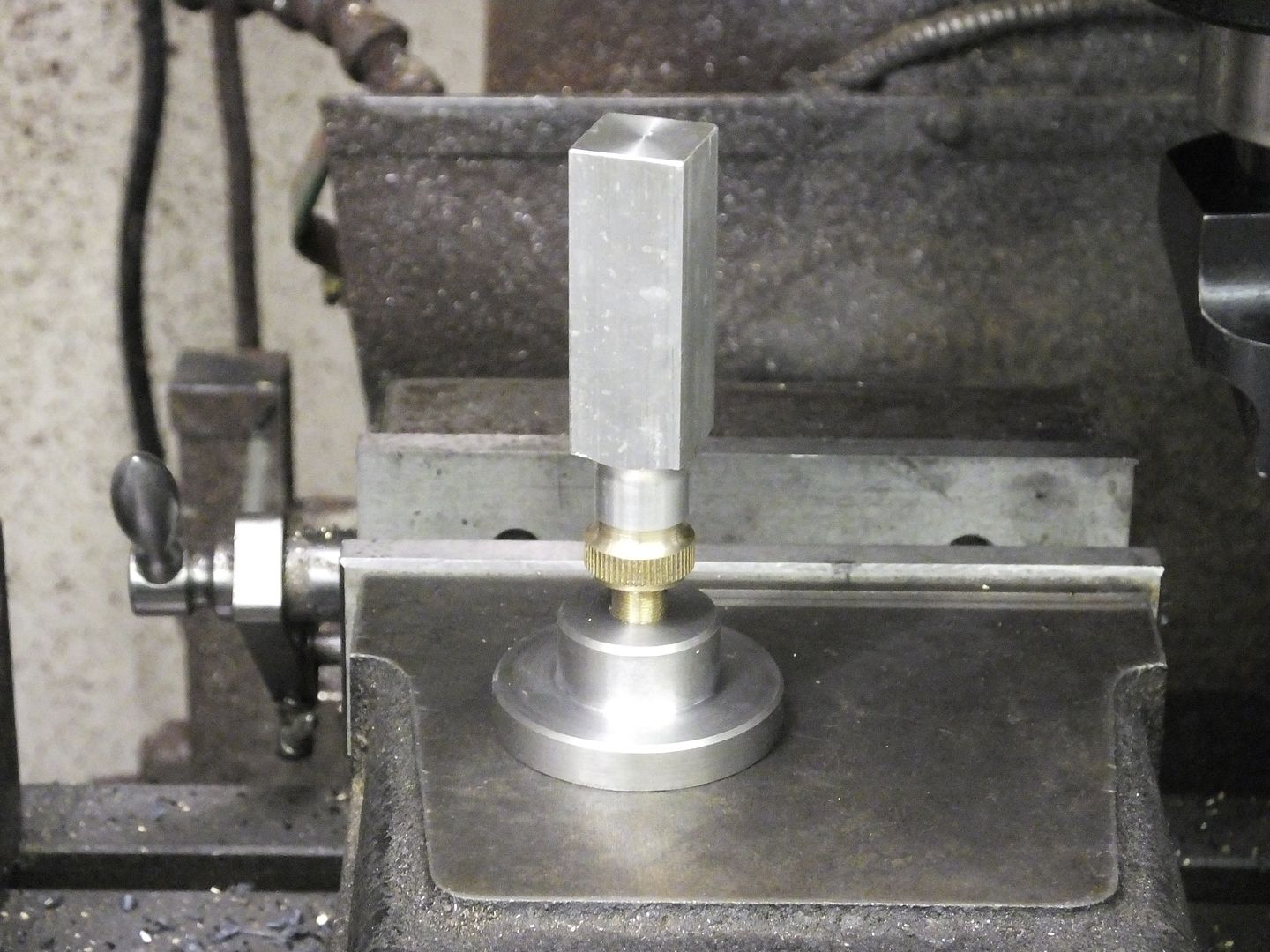
So this is as far as I go now, I will finish the write up tomorrow if all goes well.
John