When I built the flywheels for my Kerzel engine, I drilled and tapped each hub 3 places at 120 degrees for set screws, to hold them to the crankshaft. I believe it was Tel who pointed out that this was incorrect. Two setscrews at 90 degrees apart are far better and will lock things more securely. Now on a steam engine, I would probably have been okay with that, because generaly you will have the flywheels on and off a maximum of about 5 times during the build.---BUT---On this I.C. engine, I have been loosening those screws off and turning the flywheels to reposition them to adjust the way the counterweight arms pivotted and for various and sundry other reasons, to the point where my crankshaft is all scored up, and the set screws are all getting worn to the point where the allen wrench slips in them.--And the flywheels are seizing onto the shaft, becoming so frozen in place that they are very difficult to adjust rotationally. Since I have to pull the crankshaft out to install the roller bearings I have ordered, I thought this would be a good time to design and build some other type of locking mechanism for the flywheel hubs. Luckily, the flywheel hubs are 3/4" o.d. with a 3/8" bore, so I have some meat to work with. My plan is to open the bores out to 1/2" dia. and insert new steel locking type hubs into them. This is the drawing of what I plan to do---and for all you eagle eyes out there who will want to tell me that the head on a #5-40 shcs won't fit into a 3/16" c'bore, I know that. Its just that I didn't have room to make the extended portion of the hubs longer than 1/4", and I do have a 3/16" 2-flute milling cutter, so I planned on turning the heads down to 0.180" diameter.
View attachment HUB.PDF
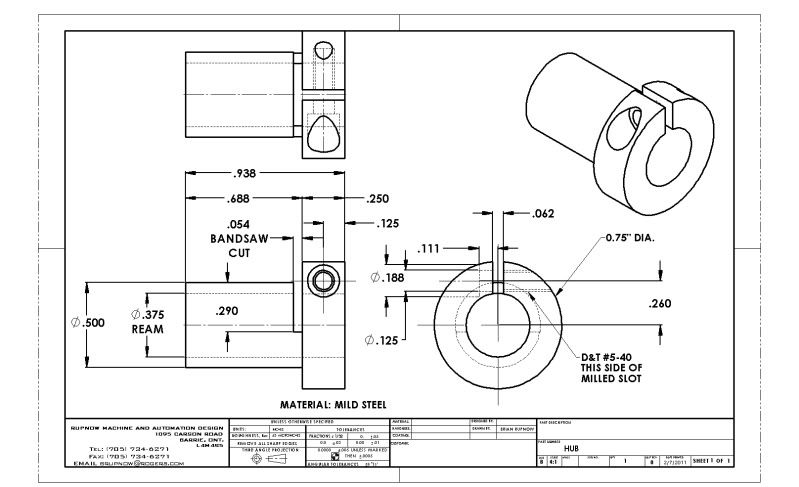
View attachment HUB.PDF