Hi all;
Been wanting to make some things for the new/old Atlas, and now that the engine is done, I'm gettin'
to it.
First thing on the list is a clamp on DI holder so I can attach a DI to the lathe ways. The carriage on
this lathe doesn't have any kind of dial. I keep a few of the cheap China DI's around for projects like
this. Made something similar for my Taig a few years ago.
First step was to dig through the scrap box and find a little chunk of aluminum. It had a hole in it that
wouldn't work out, but that will be taken care of soon.
After milling the edges square, an end mill was used to cut the large slot that will fit on the edge of the
lathe ways.
Then, to take care of that hole, I chucked up a piece of 3/8" al rod in the lathe and turned down an end
that was about .002" over sized for the stray hole. Then mashed it into the hole and cut off the parent
piece, like so.
The other side looks like this, but both sides will be flat, soon enough.
Now the piece is put into the vise in a convenient position so I can get a few operations done in the one
setup. First the end mill is run over the surface to get rid of the nub left from patching the hole, and
then a new hole is bored for the shank on the DI. I used an end mill for this hole, since it was already in
the mill spindle from running the surface on the piece. It was either center drill, drill, and ream, or just
plunge. I took the plunge.
Plunge cuts create strange forces, on any milling machine. Great big machines don't mind quite so
much, but if you are using a small machine and want to plunge cut with an end mill, lock the gibs on the
X and Y to keep from putting the machine through some strange vibrations. It's easier on your nerves,
and the machine will appreciate not having the leadscrew nuts banging on the leadscrews, too.
Then a 1/4" hole is drilled on the center line of the larger slot, and 1/16" from the edge farthest from
it. This will the pinch relief hole. It will let the top of the piece flex when it's tightened down on the lathe
ways. You'll see.
Now a pinch slot is milled from the hole to the cut out for the lathe ways. Now you can see how it can
pinch on lathe ways. The slot is cut all the way through the piece with a 1/8" end mill.
This hole will be for the cap screw that squeezes the top of the piece down on the lathe way. The top
half of the hole is clearance diameter for a #10 screw. The bottom half is drilled for a #10 tap.
Normally, this hole should have been done first, when the piece was fully intact, so the top part of the
clamp wouldn't be smashed down to the lower part of the clamp by the pressure of the drill bit. I just
used a piece of 1/8" inch scrap to keep that from happening. Doing the other steps first was for "ease
of manufacturing", and faster since I had extra milling steps due to the wayward hole in the work piece
that needed plugging.
The top is counterbored a little. It won't take a full C'bore, because the bottom of the head on the
socket head screw would hit the top of the lathe ways, so I just made it a rather deep spot face.
Shop made C'bore.
When the top side of the hole is done, the bottom half is tapped 10-32.
Shop made tap handle, too.
The last step in this piece is to drill and tap the set screw hole to hold the DI shank.
When you tap a hole, it always brings up a little bur, like in the picture above. If you're going to file all
the surfaces, that won't matter so much, but I'm leaving the edges on this "as milled", so the bur needs
to be removed.
The hole is too small for a regular countersink to clean up, so a center drill is used to clean it up. Just
turned lightly between the fingers will usually do the job.
(Put a lead shot down in the hole before the set screw is tightened down on the DI shank.)
And that part is done.
The back of most DI's have some kind of lug. Other wise you would only be able to use it by holding
the shank. Some are like that. This one's not. That lug is just completely in my way! It won't let the
DI set up close to the lathe bed...
So, off with it's head!
These things are held on the back of the DI with four little screws. They are meant to be taken off, so
you can reposition the mounting lug for different mountings. If you want to take one off and look
around in there, go ahead. Nothing will jump out at you.
Now it's ready to go to work.
It can be used to hold the DI and get some kind of readings off the lathe carriage.
It can be used as a regular carriage stop.
Or a piece of 3/8" drill rod can be put in the place of the DI to use as a rod stop for the carriage.
That's all folks. No M&M's this time.
Dean
Been wanting to make some things for the new/old Atlas, and now that the engine is done, I'm gettin'
to it.
First thing on the list is a clamp on DI holder so I can attach a DI to the lathe ways. The carriage on
this lathe doesn't have any kind of dial. I keep a few of the cheap China DI's around for projects like
this. Made something similar for my Taig a few years ago.
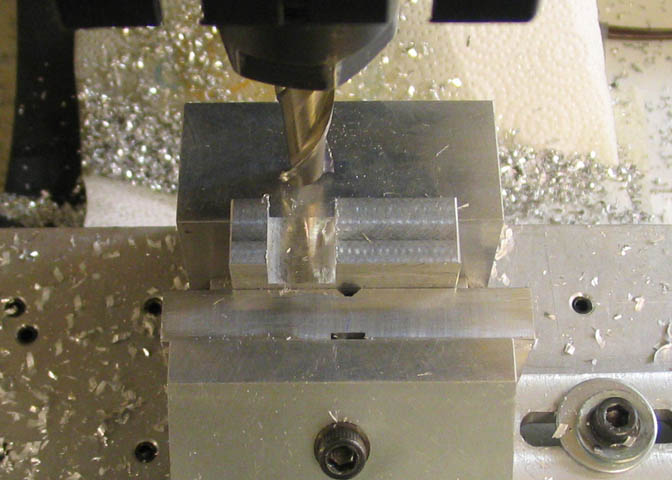
First step was to dig through the scrap box and find a little chunk of aluminum. It had a hole in it that
wouldn't work out, but that will be taken care of soon.
After milling the edges square, an end mill was used to cut the large slot that will fit on the edge of the
lathe ways.
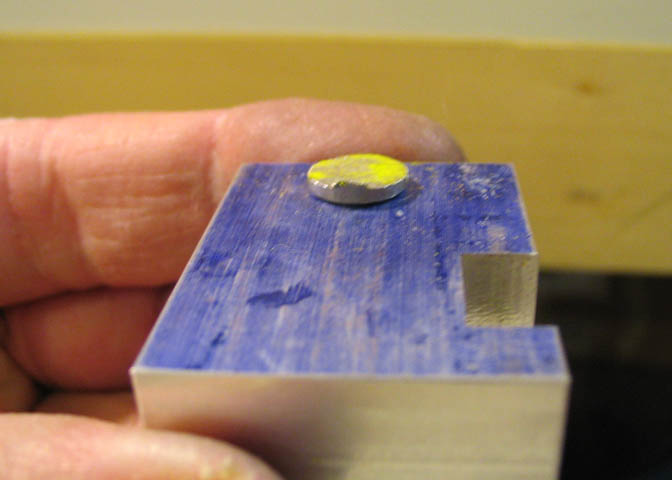
Then, to take care of that hole, I chucked up a piece of 3/8" al rod in the lathe and turned down an end
that was about .002" over sized for the stray hole. Then mashed it into the hole and cut off the parent
piece, like so.
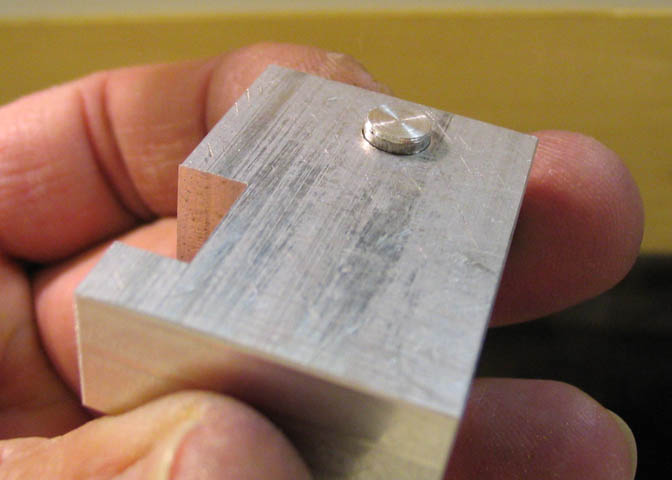
The other side looks like this, but both sides will be flat, soon enough.
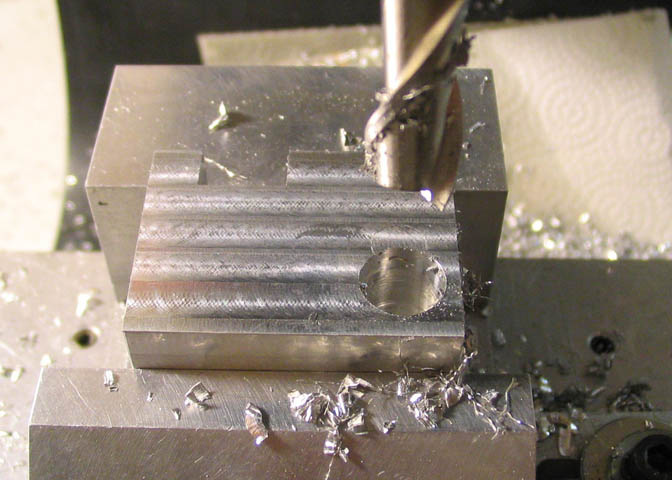
Now the piece is put into the vise in a convenient position so I can get a few operations done in the one
setup. First the end mill is run over the surface to get rid of the nub left from patching the hole, and
then a new hole is bored for the shank on the DI. I used an end mill for this hole, since it was already in
the mill spindle from running the surface on the piece. It was either center drill, drill, and ream, or just
plunge. I took the plunge.
Plunge cuts create strange forces, on any milling machine. Great big machines don't mind quite so
much, but if you are using a small machine and want to plunge cut with an end mill, lock the gibs on the
X and Y to keep from putting the machine through some strange vibrations. It's easier on your nerves,
and the machine will appreciate not having the leadscrew nuts banging on the leadscrews, too.
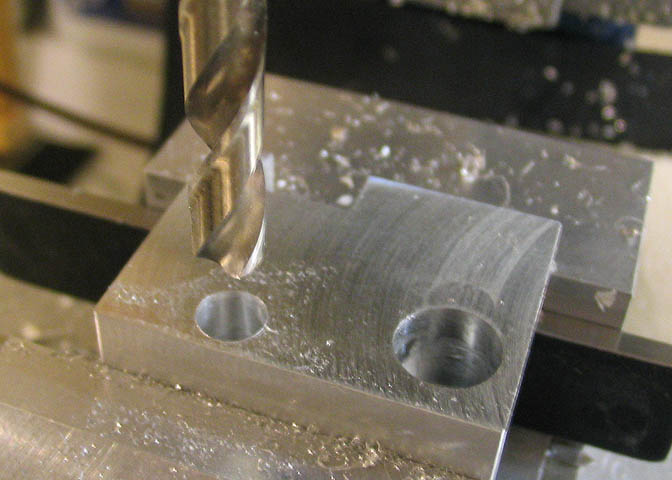
Then a 1/4" hole is drilled on the center line of the larger slot, and 1/16" from the edge farthest from
it. This will the pinch relief hole. It will let the top of the piece flex when it's tightened down on the lathe
ways. You'll see.
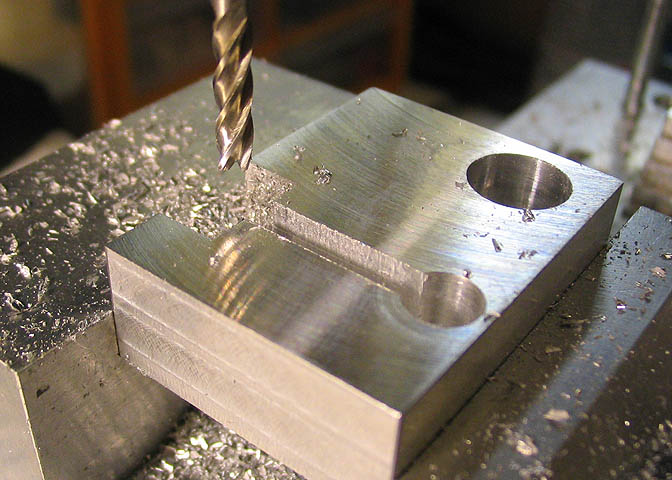
Now a pinch slot is milled from the hole to the cut out for the lathe ways. Now you can see how it can
pinch on lathe ways. The slot is cut all the way through the piece with a 1/8" end mill.
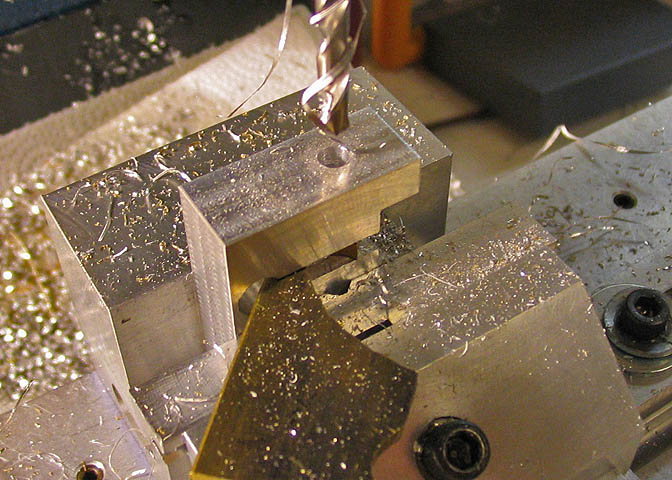
This hole will be for the cap screw that squeezes the top of the piece down on the lathe way. The top
half of the hole is clearance diameter for a #10 screw. The bottom half is drilled for a #10 tap.
Normally, this hole should have been done first, when the piece was fully intact, so the top part of the
clamp wouldn't be smashed down to the lower part of the clamp by the pressure of the drill bit. I just
used a piece of 1/8" inch scrap to keep that from happening. Doing the other steps first was for "ease
of manufacturing", and faster since I had extra milling steps due to the wayward hole in the work piece
that needed plugging.
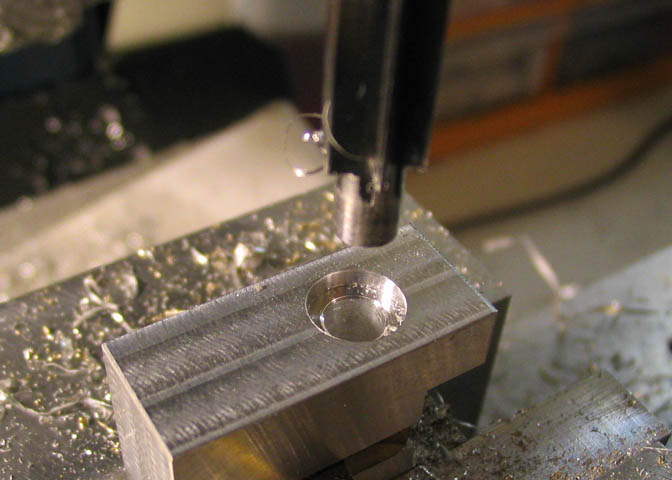
The top is counterbored a little. It won't take a full C'bore, because the bottom of the head on the
socket head screw would hit the top of the lathe ways, so I just made it a rather deep spot face.
Shop made C'bore.
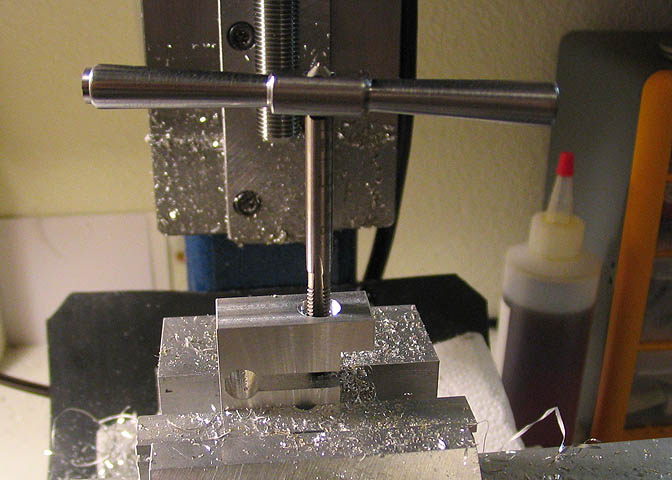
When the top side of the hole is done, the bottom half is tapped 10-32.
Shop made tap handle, too.
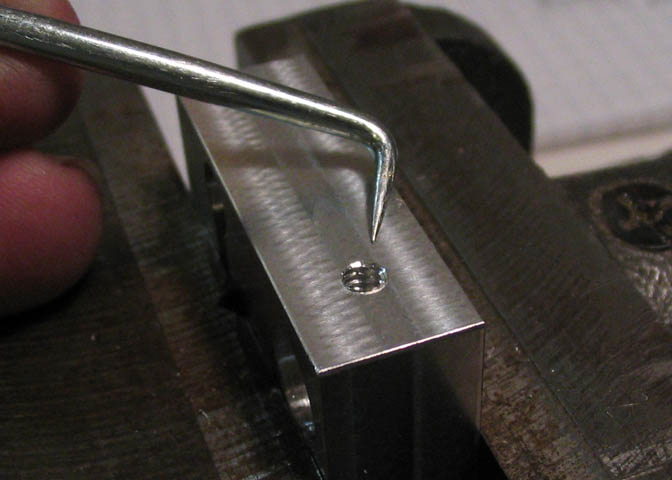
The last step in this piece is to drill and tap the set screw hole to hold the DI shank.
When you tap a hole, it always brings up a little bur, like in the picture above. If you're going to file all
the surfaces, that won't matter so much, but I'm leaving the edges on this "as milled", so the bur needs
to be removed.
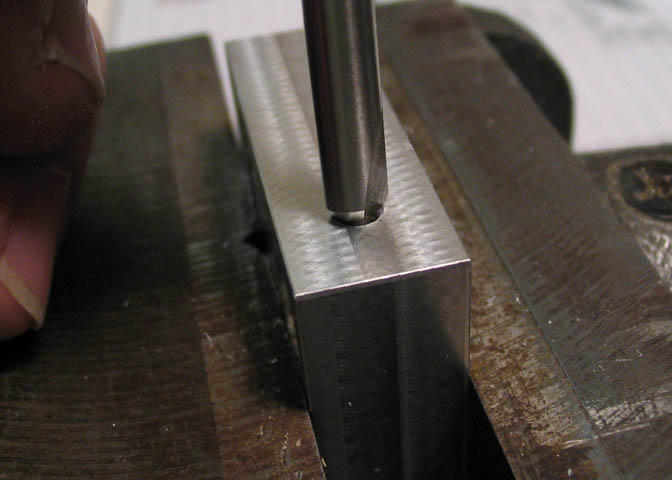
The hole is too small for a regular countersink to clean up, so a center drill is used to clean it up. Just
turned lightly between the fingers will usually do the job.
(Put a lead shot down in the hole before the set screw is tightened down on the DI shank.)
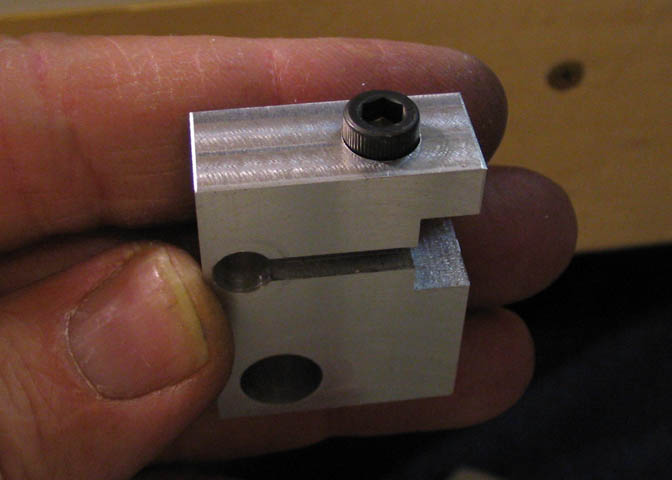
And that part is done.
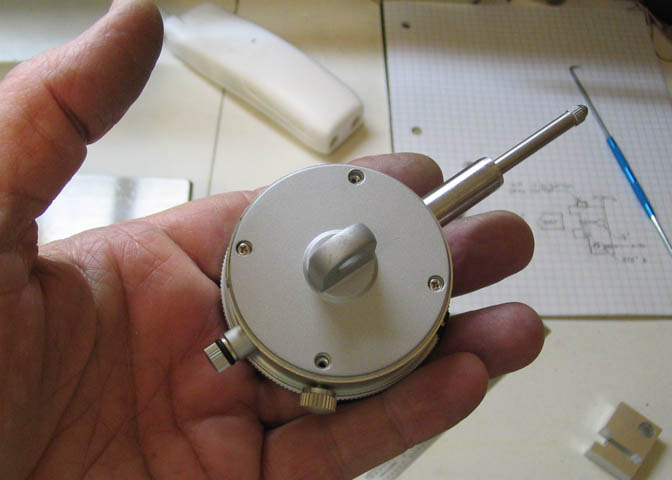
The back of most DI's have some kind of lug. Other wise you would only be able to use it by holding
the shank. Some are like that. This one's not. That lug is just completely in my way! It won't let the
DI set up close to the lathe bed...

So, off with it's head!
These things are held on the back of the DI with four little screws. They are meant to be taken off, so
you can reposition the mounting lug for different mountings. If you want to take one off and look
around in there, go ahead. Nothing will jump out at you.
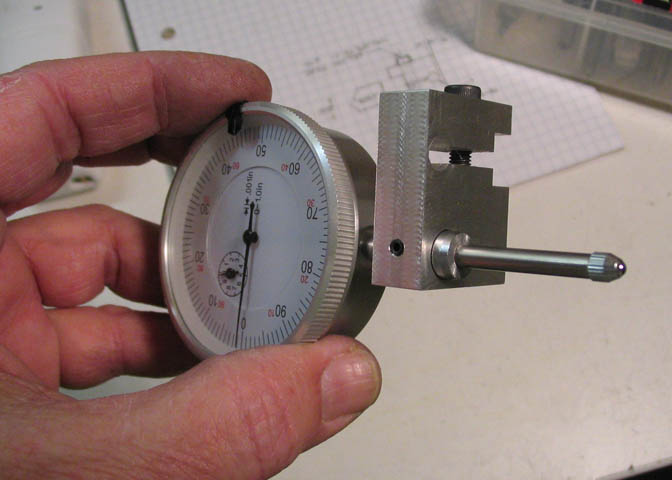
Now it's ready to go to work.
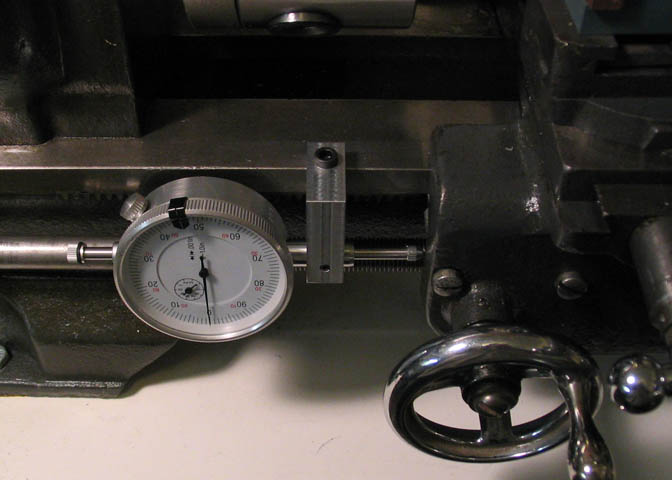
It can be used to hold the DI and get some kind of readings off the lathe carriage.
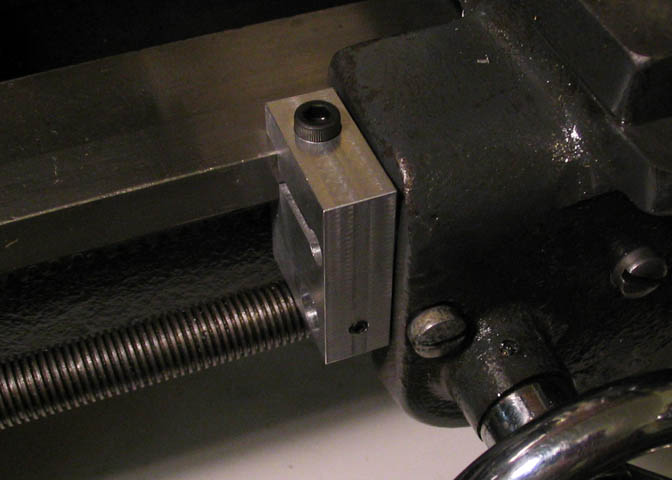
It can be used as a regular carriage stop.
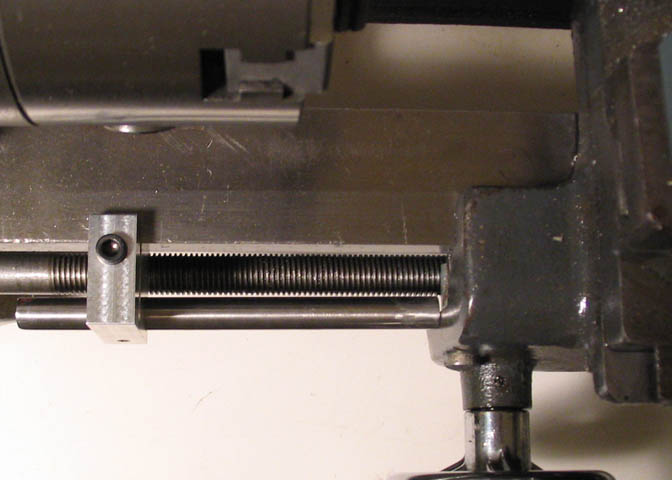
Or a piece of 3/8" drill rod can be put in the place of the DI to use as a rod stop for the carriage.
That's all folks. No M&M's this time.
Dean