- Joined
- Feb 17, 2008
- Messages
- 2,330
- Reaction score
- 445
By way of background for this project, every year for the last 20 years or so a group of us with r famil memembers get tgather in the mountains east of Sllt Lake, UT, USA to play trains and have fun. This is known as the Poison Creek Steamup. The leader of this pack and track owner has a 250 foot loopt of outdoor track consisting of 2 loops of Gauge 1 track with one of the loops being dual gauge for Gauge 3 operation. The track is not powered so all locomotives are steam or IC engine powered with the occasional battery and clockwork power thrown in.
The Name Poison Creek comes from the Poison Creek mining area that is nearby and a lot of narrow gauge railroad operation took place aaround the mines.
I have been making steamup pins for this event for many years on my laser engraver. I use laser engraving stock and engrave and cutout the pin fronts out of laser engravers stock. Then the pin back is glued on and they are ready for wear on caps or steamup aprons. Here is a photo of this years pin.
You will note the "AND BEER FESTIVAL" sub script that I added this year. tI has become tradition that anyone driving brings a six pack or case of beer or ale from thier favorite local micro brewery to share with others. As members of this group come from British Columbia to Florida and points in between it makes for a good variety of engineer lubricant. As the event lasts for 4 days officially and a week or more unofficially no one gets drunk as the actual consumption is spread out over a long period of time.
So now we come to the real purpose of this post. What would be a suitable load for our trains. Well crates of beer or ale of course. So on to construction of wooden crates for beverages.
Gail in NM
The Name Poison Creek comes from the Poison Creek mining area that is nearby and a lot of narrow gauge railroad operation took place aaround the mines.
I have been making steamup pins for this event for many years on my laser engraver. I use laser engraving stock and engrave and cutout the pin fronts out of laser engravers stock. Then the pin back is glued on and they are ready for wear on caps or steamup aprons. Here is a photo of this years pin.
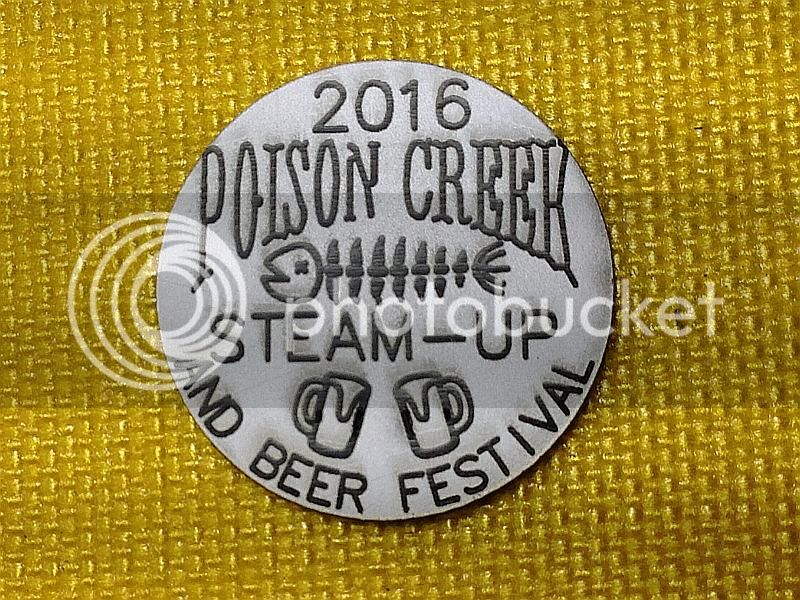
You will note the "AND BEER FESTIVAL" sub script that I added this year. tI has become tradition that anyone driving brings a six pack or case of beer or ale from thier favorite local micro brewery to share with others. As members of this group come from British Columbia to Florida and points in between it makes for a good variety of engineer lubricant. As the event lasts for 4 days officially and a week or more unofficially no one gets drunk as the actual consumption is spread out over a long period of time.
So now we come to the real purpose of this post. What would be a suitable load for our trains. Well crates of beer or ale of course. So on to construction of wooden crates for beverages.
Gail in NM
