kevincoxshall
Member
- Joined
- Feb 20, 2010
- Messages
- 21
- Reaction score
- 0
Today I fixed my lathe to my concrete garage floor. The lathe is a BH600 from warco. I did this because at the higher speeds I noticed it vibrating. I used those coach bolts that don't need a sleeve. I managed to get a total of 5 bolts into the floor. 3 into the headstock end and 2 into the tailstock end.
To move the lathe I used a 4 ft metal bar and some wood to raise the lathe enough so I could place 4mm ply under the stand. This meant the lathe could slide easier. With this lathe the tail stock is very easy to slide but head stock is very heavy. I moved most of the headstock end using leverage. After lots of fiddling to get the machine to line up with the holes I drilled, I realised I could slide the headstock end on the ply wood. Do mind your back if you are trying this. I developed a technique where I hold onto the tray, lean over as much as possible and let your leg do the pushing work.
I used 6mm bolts which are quite small. The reason for this is because there is only 55mm for the length of the bolt. I also used washers. I couldn't get a ratchet spanner to fit in so its a bit fiddly with just a spanner but do-able.
The manual says to do this or use straps if your floor is not level. I wanted a 'hidden' job so i chose this method. I have heard of using resins to fix bolts into the floor. Setting bolts at the time of concreting etc.
Can I ask what everyone else has done?
All comments welcome.
Kevin from Jersey CI
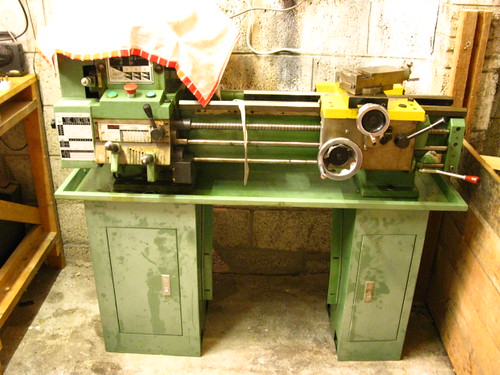
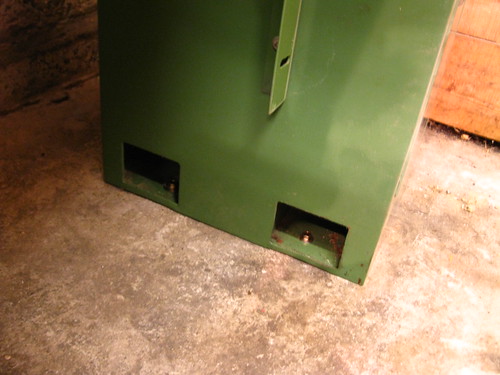
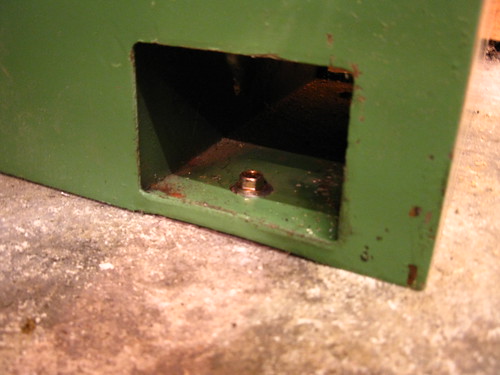
To move the lathe I used a 4 ft metal bar and some wood to raise the lathe enough so I could place 4mm ply under the stand. This meant the lathe could slide easier. With this lathe the tail stock is very easy to slide but head stock is very heavy. I moved most of the headstock end using leverage. After lots of fiddling to get the machine to line up with the holes I drilled, I realised I could slide the headstock end on the ply wood. Do mind your back if you are trying this. I developed a technique where I hold onto the tray, lean over as much as possible and let your leg do the pushing work.
I used 6mm bolts which are quite small. The reason for this is because there is only 55mm for the length of the bolt. I also used washers. I couldn't get a ratchet spanner to fit in so its a bit fiddly with just a spanner but do-able.
The manual says to do this or use straps if your floor is not level. I wanted a 'hidden' job so i chose this method. I have heard of using resins to fix bolts into the floor. Setting bolts at the time of concreting etc.
Can I ask what everyone else has done?
All comments welcome.
Kevin from Jersey CI