I must admit, I haven't put a great deal of science into the design of the exhaust cams on the two engines I have designed from scratch, the "Rupnow Engine" and the "dual opposed piston" engine. With the "Rupnow Engine" I copied the cam profile from the Kerzel hit and miss engine, and I got lucky.---It ran. The dual opposed piston engine runs, but not the way I ultimately want it to. First I am going to tell you what I know. Then we will delve into the arcane science of cam design. So---This I know. When you have built a new 4 cycle engine from scratch, be it from someone else's proven design, or from your own design the first step in setting it up to run is to set the valve timing. The valve is driven either directly or indirectly by a cam, which revolves at 1/2 the speed of the crankshaft. The cam gear is attached to the camshaft, or else it rotates freely on a stub-shaft with the cam attached to the face of the gear, but either way, it meshes with a gear on the crankshaft. The gear on the crankshaft is not keyed in place, but is generally held in place on the crankshaft by one or two set screws. We are only concerned here with rotational movement, not movement parallel to the centerline of the crankshaft. With the cam lobe not providing any lift at all on the valve, use a feeler gauge and set the gap between the end of the valve and the lifter (or rocker arm) at about 0.010". The engine is then rotated by hand in the direction of rotation you want the engine to run. The set screws holding the crankshaft gear are not tightened down at this point. You want the piston to be moving from top dead center towards bottom dead center. About 1/8" before the piston reaches bottom dead center, stop turning the crankshaft. Rotate the crankshaft gear in the same direction with your fingers (it is loose on the crankshaft) and as you do the cam gear will rotate in the opposite direction. When the lobe on the cam just begins to lift the valve pushrod (a point that you can definitely feel, as there is resistance to the valve lifting created by the valve spring), stop and lock down the set screws in the crankshaft gear. Now your valve timing is set. As the piston moves that final 1/8" to bottom dead center, the valve begins to open. As the piston travels from bottom dead center towards top dead center, the exhaust valve will fully open to let any exhaust gas in the cylinder be pushed out thru the exhaust valve to the exhaust pipe. As the piston approaches top dead center, the valve should begin closing, and by the time it reaches top dead center, the valve should be fully closed to begin the intake stroke. This means that the "lifter" has raised up on the leading edge of the cam, skated across the major diameter at the end of the cam, and rode back down the other slope of the cam and returned to the portion of the cam which provides no lift. Now--Here lies the mystery. On low speed engines such as mine, both sides of the cam are a straight line that lean in towards each other at the major diameter area of the cam which provides maximum lift. The secret of just how much they should lean in towards each other is directly related to the number of degrees the crankshaft has to rotate to carry the piston from bottom dead center to top dead center, which should, in theory be exactly 180 degrees. I have set the opposed piston engine up so the valve is opening at the correct time. However, I find that the valve is closing much sooner than it should as the piston travels up the cylinder towards top dead center on its exhaust stroke.--This means I am going to have to come up with a cam profile that has a wider area of "maximum lift" than the profile I am currently using. I hope this is making some sense. If anyone with experience in the development of cam profiles wants to speak up and educate me somewhat on this, I would greatly appreciate it.---Brian
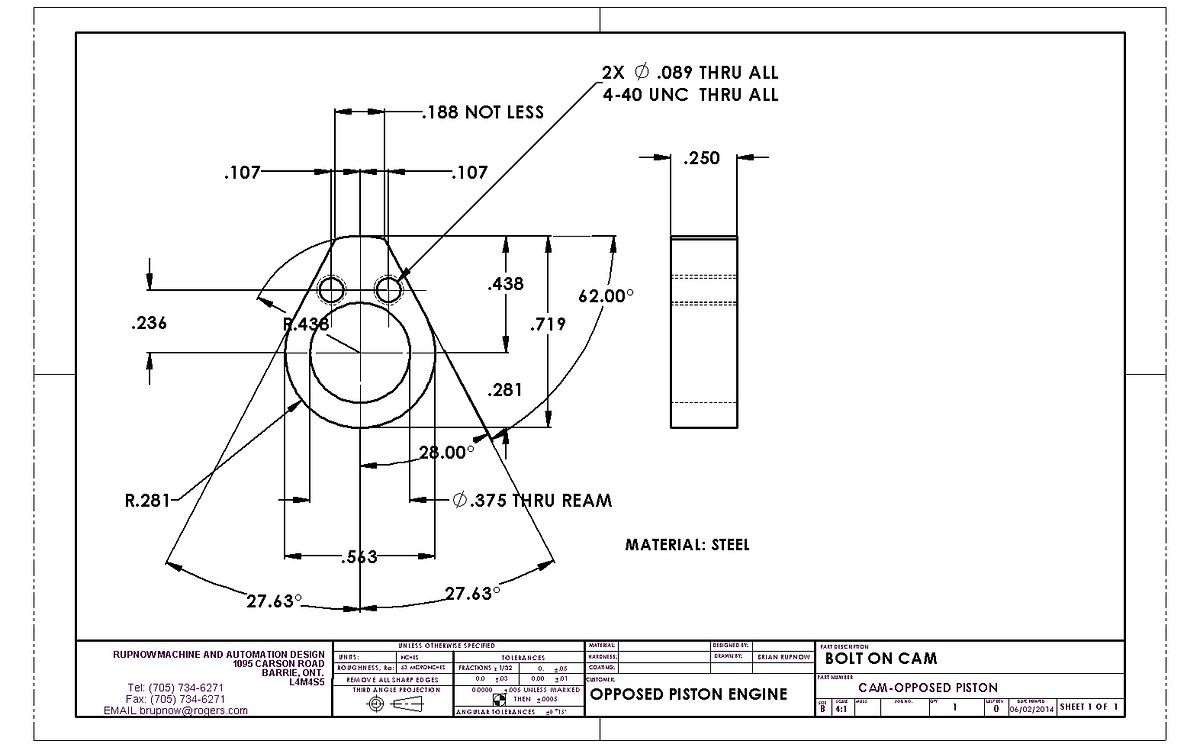
Last edited: