Ken Bartlett
Well-Known Member
- Joined
- Dec 1, 2009
- Messages
- 48
- Reaction score
- 5
I have just recently(as of 2 days ago), brought home my first milling machine, a used Harbor Freight X2. After stripping it down, cleaning, reassembly and setup was done I am ready to start on my first engine. Listing in my head the required tooling I will need to complete the project, I realize that a fly cutter would help in bringing some of the stock down to size and produce a nice surface finish. Are there any suggestion on a easy to make fly cutter that a novice can make. I do have a Harbor Freight 7 x 10 mini lathe as well for the turning work required. Drawings for said fly cutter would be great, as well as recomendations for spindle speed for cutting aluminum with the fly cutter as well. Any and all comments are welcome. Thanks.
My very small corner of our 2 car garage.
http://i208.photobucket.com/albums/bb66/THEBARTLETT/MyShop/12-3-09001.jpg[/img]]
My very small corner of our 2 car garage.
http://i208.photobucket.com/albums/bb66/THEBARTLETT/MyShop/12-3-09001.jpg[/img]]
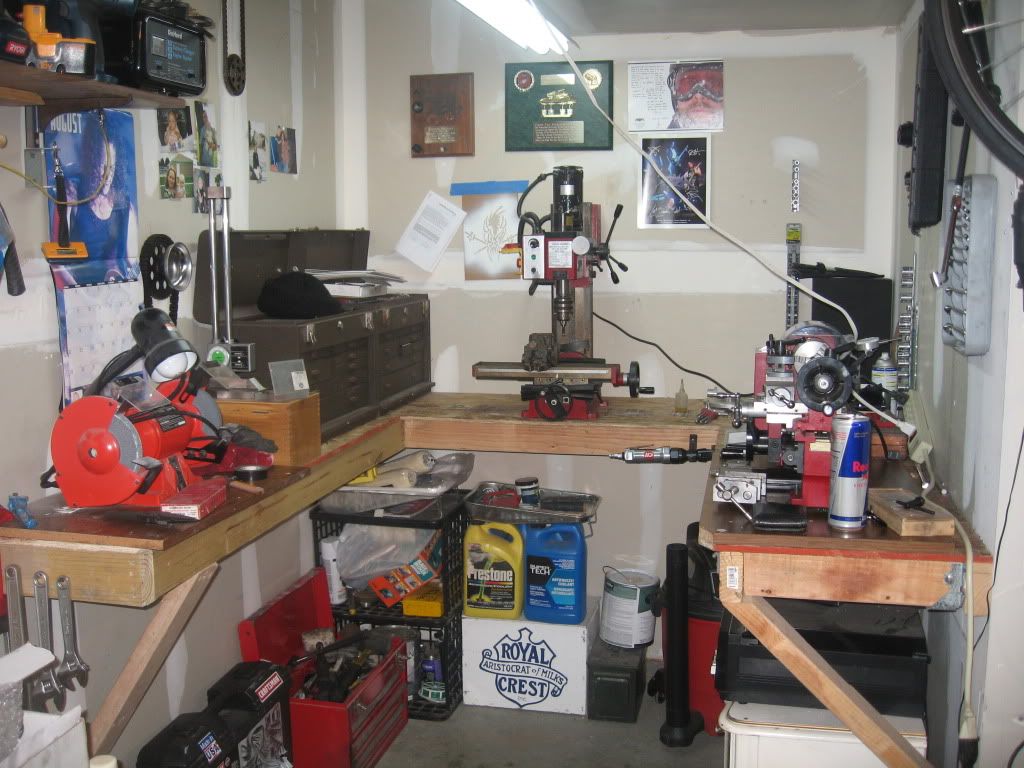