- Joined
- Jul 16, 2007
- Messages
- 3,024
- Reaction score
- 1,100
I was going back through all the old threads I started since joining this forum and realized that I hadn't posted my 302 Ford engine other than to answer someone's question about plans for a V8. The first series of photos are of the block, heads, cam and crank and disassembled on my workbench. First I will give you some background on this build. I first got into gas engines by building hit and miss engines from castings. After seeing some of the multi cylinder engines being built I designed and built my 4 cylinder OHV engine. At the time (mid 80's) I was working for the Ford Motor Company as a metal patternmaker. At the foundry where I worked we made iron castings for the 302 V8 engine. These were the block, heads, intake manifold, exhaust manifolds and water pump. Working in the pattern shop gave me access to the engineering drawings and when word surfaced that the 302 would be phased out I decided to build one. I decided on a scale (3:1) and started making sketches and drawings to create it. This would be a scratch built engine as the process for making castings is quite an undertaking in itself and with the plan to only build one I really didn't need all the extra work. Starting with the block it is made from 6061 aluminum. It has iron sleeves and has a complete water jacket machined into it. This was accomplished by machining out the jacket area and making a head plate to seal everything up. I had good luck doing this on my 4 cylinder so this was the direction I took with the V8. I don't have the amount of time involved in each component but the entire build took over 3 years and approximately 2500 hours. Most of this was because of the extensive hand machining to make all the parts look like the castings.
The only pictures I have of the individual components were taken with a film camera as digital wasn't around at that time, at least not for home use. The front picture of the block shows a boss to the left and above the crank bore. This is for an idler gear to drive the cam. The cam design would be the same as the full sized engine because it was driven by a cam chain so with the intermediate gear both the crank and cam would turn in the same direction.
The block has full oil passages drilled into it and is pressurized by a gear pump as on the full sized engine.
Next comes the heads. They were machined from Durabar or schedule 40 continuous cast iron. This material machines great and when drilling will sometimes give a curl as when machining steel. The main reason for using iron is it eliminates having to put some other material in the head for valve seats. To produce the water passages in the head I layed out an end view of the head with all the porting, head bolts and pushrod holes. The remaining spaces were used to drill passages lenthwise through the head. The steam holes from the block were then drilled up into these passages. The pushrod holes provided a challenge as the full sized heads have a boss cast into the port to provide a wall around the hole. With my ports being round instead of rectangular this became more of a problem. To accomplish what I needed to do I first drilled my ports in and then reamed the pushrod holes oversize to use sleeves in them. The 2 pictures show the rocker side with the exhaust ports and spark plug holes and the combustion chamber side with the holes for the pushrods, head bolts and steam openings.
That's about it for this posting. I don't want to have a problem and lose everything that I've done till now.
gbritnell
The only pictures I have of the individual components were taken with a film camera as digital wasn't around at that time, at least not for home use. The front picture of the block shows a boss to the left and above the crank bore. This is for an idler gear to drive the cam. The cam design would be the same as the full sized engine because it was driven by a cam chain so with the intermediate gear both the crank and cam would turn in the same direction.
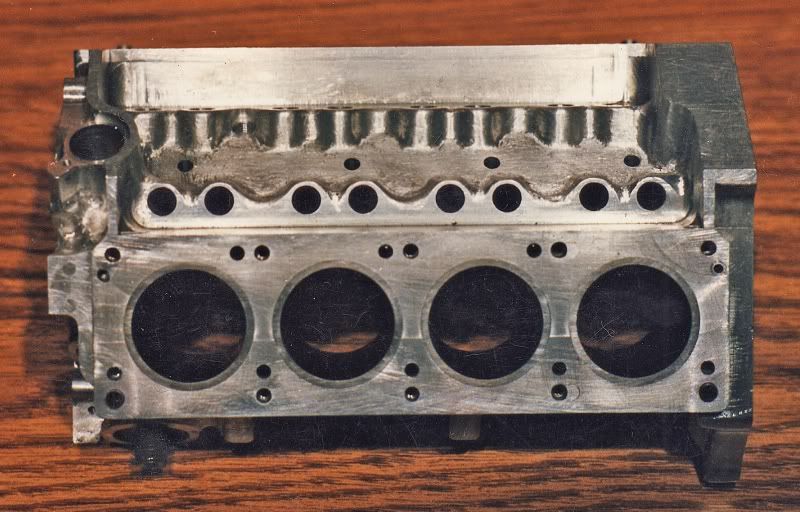
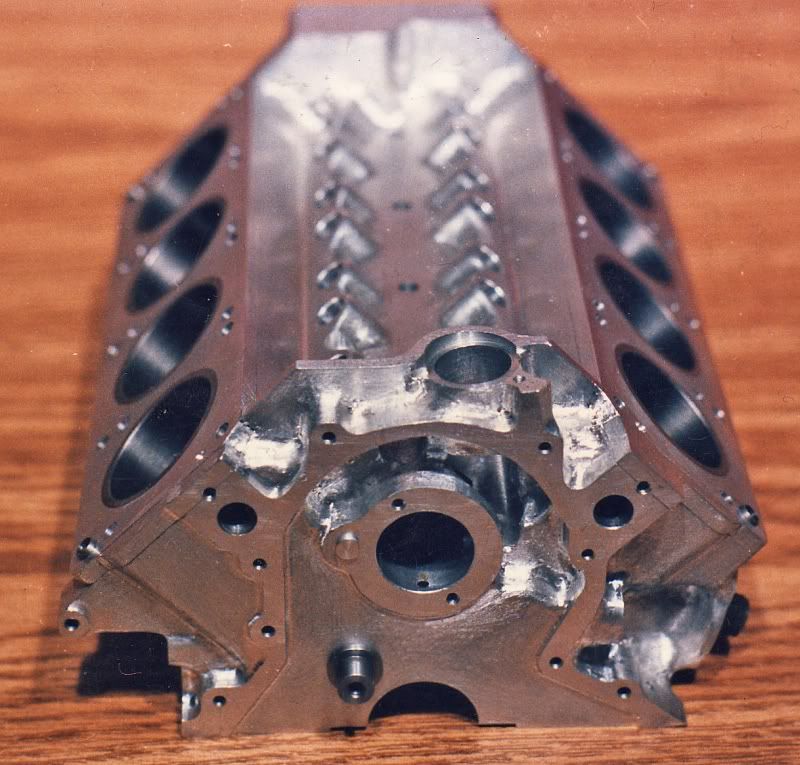
The block has full oil passages drilled into it and is pressurized by a gear pump as on the full sized engine.
Next comes the heads. They were machined from Durabar or schedule 40 continuous cast iron. This material machines great and when drilling will sometimes give a curl as when machining steel. The main reason for using iron is it eliminates having to put some other material in the head for valve seats. To produce the water passages in the head I layed out an end view of the head with all the porting, head bolts and pushrod holes. The remaining spaces were used to drill passages lenthwise through the head. The steam holes from the block were then drilled up into these passages. The pushrod holes provided a challenge as the full sized heads have a boss cast into the port to provide a wall around the hole. With my ports being round instead of rectangular this became more of a problem. To accomplish what I needed to do I first drilled my ports in and then reamed the pushrod holes oversize to use sleeves in them. The 2 pictures show the rocker side with the exhaust ports and spark plug holes and the combustion chamber side with the holes for the pushrods, head bolts and steam openings.
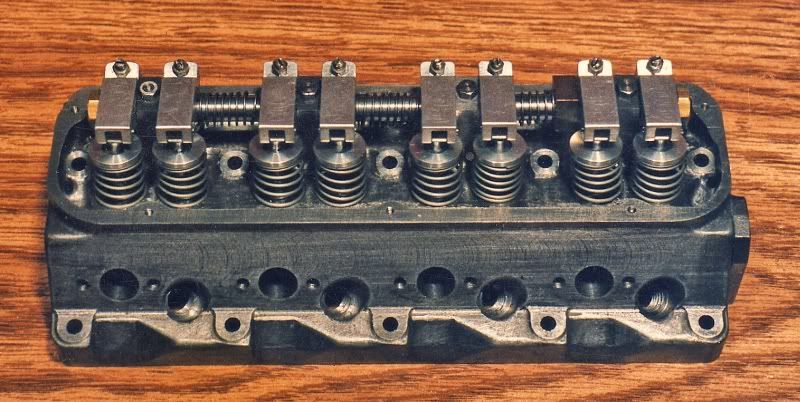
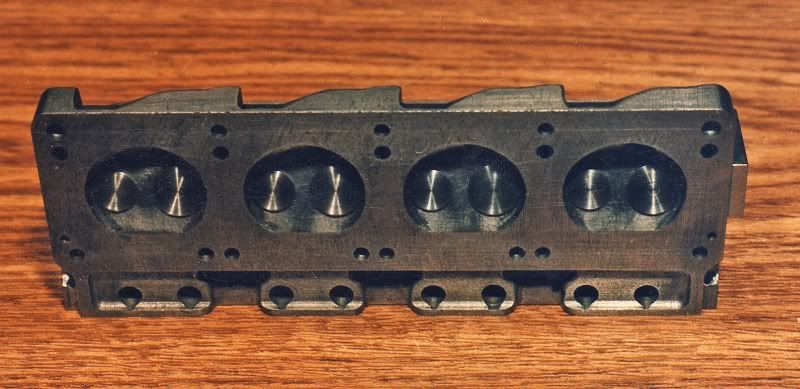
That's about it for this posting. I don't want to have a problem and lose everything that I've done till now.
gbritnell