syrtismajor
Junior Member
- Joined
- Feb 15, 2010
- Messages
- 50
- Reaction score
- 21
Ok, first post here for me. Been a long time browser and lurker but thought I'd finally take the plunge and post something!
This is my first proper model engineering build and is being a steep learning curve. I have never had any training in engineering (other than a 'A' in design technology at school) and my further education and work line is all laboratory based.
This all started four years ago when I was into model steam (Mamod, Wilesco, Jensen etc) and I was tinkering with them. I managed (successfully) to make a double acting slide valve cylinder for a Mamod traction engine using nothing but a drill, files and pure determination.
I was then sold an ageing Emco-Unimat SL1000 (the motor promptly blew and was replaced with a sewing machine motor!) and I started making proper chips.
At that point, someone offered me a project. A LSBC designed 3.5 inch gauge (3/4 scale) American Virginia steam locomotive. All that he had was some part turned driving wheels, part machined cylinders and some rather uniquely dimensioned (read 'slightly not to drawing') frames.
To cut a long story short (and it is a long story!), this is where I am now using my trusty Unimat and a friend with a lathe who bored the cylinders and tread-ed the wheels:
(forgive the clutter)
And here are some components in various stages of manufacture:
The boiler is commercially made (Cheddar models UK) which I bought second hand but unused with certification for 1/4 the cost it should have been. Other than that I have made everything you see there other than the two domes (I got with the boiler), the treads on the wheels and the cylinder bores. The frames were the ones cut by the previous owner but I have reshaped them and they do have a few erroneous holes (but they're well hidden).
And the best bit about all this so far? The chassis runs on air! (well, from a bicycle pump. One pump give about 2/3 turn of the wheels.
My next goal is to find an engineering club and get the boiler properly tested and fired up! And maybe finish the tender...
This is my first proper model engineering build and is being a steep learning curve. I have never had any training in engineering (other than a 'A' in design technology at school) and my further education and work line is all laboratory based.
This all started four years ago when I was into model steam (Mamod, Wilesco, Jensen etc) and I was tinkering with them. I managed (successfully) to make a double acting slide valve cylinder for a Mamod traction engine using nothing but a drill, files and pure determination.
I was then sold an ageing Emco-Unimat SL1000 (the motor promptly blew and was replaced with a sewing machine motor!) and I started making proper chips.
At that point, someone offered me a project. A LSBC designed 3.5 inch gauge (3/4 scale) American Virginia steam locomotive. All that he had was some part turned driving wheels, part machined cylinders and some rather uniquely dimensioned (read 'slightly not to drawing') frames.
To cut a long story short (and it is a long story!), this is where I am now using my trusty Unimat and a friend with a lathe who bored the cylinders and tread-ed the wheels:
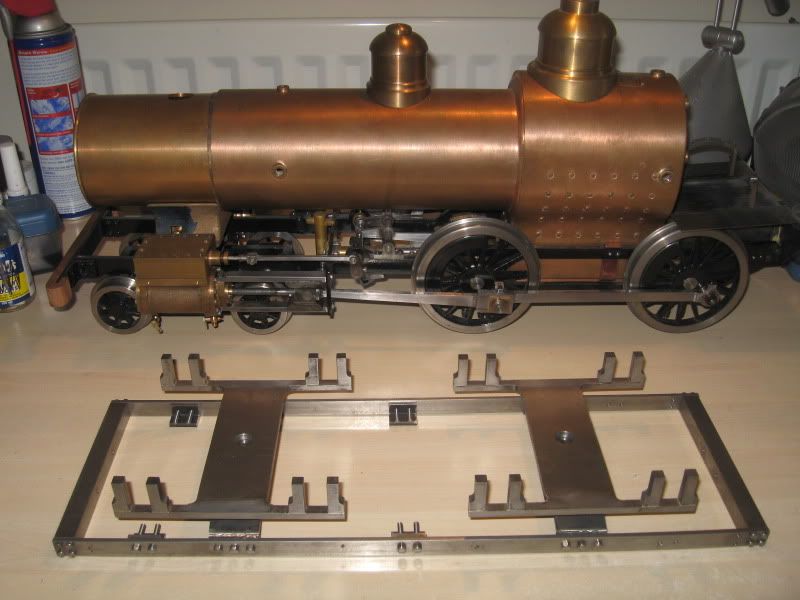
(forgive the clutter)
And here are some components in various stages of manufacture:
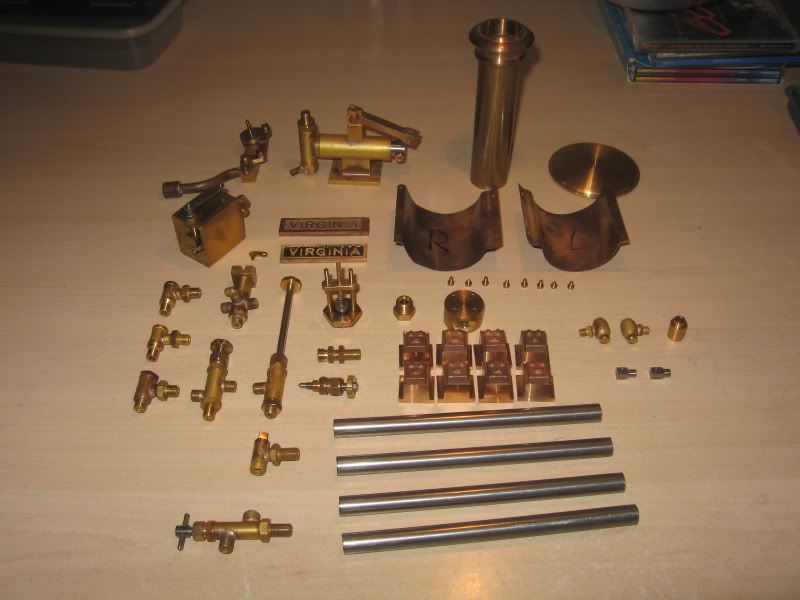
The boiler is commercially made (Cheddar models UK) which I bought second hand but unused with certification for 1/4 the cost it should have been. Other than that I have made everything you see there other than the two domes (I got with the boiler), the treads on the wheels and the cylinder bores. The frames were the ones cut by the previous owner but I have reshaped them and they do have a few erroneous holes (but they're well hidden).
And the best bit about all this so far? The chassis runs on air! (well, from a bicycle pump. One pump give about 2/3 turn of the wheels.
My next goal is to find an engineering club and get the boiler properly tested and fired up! And maybe finish the tender...